Index
Vorwort
Im hohen Norden Finnlands, unter der sengenden Sonne Afrikas,
also unter den gegensätzlichsten Betriebsbedingungen, rollen die
MZ-Motorräder zur Zufriedenheit ihrer Besitzer.
Damit die Fahrzeuge auch nach längerem Betrieb - und der damit
verbundenen Abnutzung - einsatzbereit und zuverlässig bleiben,
geben wir mit dieser Reparaturanleitung die erforderlichen Hinweise
für unsere MZ-Werkstätten im In- und Ausland.
Eine Instandsetzung ist Vertrauenssache in mehrfacher Hinsicht:
Von der zuverlässigen Arbeit des Monteurs hängt
die Sicherheit des Fahrers ab.
Das Erkennen des tatsächlichen Fehlers verhindert unnötigen
Materialeinsatz und verringert den Arbeitsaufwand.
Daraus resultieren 3 Vorteile:
- Keine Nacharbeit,
- kurze Ausfallzeit und
- niedrige Reparaturkosten!
Voraussetzung für eine fachgerechte Reparatur ist, immer
mit den von MZ empfohlenen SpezialWerkzeugen und Hilfsmitteln
zu arbeiten. Besonders die Benutzer von Selbstbedienungswerkstätten
und die Bastler möchten wir nachdrücklich auf diese Empfehlung
hinweisen, damit erheblicher Mehraufwand an Arbeitszeit und
von Materialkosten vermieden wird.
Unsere MZ-Vertragswerkstätten können die Spezialwerkzeuge vom
MZ-Ersatzteilvertrieb beziehen - für die Bastler besteht jedoch nur
die Möglichkeit des Selbstbauens mit Hilfe der im Abschnitt
8.2. gebrachten Skizzen.
Wir hoffen, den Mitarbeitern unserer Vertragswerkstätten im In-
und Ausland sowie den MZ-Freunden in der ganzen Welt mit diesem
Nachschlagewerk die erforderlichen Kenntnisse zu vermitteln
und wünschen viel Erfolg.
VEB MOTORRADWERK ZSCHOPAU
Betrieb des IFA-Kombinats Zweiradfahrzeuge
Abteilung Kundendienst
Inhaltsverzeichnis
1. | Technische Daten |
1.1. | Motor |
1.2. | Vergaser |
1.3. | Elektrische Anlage |
1.4. | Getriebe |
1.5. | Kraftübertragung |
1.6. | Fahrgestell |
1.7. | Massen |
1.8. | Füllmengen |
1.9. | Abmessungen, Meßwerte, Diagramme |
2. | Betriebsmittel |
2.1. | Kraftstoff |
2.2. | Zweitakt-Motorenöl zur Kraftstoff-Öl-Mischung |
2.3. | Ölfüllmenge im Getriebe |
2.4. | Schmiermittel für das Fahrgestell |
2.5. | Stoßdämpferöl - Teleskopgabel |
2.6. | Stoßdämpferöl - Federbeine |
2.7. | Schmiermittel für Unterbrecher |
2.8. | Bremsflüssigkeit |
3. | Demontage des Motors |
3.1. | Vorbereitungsarbeiten |
3.1.1. | Motorrad rechts |
3.1.2. | Vergaserabbau |
3.1.3. | Kupplungsseilzug aushängen bzw. wechseln |
3.2. | Motor zerlegen |
3.2.1. | Vorbereitungen |
3.2.2. | Abbau des Kupplungsdeckels |
3.2.3. | Kupplung und Primärtrieb ausbauen |
3.2.4. | Ausbau der Kickstarteranlage |
3.2.5. | Ausbau der Kupplungsbetätigung |
3.2.6. | Demontage und Montage der Kupplung |
3.2.7. | Abbau der Zylindergruppe |
3.2.8. | Motor-Lichtmaschinenseite demontieren |
3.2.9. | Trennen der beiden Gehäusehälften |
3.2.10. | Ausbau der Schaltung und des Getriebes |
3.2.11. | Herausdrücken der Kurbelwelle |
3.2.12. | Lagerausbau - Getriebelager |
3.2.13. | Abziehen der Lager 6306 von der Kurbelwelle |
3.3. | Reinigung aller Motorenteile |
3.4. | Verschleißuntersüchungen |
3.4.1. | Kupplung und Kupplungsbetätigung |
3.4.1.1. | Primärtrieb |
3.4.1.2. | Zwangsausspurung des Kickstarters |
3.4.2. | Zahnräder, Wellen und Schaltgabeln |
3.4.2.1. | Schaltwelle mit Schaltstück und Schaltanschlag |
3.4.3. | Kurbeltrieb |
3.4.3.1. | Zylinder und Kolben |
3.4.3.2. | Kontrollmessung von Kolben und Zylinder |
3.4.3.3. | Beseitigung eines leichten Kolbenklemmers |
3.4.3.4. | Kolbenringe |
3.4.3.5. | Zylinderdeckel |
3.4.3.6. | Kurbelwelle |
3.4.4. | Gehäuse und Dichtungen |
3.4.5. | Radialrillenlager für Kurbelwelle und Getriebe |
4. | Montage des Motors |
4.1. | Vorbereitungsarbeiten |
4.1.1. | Auswahl von Kolben und Zylinder |
4.1.2. | Regenerierung des Zylinders |
4.1.3. | Auswahl des Nadellagers für den Kolbenbolzen (Neuteile) |
4.1.4. | Lager und Dichtringe |
4.1.5. | Vormontage des Getriebesatzes |
4.1.5.1. | Komplettierung der Antriebswelle (A) |
4.1.5.2. | Komplettierung der Abtriebswelle (B) |
4.1.5.3. | Einsetzen der beiden Getriebewellen in den Montagebehälter 29-50.011 |
4.1.5.4. | Vormontage der linken Gehäusehälfte |
4.2. | Montage der Kurbelwelle, des Getriebes und der Fußschaltwelle |
4.3. | Vormontage der rechten Gehäusehälfte |
4.3.1. | Aufsetzen der rechten Gehäusehälfte |
4.4. | Montage von Kolben, Zylinder und Zylinderdeckel |
4.4.1. | Kolben und Zylinder |
4.4.2. | Zylinderdeckel und Verdichtungsverhältnis |
4.5. | Montage des Primärtriebes |
4.5.1. | Antriebsrad zum Getriebe (68 Zähne) |
4.5.2. | Kupplungsmitnehmer (siehe Bild 21) |
4.5.3. | Axialspiel des Kupplungsmitnehmers messen und einstellen |
4.6. | Aufbau der Kupplung |
4.7. | Kupplungsdeckel komplettieren und montieren |
4.7.1. | Kickstarteranlage montieren |
4.7.2. | Kupplungsbetätigung montieren (siehe Bild 21 und Bild 87) |
4.7.3. | Anbau des Kupplungsdeckels |
4.7.4. | Kupplungsprobeeinstellung |
4.7.5. | Kupplungsfeineinstellung |
4.8. | Antrieb für Drehzahlmesser |
4.9. | Ölverlauf zur Schmierung der Kurbelwellenhauptlager und Wellendichtringe |
4.10. | Schmierung des Getriebes |
4.11. | Montagefehler |
4.12. | Einbau des Motors in das Fahrgestell |
5. | Fahrgestell |
5.1. | Hinterradfederung und elastische Motorlagerung hinten |
5.1.1. | Lagerung der Hinterradschwinge |
5.1.2. | Auswechseln der Gummilagerung - Hinterradschwinge |
5.1.3. | Aus- und Einbau des Schwingenlagerbolzens |
5.1.4. | Montage der hinteren Schwinge einschließlich Motoraufhängung |
5.1.5. | Hintere Motoraufhängung (Bild 91) |
5.1.6. | Federbeininstandsetzung |
5.2. | Motoraufhängung am Zylinderdeckel |
5.3. | Teleskopgabel |
5.3.1. | Lenkungslager |
5.3.2. | Kriterien für die Demontage der Teleskopgabel |
5.3.3. | Ausbau und Einbau der kompletten Teleskopgabel |
5.3.4. | Aus- und Einbau der Teleskopholme (Gabelholme) |
5.3.5. | Demontage der ausgebauten Teleskopholme |
5.3.6. | Montage der ausgebauten Teleskopholme mit Verschleißuntersuchung |
5.3.7. | Funktionsprüfung der Teleskopgabel |
5.4. | Kraftstoffbehälter |
5.5. | Kraftstoffhahn |
5.6. | Hinterradantrieb und Hinterradnabe |
5.6.1. | Hinterradantrieb zerlegen |
5.6.2. | Tachometerantrieb |
5.7. | Radlager wechseln |
5.8. | Bremsen |
5.8.1. | Innenbackenbremse |
5.8.2. | Scheibenbremse für das Vorderrad |
5.9. | Sekundärkette |
5.10. | Auspuffanlage |
5.11. | Räder spuren, Vorderrad auswuchten |
5.12. | Seilzüge |
6. | Elektrische Anlage |
6.1. | Drehstromlichtmaschine (DLM) |
6.2. | Regler |
6.2.1. | Einbau |
6.2.2. | Wartung |
6.2.3. | Einstellung |
6.2.4. | Schäden und ihre Ursachen |
6.3. | Batterie |
6.4. | Zündung |
6.4.1. | Zündspule |
6.4.2. | Unterbrecher |
6.4.3. | Zündeinstellung |
6.4.4. | Zündkerze |
6.4.5. | Zündleitungsstecker (Kerzenstecker) |
6.4.6. | Störungen in der Zündanlage |
6.5. | Licht- und Signalanlage |
6.5.1. | Scheinwerfer |
6.5.2. | Brems-Schluß-Kennzeichen-Leuchte (BSKL) |
6.5.3. | Zündlichtschalter |
6.5.4. | Schalterkombination am Lenker |
6.5.5. | Bremslichtschalter |
6.5.6. | Blinkanlage |
6.5.7. | Signalhorn |
6.5.8. | Stromlaufplan und Schaltplan |
6.6. | Instrumente und Kontrolleuchten |
7. | Ansaugsystem |
7.1. | Beschreibung und Funktion der Anlage |
7.1.1. | Luftfilter |
7.1.2. | Ansauggeräuschdämpfer |
7.1.3. | Anschlußstück zum Vergaser |
7.1.4. | Vergaser |
7.1.5. | Ansaugstutzen |
7.2. | Fehlersuche |
7.2.1. | Abmagerung |
7.2.2. | Überfettung |
8. | Spezialwerkzeuge |
8.1. | Verzeichnis der Spezialwerkzeuge |
8.2. | Zeichnung für Spezialwerkzeuge |
9. | Anzugsmomente - Motor |
10. | Anzugsmomente - Fahrgestell |
|
Bild 1. ETZ 250 mit Scheibenbremse
Bild 2. ETZ 250 mit Trommelbremse in Standardausführung
Bild 3. Explosivdarstellung Motor EM 250
1. Technische Daten
1.1. Motor
nächster Punkt ; Index
Motortyp | EM 250 |
Arbeitsweise | Zweitakt-Umkehrspülung |
Kühlungsart | Luft (Fahrtwind) |
Zylinderanzahl | 1 |
Hub / Bohrung | 65 mm / 69 mm |
Hubraum | 243 cm³ |
Verdichtungsverhältnis | 10,5:1 |
Verdichtungsraum des Zylinderdeckels (im montierten Zustand) | etwa 26 cm³ |
Max. Leistung bei etwa 5500 U/min | 15,5 Kw (21 PS) |
Max. Drehmoment bei etwa 5200 U/min | 27,4 Nm (2,8 kpm) |
Schmierung | Mischungsschmierung 50:1 (oder für ausgewählte Exportländer mittels Öldosierpumpe) |
Pleuellager | Käfiggeführtes Nadellager für Hubzapfen und Kolbenbolzen |
Kurbelwellenhauptlager | 2 Lager 6306 C4f 1 Lager 6302 C4f |
Schmierung der Hauptlager | Mischungsschmierung |
Steuerwinkel |
Ansaugen | 155° Kurbelwinkel |
Überströmen | 123° Kurbelwinkel |
Auspuff | 180° Kurbelwinkel |
|
1.2. Vergaser
nächster Punkt ; Index
Vergaser | BVF 30 N 2-5 |
Durchlaß | 30 mm |
Hauptdüse | 130 |
Nadeldüse | 70 (mit Querbohrung) |
Teillastnadel | C6 mit 5 Kerben |
Nadelstellung von oben | 3...41) (4 für die Einfahrzeit) |
Startdüse | 90 |
Leerlaufdüse | 45 |
Schwimmerventil | 20 |
Leerlaufluftschraube | etwa 1 Umdrehung offen |
Drosselschieber-Schieberausschnitt | 6 mm |
|
1.3. Elektrische Anlage
nächster Punkt ; Index
Zündung | Batteriezündung |
Zündzeitpunkt | 3,0-0,5 mm vor OT = 22°15'-2° Kurbelwinkel |
Unterbrecherkontaktabstand | 0,3+0,1 mm |
Zündkerze | M 14-260 |
Elektrodenabstand | 0,6 mm |
Lichtmaschine | 12 V, 210 W, Drehstrom |
Gleichrichter | Siliziumhalbleiter in 3-Phasen-Brückenschaltung |
Regler | Einsystem-Regler, temperaturkompensiert, plusregelnd |
Batterie | 12 V, 9 Ah |
Zündspule | 12 V Kleinzündspule |
Scheinwerfer | Lichtaustritt 170 mm Durchmesser, asymmetrisches Abblendlicht |
Brems-Schluß-Kennzeichenleuchte | Lichtaustritt 120 mm Durchmesser |
Signalhorn | unter Kraftstoffbehälter |
Fahrtrichtungsanzeige | 4-Leuchten-Blinkanlage |
Schalter |
Zündlichtschalter | im Instrumentenhalter |
Schalterkombination am Lenker | Abblendschalter Fahrtrichtungsanzeige Signalhorn Lichthupe |
Bremslichtschalter | in Hinterradnabe und Vorderradnabe oder Hauptbremszylinder |
Glühlampen |
Scheinwerfer | 12 V, 45/40 W (Bilux) TGL 11413 |
Standlicht | 12 V, 4 W Sockel BA 9s TGL 10833 |
Bremslicht | 12 V, 21 W Sockel BA 15s TGL 10833 |
Fahrtrichtungsanzeige | 12 V, 21 W Sockel BA 15s TGL 10833 |
Rücklicht | 12 V, 5 W Sockel BA 15s TGL 10833 |
Ladekontrolle | 12 V, 2 W Sockel BA 7s TGL 10833 |
Leerganganzeige | 12 V, 2 W Sockel BA 7s TGL 10833 |
Fernlichtkontrolle | 12 V, 2 W Sockel BA 7s TGL 10833 |
Kontrolle der Fahrtrichtungsanzeige | 12 V, 2 W Sockel BA 7s TGL 10833 |
Tachometerbeleuchtung | 12 V, 2 W Sockel BA 7s TGL 10833 |
Sicherungen |
Hauptsicherung (2 Stück) | Schmelzeinsatz 16 A |
Fahrtrichtungsanzeige | Schmelzeinsatz 4 A |
Lichtmaschine (Leitung DP) | Feinsicherung 2 A |
|
1.4. Getriebe
nächster Punkt ; Index
Kupplung | auf dem linken Kurbelwellenstumpf - im Ölbad (5 Reibscheiben mit Korkanteilen) |
Schaltung | Fußschaltung |
Anzahl der Gänge | 5 |
Getriebeabstufung |
1. Gang | 3,0 : 1 | = | 12 : 36 |
2. Gang | 1,865 : 1 | = | 15 : 28 |
3. Gang | 1,333 : 1 | = | 18 : 24 |
4. Gang | 1,048 : 1 | = | 21 : 22 |
5. Gang | 0,87 : 1 | = | 23 : 20 |
|
1.5. Kraftübertragung
nächster Punkt ; Index
Übersetzung |
Motor - Getriebe | 2,43 : 1 |
durch schrägverzahnte Stirnräder | 28 : 68 Zähne |
Übersetzung |
Getriebe - Hinterrad | 19 : 48 Zähne = 1 : 2,53 (Solobetrieb) 15 : 48 Zähne = 1 : 3,2 (Seitenwagenbetrieb) |
durch Rollenkette | 0,8 B-1-130 TGL 11796 (12,7mm x 7,75mm x 8,51mm, 130 Rollen) für Solobetrieb
0,8 B-1-128 TGL 11796 (12,7mm x 7,75mm x 8,51mm, 128 Rollen) für Seitenwagenbetrieb |
Gesamtübersetzung |
1. Gang | 18,406 : 1 |
2. Gang | 11,453 : 1 |
3. Gang | 8,181 : 1 |
4. Gang | 6,428 : 1 |
5. Gang | 5,335 : 1 |
|
1.6. Fahrgestell
nächster Punkt ; Index
Rahmen | Zentralrohrrahmen (geschweißtes Rechteck-Profil) |
Motoraufhängung (elastisch) | am Zylinderdeckel und am Gehäuse hinten |
Lenkungswinkel | 63 Grad |
Nachlauf | 95 mm |
Art der Federung |
vorn | Teleskopgabel mit ölhydraulischer Dämpfung Federweg 185 mm |
hinten | Federbeine mit ölhydraulischer Dämpfung Federvorspannung verstellbar, Federweg 105 mm |
Räder | Drahtspeichenräder mit ungekröpften Speichen |
Felgengröße |
vorn | 1,60 x 18 |
hinten | 2,15B x 18 |
Bereifung |
vorn | 2,75 - 18 |
hinten | 3,50 - 18 |
Reifenluftdruck |
Solo: vorn | 150 kPa (1,5 kp/cm²) |
hinten | 190 kPa (1,9 kp/cm²) |
Mit zulässiger Gesamtmasse: |
vorn | 170 kPa (1,7 kp/cm²) |
hinten | 250 kPa (2,5 kp/cm²) |
Bremsen |
vorn | Trommelbremse, Durchmesser 160 mm, Belagbreite 30 mm, Betätigung mit Seilzug
oder hydraulische Ein-Scheiben-Festsattel-Bremse, Bremsscheibendurchmesser 280 mm |
hinten | Trommelbremse, Durchmesser 160 mm, Belagbreite 30 mm, Betätigung mit Gestänge |
|
1.7. Massen
nächster Punkt ; Index
Leermasse (mit Kraftstoff und Werkzeug) | 151 kg (Ausführung mit Trommelbremse vorn) 153 kg (Ausführung mit Scheibenbremse vorn) |
zulässige Gesamtmasse | 330 kg |
|
1.8. Füllmengen
nächster Punkt ; Index
Getriebe | 1000 cm³ Getriebeöl SAE 80 |
Kraftstoffbehälter | 17 l Kraftstoff-Öl-Mischung, davon 1,5 l Reserve |
Ölbehälter für Öldosieranlage | 1,3 l |
Teleskopgabel | je Holm 230 cm³ Dämpfungsflüssigkeit |
|
Bild 4. Vollastkennlinien des Motors EM 250
Bild 5. Drehzahl-Gang-Diagramm ETZ 250 - Solo
Bild 5a. Drehzahl-Gang-Diagramm ETZ 250 - Seitenwagenausführung
2. Betriebsmittel
2.1. Kraftstoff
nächster Punkt ; Index
Entsprechend der konstruktiven Auslegung des Motors
ist ein Vergaserkraftstoff mit einer Oktanzahl ROZ von mindestens
88 zu verwenden (in der DDR Kurzbezeichnung "VK 88").
Außerhalb der DDR wird ein Kraftstoff mit ähnlicher Oktanzahl
empfohlen.
|
2.2. Zweitakt-Motorenöl zur Kraftstoff-Öl-Mischung
nächster Punkt ; Index
Das Motorenöl für Zweitaktmotoren wird in einem
Verhältnis von 1 : 50
dem Kraftstoff beigemischt (z.B. 0,2 Liter Zweitakt-Motorenöl
auf 10 l Kraftstoff).
Das Mischungsverhältnis 1 : 50 gilt auch während
der Einfahrzeit.
Beide Pleuellager, die Zylinderlaufbahn, der Kolben
und die Kurbelwellenhauptlager 6306 werden durch diese
einfache und betriebssichere Mischungsschmierung mit
Öl versorgt. Unsere jahrelangen Erprobungen veranlassen
uns, die Verwendung von
Zweitaktmotorenöl MZ 22
innerhalb der DDR vorzuschreiben. Dieses legierte
Zweitaktöl erfüllt folgende technische Forderungen:
Viskosität bei 50 °C | 20 ... 25 cSt |
Stockpunkt höchstens | -30 °C |
Es enthält Zusätze (Additives), die hohe Temperatur-
und Druckbeständigkeit bewirken. Geringe Neigung zur Ölkohlebildung;
verhindert bzw. löst den Ölkohleansatz. Verschleißmindernde und
korrosionsschützende Eigenschaften. Enthält Bleiausträger, welche
die Brückenbildung an Zündkerzen verhindern.
Für die außerhalb der DDR laufenden MZ-Motorräder empfehlen
wir, ebenfalls nur Zweitakt-Motorenöle zu verwenden, die diese
Eigenschaften besitzen (z.B. Shell 2 T, Castrol 2 T, Aral 2 T,
Mixol "S", LT-2T usw.).
|
2.3. Ölfüllmenge im Getriebe
nächster Punkt ; Index
Für das Getriebe und den Primärantrieb sind 900 cm³
Getriebeöl "GL 60" erforderlich.
Hierbei handelt es sich um ein legiertes Getriebeöl,
das zur Schmierung von Schalt- und Achsgetrieben geeignet
ist. Es ist ein alterungsbeständiges Schmierölraffinat
mit Zusätzen zur Erhöhung des Druckaufnahmevermögens
und zur Verschleißminderung.
Es hat ein günstiges Kälteverhalten und erfüllt unter
anderem folgende technische Forderungen:
Viskosität bei 50 °C | 53 ... 68 cSt (entspricht etwa 8 °E) |
Stockpunkt höchstens | -25 °C |
Flammpunkt | 180 °C |
Wassergehalt | 0,1 % |
Außerhalb der DDR ist Motorenöl SAE 30...40
oder Getriebeöl SAE 80 mit gleichen Eigenschaften zu
verwenden.
|
2.4. Schmiermittel für das Fahrgestell
nächster Punkt ; Index
Mit Wälzlagerfett "Ceritol +k2" oder
"Ceritol +k3" werden folgende Schmierstellen des
Fahrgestells geschmiert:
Lenkungslager, Radlager, Lager für Hinterradantrieb,
Sekundärkette, Bremsnocken- und Bremsbackenlagerung,
Fußbremswelle und Tachometerantrieb (die beiden letzteren
nur bei Montage bzw. Instandsetzung).
Dieses Wälzlagerfett hat einen Tropfpunkt von etwa
130...150 °C, ist einsetzbar von -20...+100 °C und
wasserbeständig bei +50 °C.
Außerhalb der DDR ist ein Wälzlagerfett mit
ähnlichen Kennwerten zu verwenden.
|
2.6. Stoßdämpferöl - Federbeine
nächster Punkt ; Index
Es wird nur Stoßdämpferöl ohne Zusätze
mit oben bezeichneter Viskosität verwendet. Die Dämpfungswerte
der Teleskopgabel und der Federbeine sind auf diese Viskosität
abgestimmt. Bei der Verwendung von Stoßdämpferöl anderer
Viskosität verschlechtern sich die Federung und die
Fahreigenschaften.
|
2.8. Bremsflüssigkeit
nächster Punkt ; Index
Für die Scheibenbremse ist Bremsflüssigkeit
"Karipol grün" bzw. im Ausland eine Bremsflüssigkeit
SAE 70 R3 oder SAE J 1703 (für Scheibenbremsen) zu verwenden.
|
3.1. Vorbereitungsarbeiten
nächster Punkt ; Index
Zweckmäßig ist es, vor Beginn der Arbeiten die
Batterie abzuklemmen und auszubauen. Sie kann während der
Montagearbeiten gepflegt werden. Wird das Motorrad in der
Werkstatt abgestellt, sind die beiden Sicherungen vom
Sicherungssockel unter der rechten Verkleidung zu
entfernen.
Während der nachfolgenden Arbeiten kann das Öl aus dem
Getrieberaum ablaufen (Öffnen der Ölablaßschraube (2)
und Herausschrauben der unteren Befestigungsachraube
(1) des Kupplungsdeckels).
Achtung: Die Schaltarretierschraube (3) dient
nicht zum Ölablassen!
|
Bild 6. Ablassen des Schmiermittels von Getriebe- und Kupplungsraum
3.1.1. Motorrad rechts
nächster Punkt ; Index
Auf der rechten Seite des Motorrades beginnen
die Arbeiten mit dem Abbau der Auspuffanlage:
- Überwurfmutter am Zylinder mit Hakenschlüssel,
- Auspuffklemmschelle vorn am Motor (SW 13),
- Haltestrebe am Schalldämpfer hinten (SW 13) und
- Lichtmaschinendeckel entfernen (Innensechskant SW 5).
|
Bild 7. Motorrad rechts
Nachdem die Kabel (1) abgezogen wurden, den
Bürstenhalter (2) abschrauben. Der Stator kann nach dem
Lösen der Befestigungsschrauben (3) abgenommen werden.
Ein Ringschlüssel (SW 13) dient zum Lösen der Befestigungsschraube
des Nockens der Lichtmaschine. Drehrichtung des Schlüssels
entgegen der Laufrichtung des Motors. Der Nocken läßt sich
danach durch leichtes Rütteln an der Befestigungsschraube
(Gewinde M7) abziehen.
|
Bild 8. Ausbau des Stators der Lichtmaschine
Die Abdrückschraube 02-MW 39-4 (1) löst
den Rotor vom Konus der Kurbelwelle (Prellschlag mit
der Hand auf den Knebel in Drehrichtung des Motors).
Für den Bastler genügt eine Sechskantschraube M 10x100 mm.
|
Bild 9. Rotor der Lichtmaschine abdrücken
Den Verschluß der Sekundärkette mit Flach- oder
Kombinationszange vorn am Kettentad der Abtriebswelle öffnen.
Danach die Kettenschutzschläuche mit der Kette nach hinten
vom Motor abziehen.
3.1.2. Vergaserabbau
nächster Punkt ; Index
Der Vergaser wird erst abgebaut, nachdem der
Kraftstoffhahn geschlossen und der Kraftstoffschlauch abgezogen
wurden.
Reihenfolge des Vergaserabbaues:
- Gummischutzkappe hochziehen und darunterliegende
Startvergaserbetätigung (SW 14) herausschrauben
- Vergasergehäusekappe abschrauben und mit Kolbenschieber
herausziehen
- Klemmverbindung Vergaser-Ansaugrohr lösen (Schraubendreher)
- Zwei Muttern (SW 10) der Ansaugstutzenbefestigung lösen
|
Bild 10. Vergaserabbau
Den Vergaser mit dem Ansaugstutzen von den
Stiftschrauben am Zylinder abziehen, nach links herausschwenken
und aus dem Ansaugrohr (Gummi) herausziehen.
3.1.3. Kupplungsseilzug aushängen bzw. wechseln
nächster Punkt ; Index
Schutzkappe (Gummi) vom Gehäuse zur Seilzugaufnahme
(2) abheben, am Bowdenzug hochschieben und Stecknippel (1)
herausnehmen.
Gehäuse für Seilzugaufnähme (2) vom Kupplungsdeckel abschrauben
(SW 19) und am Seilzug etwa 5 cm hochschieben, erst jetzt kann
das Nippel (4) des Bowdenzuges aus der Zugspindel ausgehangen
werden.
Bei der Ausführung "de Luxe" ist vor dem Motorausbau
noch die Antriebswelle für Drehzahlmesser abzuschrauben.
|
Bild 11. Kupplungsseilzug
Bild 12. Motorausbau oder Wechseln des Zylinders
Motorausbau:
- Zwei Muttern (SW 13) (1) mit Wellscheiben von
den Stehbolzen des Zylinderdeckels entfernen.
Dabei den Motor unten abstützen;
- Zwei Befestigungsschrauben (2) des Motors an
den Motorschuhen hinten herausschrauben
(SW 13);
- Den nach unten abgekippten Motor nach vorn
herausziehen.
Zylinderwechsel:
Der Zylinderdeckel, der Zylinder und die elastische
Motoraufhängung können ebenfalls in der im Bild
12 gezeigten Montagestellung gewechselt
werden.
Für den Zylinderwechsel ist das elektrische Signalhorn
(1) und der Kraftstofftank zu entfernen. Zum Wechsel des
Kraftstofftanks siehe Abschnitt 5.4.
|
3.2. Motor zerlegen
3.2.1. Vorbereitungen
nächster Punkt ; Index
Die äußerliche Reinigung des ausgebauten Motors
halten wir für selbstverständlich, ehe er endgültig zerlegt
wird. Ebenso selbstverständlich ist es, daß alle Teile so
abgelegt oder untergebracht werden, daß nichts verloren
geht oder Schaden erleidet.
Bevor der Motor in die Motoren-Montagevorrichtung eingehangen
wird, werden die Klemmschraube (SW 13) vorn und die darunter
liegende Paßhülse mit Schlagdorn 11 MW 3-4 entfernt.
|
3.2.2. Abbau des Kupplungsdeckels
nächster Punkt ; Index
Fußschalthebel (1) nach dem Lockern der Klemmschraube
mit Mutter (SW 10) abnehmen. Die Kickstarterkurbel verbleibt am
Motor und wird komplett mit dem Kupplungsdeckel abgezogen.
Das Gehäuse für Drehzahlmesserantrieb (2) abnehmen. Danach
die darunterliegende Stellplatte und das Antriebsrad für
Drehzahlmesser (SW 22) demontieren.
Nach dem Entfernen der 5 Befestigungsschrauben des Kupplungsdeckels
an den Punkten (3) durch abwechselndes Klopfen mit Plast- oder
Gummihammer den Kupplungsdeckel komplett mit Kickstarteranlage
abheben.
|
Bild 13. Kupplungsdeckel abnehmen
3.2.3. Kupplung und Primärtrieb ausbauen
nächster Punkt ; Index
Den Kupplungsabzieher (1) voll auf das Abzugsgewinde
der Kupplung (2) aufschrauben. Die Spindel (3) drückt die
Kupplung vom Konus der Kurbelwelle ab. Kupplung von innerem
Mitnehmer herunterziehen. Wellscheibe (5) und Anlaufscheibe
(4) abnehmen, Antriebsrad mit innerem Mitnehmer (3) und
Nadellager (2) sowie Distanzscheibe (1) von Kurbelwelle
abnehmen (siehe Bild 21).
|
Bild 14. Kupplung abziehen
Nach dem Aufbiegen des Sicherungsbleches mit
Montagevorrichtung (1) 22-50.430 Antriebsrad blockieren und
mit Steckschlüssel (2) (SW 24) Mutter lösen, abschrauben und
Sicherungsblech entfernen. Die im Bild angebrachten Pfeile
zeigen die Befestigungsschrauben der Montagevorrichtung.
|
Bild 15. Mutter für Antriebsrad lösen
Antriebsrad 68 Zähne mit Abzieher (1)
05 MV 45-3 abziehen.
|
Bild 16. Antriebsrad abziehen
Arretierhebel (1) aus der Kurvenwalze (2)
herauskippen, Zugfeder (3) aushängen und vom Führungsbolzen
(4) herunterziehen.
Drahtsprengring (5) und Sprengring (6) entfernen, Kappe für
Abtriebswelle (7) und darunterliegendes Ölleitblech
abnehmen.
|
Bild 17. Schaltarretierung und Sprengringe entfernen
3.2.4. Ausbau der Kickstarteranlage
nächster Punkt ; Index
Den Lagerbund der Kickstarterwelle zwischen
Kupferbacken oder Holzbeilagen in den Schraubstock
spannen (siehe Bild 84). Das Gewinde
der Keilschraube beim Herausschlagen nicht beschädigen.
Dazu wird die Mutter M 6 (SW 10) nur so weit gelöst,
daß sie als "Gewindeschutz" dienen kann.
Nach dem Entfernen der Keilschraube entspannt sich die
Kickstarterfeder, der Kupplungsdeckel dreht dabei nach
rechts.
Die komplette Kickstarterwelle kann jetzt aus dem
Kupplungsdeckel herausgezogen werden.
|
3.2.5. Ausbau der Kupplungsbetätigung
nächster Punkt ; Index
Den Druckhebel im Kupplungsdeckel aus der
Gewindeschnecke der Lagerbuchse durch Rechtsdrehung
abnehmen.
Lagerbuchse aus dem Kupplungsdeckel herausdrücken
(von innen nach außen).
Zum Austausch des Stützlagers 6302 der Kurbelwelle
in der Lagerbuchse Sprengring entfernen und Lager
herausdrücken.
|
3.2.6. Demontage und Montage der Kupplung
nächster Punkt ; Index
Die Montagevorrichtung 05-MV 150-2
(Bild 18) gestattet das Zerlegen und
Montieren der Kupplung. Zur besseren Handhabung wird
sie in einen Schraubstock eingespannt. Im Bild
20 wird die Montagestellung gezeigt.
Zur Demontage oder Kontrolle der Kupplung muß diese
so aufgesetzt werden, daß die Druckplatte (1) nicht auf
die Abstützschrauben (2) zu liegen kommt (Bild
18).
|
Bild 18. Demontage der Kupplung
Zur Demontage und Montage der Kupplung muß
immer der innere Mitnehmer mit Antriebsrad (3) auf
die Montagevorrichtung aufgesteckt werden.
Durch Rechtsdrehung der Knebelmutter (4) entspannt
sich der Kupplungsflansch und die Muttern (SW 10) (5)
können gelöst und mit den Sicherungsblechen entfernt
werden. Nach dem Herunternehmen der Knebelmutter (4)
kann die Kupplung in ihre Einzelteile (Bild 21)
zerlegt werden. Die Verschleißuntersuchung wird im
Abschnitt 3.4.1. behandelt.
Reihenfolge der Kupplungsmontage (Bilder 19,
19a, 20, 21)
- Inneren Mitnehmer mit Antriebsrad (3) auf die
Montagevorrichtung aufsetzen (Bild 19);
- Druckplatte mit Distanzbolzen (6) auf die
Abstützschrauben der Montagevorrichtung auflegen
(Bild 19);
- Zahnkranz (7) auflegen (Bild 19);
- Innenlamellen (8) und Außenlamellen (8 a) im
Wechsel einlegen (das Lamellenpaket wird durch
den inneren Mitnehmer zentriert);
- Kupplungskörper (9) aufsetzen, Sechskantschrauben
(11) mit Sicherungsblechen (10) einschrauben und
sichern (Bild 19a);
- Distanzscheiben 00-18.196 (14a) auf Distanzbolzen
auflegen (Bild 19a);
- Druckfedern (12) auf Kupplungskörper (9) aufsetzen;
- Druckflansch (13) auf legen und mit dem Oberteil
(0) der Kupplungsmontagevorrichtung spannen. Den
Druckflansch unter Beilage der Sicherungsbleche
(10) mit den Muttern (14) befestigen und sichern
(Bild 20).
|
Bild 19. Kupplungsmontage - 1. Phase
Bild 19a Kupplungsmontage - 2. Phase
Bild 20. Kupplung-Druckflanschverschrauben
Funktionsprüfung der kompletten Kupplung in
der Montagevorrichtung:
Die Knebelmutter (4) der Montagevorrichtung (Bild
18) wird durch Rechtsdrehung angezogen,
der innere Mitnehmer (3) mit Antriebsrad muß sich jetzt
frei drehen lassen.
Gleiche Prüfung kann mit dem Oberteil der
Montagevorrichtung 05-MV 150-2 im
eingebauten Zustand der Kupplung im Motor vorgenommen
werden.
|
Bild 21. Kupplung-Explosivdarstellung
3.2.7. Abbau der Zylindergruppe
nächster Punkt ; Index
Die Muttern (SW 13) mit Steckschlüssel von
den Zylinderstehbolzen kreuzweise allmählich lösen,
den Zylinderdeckel und danach den Zylinder abziehen.
Achtung:
Wird der Motor nicht zerlegt, ist die Öffnung des
Kurbelraumes mit einem sauberen Putztuch abzudecken!
Den Kolbenbolzen mit der Ausdrückvorrichtung (1)
22-50.010 herausdrücken und den
Kolben vom Pleuel abheben.
Achtung:
Das Herausschlagen des Kolbenbolzens schadet der Kurbelwelle
und zerstört das auf dem Kolbenbolzen sitzende
Nadellager!
|
Bild 22. Kolbenbolzen herausdrücken
Bild 23. Kettenrad am Getriebe abbauen
- Dichtkappe (1) abschrauben, mit Dichtung
herunternehmen und Ausgleichscheiben
herausnehmen;
- Zylinderrolle (2) für die Ankerarretierung und
den Drahtsprengring (3) entfernen;
- Gummistopfen (4) herausdrücken;
- Gehäusebefestigungsschrauben (14 Stück) mit
Schraubendreher lösen und aus dem Gehäuse
herausnehmen;
- Knebel der Motoren-Montagevorrichtung öffnen.
|
Bild 24. Motor rechte Seite
3.2.9. Trennen der beiden Gehäusehälften
nächster Punkt ; Index
Die Montagebrücke 22-50.430
wird mit zwei Schrauben M6 (1) auf die rechte Gehäusehälfte
geschraubt (siehe Bild 25).
Mit den Spindeln (2) vom Lagerauszieher 6203 und dem
Kupplungsabzieher werden die Gehäusehälften durch
gleichmäßiges Drehen der Druckspindeln getrennt.
Achtung:
Das Verwenden von anderen Hilfsmitteln wie Schraubendreher,
Meißel usw. führt zur Zerstörung des Gehäuses!
Rechte Gehäusehälfte abheben, und linke Gehäusehälfte
in der Motorenmontagevorrichtung festspannen.
|
Bild 25. Trennen des Gehäuses
3.2.10. Ausbau der Schaltung und des Getriebes
nächster Punkt ; Index
(A) = Antriebswelle
(B) = Abtriebswelle
Reihenfolge der Demontage:
- Schaltarm (1) des Schaltstückes (2) aus der
Kurvenwalze (3) in Pfeilrichtung Herausdrücken
und Schaltwelle mit Schaltstück (4) aus dem
Gehäuse herausziehen;
Achtung:
Dabei die Isolierscheibe (5) der Kurvenwalze nicht
beschädigen!
|
Bild 26. Schaltung und Getriebe
- Trennscheibe (6) (Gummi) aus der Ölfangtasche
des Gehäuses herausnehmen;
- Antriebs- und Abtriebswelle mit Aluminium-, Messing-
oder Kupferdorn aus dem Lagersitz von Kupplungsseite
aus herausschlagen;
Die Schaltarretierschraube wurde bereits bei einem
vorangegangenen Arbeitsgang entfernt.
- Kompletten Getriebesatz (Antriebs- und Abtriebswelle,
Kurvenwalze, Führungsbolzen mit Schaltgabeln) aus der
linken Gehäusehälfte herausziehen.
|
3.2.11. Herausdrücken der Kurbelwelle
nächster Punkt ; Index
- Die Montagebrücke (1) 22-50.430
mit eingesetztem Kupplungsabzieher (2) auf der
Kupplungsseite der linken Gehäusehälfte mit den
Befestigungsschrauben (3) und (4) befestigen;
Achtung:
Unbedingt vor dem Aufsetzen des Kupplungsabziehers
das Druckstück (5) auf den Zentrierbund der Kurbelwelle
auflegen (Bild 28)!
- Kurbelwelle mit der Druckapindel (6) des
Kupplungsabziehers durch Rechtsdrehung herausdrücken;
dabei hält die rechte freie Hand die Kurbelwelle von
unten und sorgt dafür, daß die Welle nach dem
Verlassen des Lagersitzes nicht herunterfällt.
|
Bild 27. Kurbelwelle herausdrücken
Bild 28. Druckstück-Demonstrationsbild
3.2.12. Lagerausbau - Getriebelager
nächster Punkt ; Index
Beide Gehäusehälften sollten vor dem Ausbau
der Kugellager erhitzt werden, damit keine Beschädigungen
der Lagersitze im Gehäuse auftreten.
Das Herausschlagen der Kugellager erfolgt mit dem
Schlagdorn 11 MW 7-4.
Linke Gehäusehälfte:
Auf der Kupplungsseite den Sprengring des Lagers 6204
entfernen und das Lager vom Getrieberaum aus
herausschlagen.
Das Lager 6203 von außen zum Getrieberaum herausschlagen
(der Sprengring wurde bereits nach der Demontage des
Primärtriebes entfernt).
|
Bild 29. Lager 6203 entfernen
Rechte Gehäusehälfte:
Das Lager 6204 vom Getrieberaum aus nach außen
herausschlagen.
Das Lager 6203 mit Abziehschraube (1) und
Spannpatrone (2) entfernen.
|
3.2.13. Abziehen der Lager 6306 von der Kurbelwelle
nächster Punkt ; Index
Mit dem Kugellagerabzieher 22-50.431
(1) werden die Kurbelwellenhauptlager 6306 C4f von der Kurbelwelle
abgedrückt. Dabei werden die beiden Hälften des Werkzeuges
zwischen Lager und Hubscheibe der Kurbelwelle angesetzt, im
Schraubstock zusammengedrückt und mit 2 Schrauben M 8x100 (2)
vorgespannt.
Durch das Einschrauben von 2 weiteren Schrauben mit
gehärtetem Zapfen am Anfang des Gewindes (3) werden die
Lager gegen die Hubscheiben der Kurbelwelle gedrückt
(Bild 30).
|
Bild 30. Abziehen der Kugellager 6306 von der Kurbelwelle
3.3. Reinigung aller Motorenteile
nächster Punkt ; Index
Vor der Verschleißuntersuchung der
Motorenteile werden diese einer gründlichen
Reinigung unterzogen. Welche Einrichtungen oder
Methoden angewendet werden, hängt von den
vorhandenen Möglichkeiten ab.
Als Resultat müssen jedoch immer einwandfrei saubere,
nicht korrodierte Teile für die weitere Behandlung
zur Verfügung stehen.
Besonders auf den freien Durchgang der Ölkanäle
für die Kurbelwellenhauptlager in beiden
Gehäusehälften achten. Zur Sicherheit die
Ölkanäle (1) mit Draht durchstoßen.
|
Bild 31. Kontrolle der Ölkanäle im Gehäuse
Im Zylinder werden eventuell verkokte Stellen
des Auspuffkanales und der Überströmkanäle gesäubert.
Den Brennraum im Zylinderdeckel und den Kolbenboden
mit Schaber und Drahtbürste von Ölkohle befreien.
Beide Oberflächen müssen nach dem Reinigen ohne
Riefen und metallisch blank sein.
Über die Reinigung der Kolbenringnuten des Kolbens
sind im Abschnitt 3.4.3.4. Hinweise
enthalten.
3.4. Verschleißuntersuchungen
3.4.1. Kupplung und Kupplungsbetätigung
nächster Punkt ; Index
Verschleißstellen:
- Innenlamelle mit Reibbelag
Verschleiß tritt verstärkt bei unkorrekter
Kupplungseinstellung auf (kein Kupplungsspiel
oder zu langes Schleifenlassen der Kupplung).
Im Extremfall verbrennt der Reibbelag.
Wenn die Kupplung nicht mehr nachgestellt werden
kann und diese bei der Beschleunigung des Motors
rutscht, sind neue Lamellen einzubauen.
Das trifft zu, wenn das Maß "x"
im Bild 32 unter 0,5 mm kommt.
Neue Lamellen sind 3,0 mm ± 0,1 mm dick.
Verschleißwert: -0,3 mm;
|
Bild 32. Kupplungs-Verschleißwert
- Außenlamelle
Sie sind auszuwechseln, wenn sie durch Kupplungsrutschen
blau angelaufen (weich geworden!) oder verzogen sind.
Dicke im Neuzustand: 1,5 mm -0,1 mm.
Planabweichung der Fläche max. 0,2 mm;
- Druckfedern
Diese können in ihrer Pederwirkung nachlassen, d.h.
sie setzen sich.
In krassen Fällen rutscht die Kupplung, auch wenn alle
anderen Bauteile und die Einstellungen in Ordnung sind.
Neuwerte:
Länge, entspannt 28,3 mm ± 0,6 mm
Einbaulänge 17,0 mm
Federkraft im Einbauzustand 135 N (13,5kp) ± 11 %
- Antriebsrad mit innerem Mitnehmer
(Bild 33)
Es ist zu überprüfen, ob die Kerbstiftverbindung zwischen
dem Antriebsrad und dem inneren Mitnehmer in Ordnung ist.
Bei loser Kerbstiftverbindung ist der innere Mitnehmer
mit Antriebsrad auszuwechseln (ein Nachnieten ist
zwecklos!);
- Verzahnung-Mitnehmer und Zahnkranz
Entsteht beim Ziehen der Kupplung ein Geräusch, so
haben einzelne Lamellen (Außen- oder Innenlamellen)
im Zahnkranz oder auf dem inneren Mitnehmer erhöhte
Luft in der Nutverzahnung und sie beginnen nach Aufhebung
des Kupplungsdruckes zu klirren.
Das Geräusch kann beseitigt werden, wenn die Lamellen
im Zahnkranz und auf dem inneren Mitnehmer einzeln
aufgepaßt und solche mit zu großer Luft ausgewechselt
werden;
- Nadellager und Kupplungsdrucklager
Am Nadellager für inneren Mitnehmer ist auch nach
längerer Laufzeit kaum Verschleiß feststellbar;
Das Kupplungsdrucklager ist am Außenring, im
Druckflansch sitzend, 3mal in gleichmäßigen
Abständen verstemmt (1). Es ist darauf zu achten,
daß sich der Außenring des Drucklagers nicht
im Druckflansch dreht;
|
Bild 33. Innerer Mitnehmer mit Antriebsrad
Bild 34. Kupplungsdrucklager
- Konus im Kupplungskörper
Der Konus kann durch Rutschen der Kupplung auf dem
Konus der Kurbelwelle infolge unsachgemäßer Montage
beschädigt sein. In leichten Fällen wird der
Kupplungskörper durch Aufschleifen mit Schleifpaste
auf den Konus der Kurbelwelle wieder verwendbar;
- Druckhebel und Lagerbuchse (Bild 35)
Gratbildung, Druckstellen und scharfe Kanten (1) an der
Verzahnung beider Teile haben ruckendes Ein- und Auskuppeln
zur Folge.
Man beseitigt diese Mängel mit einem passenden Korundstein
oder einer Doppelschlichtfeile. Beide Teile vor der Montage
zusammenstecken und auf Leichtgängigkeit prüfen.
|
Bild 35. Kupplungsbetätigung
3.4.1.1. Primärtrieb
nächster Punkt ; Index
Bei zu großem Zahnflankenspiel zwischen dem
mit dem Kupplungsmitnehmer vernieteten Antriebsrad (28
Zähne) und dem Antriebsrad (68 Zähne) zum Getriebe
gibt es Geräusche im Leerlauf des Motors und bei
Lastwechsel.
Das Zahnflankenspiel beträgt im Neuzustand 0,036 mm
bis max. 0,131 mm.
Bei mehr als 0,25 mm Zahnflankenspiel ist ein neues
Stirnradpaar einzubauen.
Die Radialspiele der Lager 6306 und 6203 sind bei dem
Ausmessen des Zahnflankenspiels zu beachten. Die
Stirnräder sind auf beschädigte Zähne zu
kontrollieren.
|
3.4.1.2. Zwangsausspurung des Kickstarters
nächster Punkt ; Index
Verschleiß wird in der Hauptsache am
Nockenblech (1) auftreten, wenn bei dem Startvorgang
der Kickstarter nicht voll nach unten durchgetreten
wird. Dadurch bedingt, kommt es zum Rückschlag des
Motors und das Nockenblech wird durch abnormale Belastung
zerstört (Verbiegung oder Bruch).
Das verbogene oder angebrochene Nockenblech führt zur
Verringerung des Abstandes (x) zwischen dem Kickstarterrad
und -mitnehmer in Einbauzustand der Kickstarterwelle,
was zur Abnutzung der Stirnverzahnung (2) beider Räder
führt.
|
Bild 36. Kickstarterwelle
3.4.2. Zahnräder, Wellen und Schaltgabeln
nächster Punkt ; Index
Die Hinterschneidungen der Klauen an den
Schalträdern (beiderseits) und den Gegenzahnrädern sind
in einem Winkel von 3° angebracht.
Im eingerasteten Zustand (Gang eingelegt) entsteht durch
die Keilwirkung der Hinterschneidungen eine Kraft mit
der Aufgabe, Schalt- und Zahnrad (Losrad) ineinander
zu halten.
Nicht nur der Schaltarretierhebel (1) (Bild 17)
hält die einzelnen Gänge im eingerasteten Zustand,
sondern auch die Keilwirkung der Hinterschneidungen
trägt mit dazu bei.
Sind die Klauen der Schalträder stark abgenutzt,
wird die tragende Fläche kleiner und es kommt zum
Herausspringen der Gänge.
Die Schaltgabeln sind auf Winkligkeit zu überprüfen,
sie müssen zum Führungsbolzen der Schaltgabeln genau
im rechten Winkel (90°) stehen. Geringfügig verzogene
Schaltgabeln können unter Vorsicht kalt nachgerichtet
werden.
|
Bild 37. Schaltgabel und Schaltklauen
Eine nicht im rechten Winkel stehende
Schaltgabel läuft ständig am Schaltrad an und
wird ebenso wie das Schaltrad blau anlaufen. Damit
geht die Einsatzhärte verloren und beide Teile
werden nach kurzer Laufstrecke unbrauchbar, sie
müssen ausgewechselt werden.
Zur einwandfreien Kontrolle des Getriebesatzes ist
es erforderlich, alle Einzelteile gründlich zu
reinigen, damit eventuell blau angelaufene Teile
erkannt werden können.
Die Abtriebswelle ist auf saubere Ölbohrungen
zur Schmierung der Zahnräder II. und III. Gang
zu untersuchen (Bild 38).
Blau angelaufene Zahnräder, Wellen und
Schaltgabeln sind grundsätzlich auszuwechseln.
|
Bild 38. Schaltsatz
3.4.2.1. Schaltwelle mit Schaltstück und Schaltanschlag
nächster Punkt ; Index
Das Schaltstück (1) ist auf
Leichtgängigkeit des Schaltarmes (2) zu prüfen.
Die Druckfeder (3) muß in der eingesenkten Bohrung
der Schaltwelle gut sitzen. Das gleiche trifft auch
für die Sicherungsscheiben (4), (5), (6), (7) zu.
Das Maß "a" beträgt 16,6 mm. Dieser Ausschnitt
begrenzt den Drehwinkel der Schaltwelle (8). Die
Rückholfeder (9) hat eine hohe Lebensdauer, sie braucht
nur auf Anrisse untersucht zu werden.
|
Bild 39. Fußschaltwelle mit Schaltstück
Der in das Gehäuse eingedrückte
Zylinderstift 8x80 (Schaltanschlag), siehe Bild
57, darf nicht locker oder verbogen
sein.
Die Kerbverzahnung der Fußschaltwelle wird zerstört,
wenn der Fußschalthebel locker sitzt und nicht
nachgezogen wird.
Ist die Kerbverzahnung stark beschädigt, muß die
Fußschaltwelle mit Schaltstück ausgewechselt
werden.
|
3.4.3. Kurbeltrieb
3.4.3.1. Zylinder und Kolben
nächster Punkt ; Index
Sollte sich am Motor eine Leistungsminderung
bemerkbar machen, welche nicht auf falsche Zündeinstellung,
Vergasereinstellung, undichte Wellendichtringe oder
verstopfte Auspuffanlage (Staudruck zu hoch) zurückzuführen
ist und der ausgebaute Kolben ist unterhalb der Kolbenringpartie
am gesamten Kolbenhemd "schwarz", so müssen
Kolben und Zylinder ausgewechselt werden (Kompressions- und
Verbrennungsdruck schlägt an der Lauffläche der Kolbenringe
und der Zylinderwandung durch).
Der Zylinder hat in diesem Falle in der Laufbuchse (Kanalzone)
eine starke Ausarbeitung (Aufbauchung) und unterhalb der
Oberkante der Laufbuchse einen spürbaren Ansatz. Das
alleinige Wechseln verschlissener Kolbenringe ist zwecklos.
Das Auswechseln des Zylinders kann durch Einsatz eines
neuen Zylinders mit Kolben erfolgen, oder der ausgebaute
Zylinder wird regeneriert (was wirtschaftlicher ist),
indem durch eine Zylinderschleiferei nach einem neuen
Kolben der Zylinder (unter Beachtung des vorgeschriebenen
Einbauspieles 0,05 mm) nachgeschliffen wird.
Kolben mit folgenden Übergrößen stehen zur Verfügung:
69,50 mm; 70,00 mm; 70,50 mm und 71,00 mm.
|
3.4.3.2. Kontrollmessung von Kolben und Zylinder
nächster Punkt ; Index
Im Neuzustand von Kolben und Zylinder
beträgt das Einbauspiel zwischen Zylinderlaufbuchse
und Kolben 0,04 mm.
Die Verschleißgrenze liegt bei etwa 0,09 mm. Dann
muß ein neuer oder Austauschzylinder aufgebaut werden,
da die Geräusche mit steigen - dem Einbauspiel ansteigen
(besonders bei Gaswechsel und bei unbelastetem Motor).
Das Nennmaß des Kolbens wird etwa 30 mm oberhalb der
Kolbenunterkante gemessen. Nur ein neuer Kolben kann
bei einer Kontrollmessung, unter Beachtung der
Meßvorschriften, das aufgeschlagene Nennmaß
erreichen. Ein bereits gelaufener Kolben ist verformt.
Der Zylinder ist mit einem Innenmeßgerät im
unteren und oberen Drittel der Laufbuchse zu messen.
Ohne Meßgerät kann der Verschleiß an der entstandenen
Kante (Absatz), etwa 8 mm unterhalb der Oberkante der
Zylinderlaufbuchse erkannt werden.
|
3.4.3.3. Beseitigung eines leichten Kolbenklemmers
nächster Punkt ; Index
Ist es zu einem Kolbenklemmer gekommen,
so kann bei einem leichten Fall der Kolben durch
Nacharbeiten der Klemmstellen mit einem in
Kraftstoff-Öl-Gemisch getauchten Korundstein
wieder brauchbar gemacht werden.
Leichte Klemmstellen im Zylinder durch angepreßte
Aluminiumrückstände (vom Kolben verursacht)
sind mit feinem Schleifpapier (etwa 400er Körnung)
vorsichtig nachzuarbeiten.
Das Nacharbeiten der Klemmstellen am Kolben und im
Zylinder nur in Längsrichtung durchführen.
Achtung:
Es hat keinen Zweck, nach einem Kolbenklemmer nur
die Klemmstellen zu beseitigen und nicht die Ursache,
welche zum Klemmen führte zu erkennen und abzustellen.
Einige Beispiele möchten wir aufzeigen:
- Ölmangel (es wurde kein Kraftstoff-Öl-Gemisch,
sondern blanker Kraftstoff getankt);
- Kraftstoffmangel und demzufolge auch Ölmangel
durch ungenügenden Nachlauf vom Kraftstoffbehälter
zum Vergaser. Belüftungsbohrung im Tankdeckel
nicht frei;
- Kraftstoffilterhahn verstopft oder Halteschrauben
am Knebel zu fest angezogen (Knebel muß leichtgängig
sein);
- Vergasergrundeinstellung verändert;
- Zündeinstellung falsch, dadurch Überhitzung des
Motors;
- Auspuffanlage durch Fremdeingriff verändert,
Staudruck stimmt nicht;
- Luftfilteranlage defekt;
- Motor saugt falsche Luft (Abmagerung im
oberen Drehzahlbereich).
3.4.3.4. Kolbenringe
nächster Punkt ; Index
Vor der Weiterverwendung gebrauchter
Kolben ist den Kolbenringen und den Ringnuten im
Kolben einige Aufmerksamkeit zu schenken.
|
Bild 40. Ringnuten reinigen
Durch zu viel oder ungeeignetes Öl
im Kraftstoff (Zweitaktmischung) festgebrannte
Kolbenringe werden vorsichtig vom Kolben entfernt,
sie dürfen dabei nicht überdehnt werden.
Die am Innendurchmesser des Kolbenringes haftende
Ölkohle wird entfernt und die Ringnuten im Kolben
sind mit einem alten gebrochenen Kolbenring
gleichen Typs vorsichtig zu reinigen.
Nach diesem Arbeitsvorgang müssen die Kolbenringe
in den Ringnuten frei beweglich sein.
Die Kolbenringe dürfen nicht verwechselt d.h.,
sie müssen in die Ringnut eingesetzt werden, aus
der sie herausgenommen wurden.
Kein Öl beim Einsetzen der Kolbenringe verwenden!
Breite der Ringnuten |
Obere Ringnut | 2,06 | +0,02 | mm |
|
Mittlere und untere Ringnut | 2,04 | +0,02 | mm |
|
Verschleißwert | 2,10 mm |
Dicke der Kolbenringe |
Alle Kolbenringe | 2,00 | -0,010 | mm |
-0,022 |
Verschleißwert | 1,90 mm (Maximum!) |
|
Bild 41. Ringstoß messen
Bevor die Kolbenringe wieder auf den
Kolben aufgesetzt werden, überprüfen wir noch den
Verschleißzustand ihres Außendurchmessers. Dazu wird
der Kolbenring bis etwa 10 mm unterhalb der Oberkante
des Zylinders in die Zylinderlaufbuchse eingesetzt
und der Ringstoß gemessen. Im Neuzustand der Kolbenringe
soll der Ringstoß 0,2 mm betragen.
Bei mehr als 1,6 mm Ringstoß sind Kolben und Zylinder
unbrauchbar.
Sitzen die Arretierstifte im Kolben locker (Stirnseiten
der Stifte blank), oder fehlen diese, ist ebenfalls ein
neuer Kolben mit Zylinder (evtl. ausgeschliffen)
aufzubauen.
Achtung:
Die Kanten der Kanalfenster müssen
angefast sein. Andernfalls gibt es häßliche Geräusche
bei unbelastetem Motor!
Deshalb die Kanalfenster neugeschliffener Zylinder
stets leicht anfasen!
3.4.3.5. Zylinderdeckel
nächster Punkt ; Index
Sollte der Zylinderdeckel einmal undicht
sein, was an den oberen verölten Rippen des
Zylinders zu erkennen ist, dann kann der Zylinderdeckel
auf einer Tuschierplatte mit untergelegtem feinen
Schleifleinen (400er Körnung) durch kreisende Bewegungen
in geringem Umfang nachgearbeitet werden, falls kein
neuer Zylinderdeckel zur Verfügung steht.
|
Bild 42. Zylinderdeckel-Dichtfläche und Brennraum
Bei einem undichten Zylinderdeckel ist
das zusätzliche Unterlegen einer weiteren
Aluminium-Ausgleichscheibe falsch. Es führt nicht
zum Erfolg, das Verdichtungsverhältnis wird damit
verändert, was wiederum zur Leistungsminderung
führt.
Achtung:
Bei der Demontage und Montage des
Zylinderdeckels ist unbedingt darauf zu achten,
daß die Befestigungsmuttern gleichmäßig und über
Eck gelöst und angezogen werden.
Bei Nichtbeachtung dieses Hinweises verspannt sich
der Zylinderdeckel und wird undicht.
3.4.3.6. Kurbelwelle
nächster Punkt ; Index
Eine Sichtkontrolle entscheidet, ob die
Dichtringbunde (1) zu stark eingelaufen sind, das
Gewinde der Kupplungsbefestigung (2), der Zentrierbund
(3) und das Gewinde für die Ankerhalteschraube
(4) sowie die Konen für die Kupplung (5) und der Anker
(6) noch einwandfrei sind.
|
Bild 43. Kurbelwelle
Wenn möglicherweise festgestellte Mängel
nicht durch Nacharbeit beseitigt werden können, ist
eine neue oder regenerierte Kurbelwelle einzubauen.
|
Bild 44. Radialschlag messen
Danach erfolgt die Messung des Radialschlages
der im Bild 44 gekennzeichneten Stellen.
Dazu wird die Kurbelwelle zwischen zwei feststehenden
Spitzen eines Rundlauf-Prüfgerätes oder einer
Drehmaschine eingespannt.
Der zulässige Radialschlag beträgt 0,03 mm.
Größere Werte führen zu Zündstörungen bei
hohen Drehzahlen, Vibrationen des Motors und Undichtheit
der Wellendichtringe.
Das Resultat ist schlechte Motorleistung. Eine neue
Kurbelwelle sollte ebenfalls überprüft werden,
da an diesen Wellen Transportschäden vorliegen können.
|
Bild 45. Radialluft des Pleuels messen
Ausgeschlagene Nadellager im großen und
kleinen Pleuelauge machen sich durch Geräusche
unter Belastung bemerkbar.
Die Messung des großen Pleuelauges erfolgt wie im Bild
45. Das Radialspiel beträgt im
Neuzustand der Kurbelwelle 0,020...0,035 mm.
Bei mehr als 0,05 mm ist die Kurbelwelle verschlissen.
|
Bild 46. Axialspiel großes Pleuelauge prüfen
Den Zustand der Lagerung im kleinen
Pleuelauge kann man mit den üblichen
Werkstatteinrichtungen nur subjektiv beurteilen. Der
Kolbenbolzen muß im Pleuel spielfrei sein und sich
mit eben fühlbarem Widerstand, ohne zu klemmen,
drehen lassen. Eingelaufene oder blau angelaufene
Kolbenbolzen sind unbrauchbar und müssen
ausgewechselt werden.
Axialspiel des großen Pleuelauges zwischen den Hubscheiben
0,170...0,563 mm.
Verschleißwert: 1,0 mm.
|
3.4.4. Gehäuse und Dichtungen
nächster Punkt ; Index
Die Untersuchung erstreckt sich in erster
Linie auf den Zustand der Gehäusedichtflächen.
Sind diese beschädigt, kann man sie in leichten
Fällen, wie im Bild 42 am Beispiel
des Zylinderdeckels gezeigt wird, auf einer
Tuschierplatte mit untergelegtem feinen Schleifleinen
nacharbeiten.
Weiter muß am Gehäuse überprüft werden,
ob die Lagersitze und die Nuten der Sicherungsringe
noch einwandfrei sind.
Lagersitze sind unbrauchbar, wenn sich die Lager von
Hand in das kalte Gehäuse bzw. auf den Lagersitz
der Wellen (Lagerinnenringe kalt) schieben lassen.
Die Wellendichtringe sind auf Einrisse der Dichtlippe,
deren Verschleiß (Abflachung) und Spannung; auf das
Vorhandensein der Feder in der für sie bestimmten Nut
und die Güte der Verbindung beider Federenden zu
untersuchen. Es ist besser, einen Wellendichtring vorzeitig
auszutauschen, als einen Monat später den Motor
wegen dieses relativ billigen Teiles nochmals zu
demontieren.
|
3.4.5. Radialrillenlager für Kurbelwelle und Getriebe
nächster Punkt ; Index
Defekte Kurbelwellenhauptlager erkennt
man bereits am Motorengeräusch und an der Unmöglichkeit,
den Unterbrecherabstand genau einstellen zu können.
Der Zustand der Laufflächen und Kugeln kann bei Lagern
mit Kunststoffkäfig nach dem Auseinanderdrücken
festgestellt werden. Verschlissene Lager zeichnen
sich durch Pittingbildung aus.
Auch bei den Lagern gild der Grundsatz, daß nach
längerer Lebensdauer des Motors (Generalüberholung)
alle Lager durch neue ersetzt werden.
Folgende Lager sind zu verwenden:
Für die Kurbelwelle sind als Hauptlager 2 Stück
6306 C 4 f (Plastkäfig) und als Stützlager der
Kurbelwelle in der Lagerbuchse 1 Stück 6302 C 3 f
(Plastkäfig) zu verwenden.
Im Getriebe werden
2 Stück Lager 6203 J C 4,
1 Stück Lager 6204 J C 4 und
1 Stück Lager 6304 J C 4
eingebaut.
|
4. Montage des Motors
4.1. Vorbereitungsarbeiten
nächster Punkt ; Index
Sämtliche Teile des Motors sind gereinigt.
Defekte Teile wurden bereits ausgesondert und durch
neue ersetzt. Die weiter verwendbaren Teile sind bereits
für den Wiedereinbau vorbereitet. Ehe die Motormontage
beschrieben wird, soll anschließend nochtetwas über die
Auswahl bzw. Paarung verschiedener Aggregate ausgeführt
werden.
|
4.1.1. Auswahl von Kolben und Zylinder
nächster Punkt ; Index
Der Zylinder der ETZ 250 weicht von
den bisherigen Zylindern ab. Im Zylinder sind vier
Überströmkanäle angeordnet. Der Ansaugkanal verfügt
über eine Führungsnase für die Kolbenringe. Der
Kolben ist nur in der Ausführung 69.6 mit auf den neuen
Zylinder abgestimmter Formkurve zu verwenden.
|
Bild 47. Zylinder-untere Dichtfläche
Bild 48. Zylinder-Ansaugpartie
Zwischen Kolben und Zylinder ist ein
Einbauspiel von 0,04mm vorgesehen. Nachstehende Tabelle
erleichtert die Auswahl der zu paarenden Bauteile.
Zylinder | Kolben 69.6 |
Kennzeichnung (Toleranzgruppe) | Nennmaß in mm | Nennmaß in mm |
1 = -1 | 68,99 | 68,94 |
0 | 69,00 | 68,95 |
+1 | 69,01 | 68,96 |
+2 | 69,02 | 68,97 |
In dieser Tabelle handelt es sich um
Kolben und Zylinder mit Neumaß, welche von unserer
Abteilung Ersatzteilvertrieb bezogen wurden, oder
um in der Produktion in unserem Werk montierte Teile.
|
Bild 49. Zylinderkennzeichnung
- Toleranzgruppe
Bild 50. Kolbenkennzeichnung
- Nennmaß in mm
- Einbaurichtung
4.1.2. Regenerierung des Zylinders
nächster Punkt ; Index
Jeder Zylinder kann vom Grundmaß (69,00 mm)
ausgehend max. 2,00 mm ausgeschliffen werden.
Kolben in den Übergrößen
69,50; 70,00
70,50; 71,00
stehen zur Verfügung.
Der Zylinder wird in der Zylinderschleiferei nach dem
vorhandenen Kolben unter Beachtung des vorgeschriebenen
Einbauspiels von 0,04 mm geschliffen und im gepaarten
Zustand ausgeliefert.
|
4.1.3. Auswahl des Nadellagers für den Kolbenbolzen (Neuteile)
nächster Punkt ; Index
Die Auswahl des passenden Nadellagers
können, Sie entsprechend der mit Bild
51 gezeigten Tabelle vornehmen.
Dies ist nur für Neuteile (Kurbelwelle, Kolben
und Kolbenbolzen, sowie Nadellager) möglich.
Beachten Sie bitte, daß die Handelspackungen der
Nadellager nur mit den mittleren Abmaßen (ermittelt
aus oberem und unterem Nadelabmaß) gekennzeichnet
sind. Die Nadellager selbst sind nicht markiert!
Deshalb angebrochene Packungen stets getrennt halten.
Wenn Kolbenbolzen, Kolben und Kurbelwelle gebraucht
weiterverwendet werden, das Nadellager nach Gefühl
einpassen. (Farbmakierung ist nicht mehr genau
erkennbar.) Der Kolbenbolzen ist spielfrei einzupassen
und muß sich mit eben fühlbaren Widerstand, ohne
zu klemmen, drehen lassen.
|
Bild 51. Tabelle zur Lagerauswahl
(nicht gekennzeichnete Maße in mm)
4.1.4. Lager und Dichtringe
nächster Punkt ; Index
Für das Getriebe werden Lager mit
Kunststoffkäfigen verwendet.
2 x 6204 J C 4,
1 x 6203 J C 4 und
1 x 6304 J C 4
Die Kurbelwellenhauptlager 6306 sind nur in der
Sortierungsgruppe C4f und das Stützlager der
Kurbelwelle in der Lagerbuchse (Kupplungsdeckel) in
der Sortierungsgruppe C3f zu verwenden. Als
Kupplungsdrucklager wird ein Rillenkugellager
16005 eingebaut.
Die Wellendichtringe D25x72x7 müssen unbedingt
kraftstoff- und ölfest sein (nur originale
Wellendichtringe verwenden).
Das Nadellager für den Kupplungsmitnehmer ist nach
folgender Tabelle auszuwählen, wenn ein neuer
Mitnehmer eingebaut wird.
Kupplungsmitnehmer (Kennzeichnung) | Nadellager (mittl. Abmaß in mm) |
gelb | -1; -2; -3; -4 |
schwarz | -3; -4; -5; -6 |
grün | -5; -6; -7; -8; -9 |
|
4.1.5.1. Komplettierung der Antriebswelle (A)
nächster Punkt ; Index
- Antriebsrad für IV. Gang (1) bis zum Festrad
(2) aufschieben, Anlaufscheibe (3) und Sprengring
(4) montieren;
Achtung:
Auf guten Sitz der Sprengringe in den Nuten achten.
Kontrolle durch Aufschlagen der Welle auf Hartholz,
dabei wird das Antriebsrad (1) in einer Hand
gehalten!
- Das Schaltrad IV. und V. Gang (5) auf Antriebswelle
aufschieben, dabei zeigt die Seite mit den 18 Zähnen
zum Antriebsrad für IV. Gang (1);
- An den Bund (Beginn der Nuten) eine gehärtete und
geschliffene Distanzscheibe (6) anlegen. Zwei dieser
Distanzscheiben werden auf der Antriebswelle und zwei
auf der Abtriebswelle benötigt. Sie sind untereinander
austauschbar;
- Das Antriebsrad für V. Gang (7) aufschieben und die
24 Lagernadeln (8) (2,5x11,8) einsetzen, anschließend
die Distanzscheibe (6) und den Sprengring (9) montieren
(auf guten Sitz des Sprengringes in der Nut achten).
|
Bild 52. Antriebswelle (A) und Abtriebswelle (B)
4.1.5.2. Komplettierung der Abtriebswelle (B)
nächster Punkt ; Index
- Zuerst die Abtriebswelle auf saubere Ölbohrung
für die Zahnräder (Fensterräder) II. und III. Gang
überprüfen. Erst danach das Zahnrad für II. Gang (10)
(28 Zähne) bis an den Bund des Nutstückes aufschieben,
Distanzring (11) und das Zahnrad für III. Gang (12)
(24 Zähne) an Distanzring anlegen;
Achtung:
Die Zahnräder (10) und (12) mit der flachen Seite
zum Distanzring (11 ) zeigend montieren!
- Die Anlaufscheibe (3) und den Sprengring (4) aufsetzen;
- Das Schaltrad für I. und III. Gang (13) aufschieben.
Die Distanzscheibe (6) an den Bund des Nutstückes
anlegen und das Zahnrad für I. Gang (14) (36 Zähne)
aufsetzen. Die 24 Stück Lagernadeln (8) (2,5x11,8)
einlegen und die Distanzscheibe (6) aufstecken sowie den
Sprengring (9) einbauen;
- Das Schaltrad für II. Gang (15) auf der entgegengesetzten
Seite der Abtriebswelle aufstecken.
|
Bild 53. Getriebesatz im Montagebehälter
- Antriebswelle
- Abtriebswelle
- Die Schaltgabel 011 (1) (mittlere
Schaltgabel) zuerst in das Schaltrad IV. Gang und
V. Gang einsetzen (A = Antriebswelle).
Danach die Schaltgabel 010 (2) in das Schaltrad für
I. und III. Gang und die Schaltgabel 012 (3) in das
Schaltrad für den II. Gang einsetzen (B = Abtriebswelle).
Jetzt kann der Führungsbolzen (E) für die Schaltgabeln
eingeschoben werden (langer Bund zum großen Zahnrad
für I. Gang (4) 36 Zähne zeigend). Die Scheiben (5)
nicht vergessen aufzustecken;
|
Bild 54. Getriebesatz mit Schaltgabeln
- Nun wird die Kurvenwalze (C) in die
Führungsbolzen der Schaltgabeln eingelegt. Dabei
muß die Isolierscheibe (1) der Kurvenwalze am
schwachen Lagerzapfen zur Seite der Schaltgabel
012 zeigen.
Der Getriebesatz ist jetzt einbaufertig.
|
Bild 55. Getriebesatz einbaufertig
Bild 56. Ersatzteilgehäuse-Sortiment
Wird ein Ersatzteilgehäuse verwendet,
muß dieses zunächst komplettiert werden. Es sind
die im Bild 56 gekennzeichneten
Teile wie folgt einzubauen:
- Kerbnagel (1) für Schaltarretierfeder in
linke Gehäusehälfte (Kupplungsseite)
eindrücken;
- Kerbstift (2) zur Lagefestlegung der
Lichtmaschine in die rechte Gehäusehälfte
eindrücken;
- Paßhülse (3) und Zylinderstift (4) in
linke Gehäusehälfte auf Kupplungsseite
eindrücken;
- Zylinderstift 8x80 (s) Bild
57 für Schaltanschlag
auf eine Höhe von a =
57-1 mm,
von der Dichtfläche aus gemessen,
eindrücken in kaltes Gehäuse;
|
Bild 57. Schaltanschlag und Ölleitblech montieren
- Ölleitblech (4 Bild 57)
im Getrieberaum einsetzen und auf Kupplungsseite
Sicherungsblech auflegen, Befestigungsmutter M 6
anziehen und sichern;
- Verschlußscheiben (6) in die entsprechenden
Bohrungen der rechten Gehäusehälfte von der
Lichtmaschinenseite aus so eindrücken, daß
Dichtheit garantiert ist.
Wird das alte Gehäuse weiter verwendet,
sind nur nachstehende Arbeitsgänge auszuführen:
- Inneren Sprengring (1) für das
Kurbelwellenhauptlager 6306 C4f einsetzen
(Öffnung zur Ölbohrung zeigend - Pfeil a);
- Sprengring (2) für das Getriebelager
6203 C4f (Abtriebswelle) im Gehäuse
montieren. Öffnung des Sprenringes muß nach
oben zur Ölfangtasche zeigen (siehe Pfeil b);
|
Bild 58. Linke Gehäusehälfte
Bild 59. Linke Gehäusehälfte - Ölleitscheibe und Getriebelager
- Gehäusehälfte auf etwa 100°C aufheizen, dabei
dürfen keine Gummiteile in der Gehäusehälfte
montiert sein;
- Getriebelager 6204 JC4 (1) für Antriebswelle
von der Kupplungsseite bis zum Gehäusebund
einsetzen und Sprengring (2) auf Kupplungsseite
montieren;
- Kappe (3) und Dichtblech (4) sowie Getriebelager
6203 JC4 für Abtriebswelle in der Reihenfolge vom
Getrieberaum aus einsetzen;
- Ölleitscheibe (5) für das Lager 6306 C4f
auf den Sprengring (6) vom Kurbelraum aus
auflegen. Der am äußeren Rand der
Ölleitscheibe an einer Stelle eingedrückte
kleine Punkt zeigt zur offenen Stelle des
Sprengringes und dient als Sicherung gegen
Verdrehung (siehe Pfeil im Bild
59);
- Kurbelwellenhauptlager 6306 C4f (3) mit
Montagedorn (1) (29-50.405)
einsetzen. Die Olleitscheibe wird dabei
mit dem konischen Bund des Montagedornes
zentriert (2);
|
Bild 60. Kurbelwellenhauptlager einsetzen
4.2. Montage der Kurbelwelle, des Getriebes und der Fußschaltwelle
nächster Punkt ; Index
- Den Innenlaufring des bereits im Gehäuse
befindlichen Lagers 6306 mit Heizdorn (1 im Bild
61) aufwärmen;
- Kurbelwelle mit den langen Kurbelwellenzapfen in
den aufgeheizten Innenlaufring des Lagers
einführen und in einem Zug bis zum Anschlag
hineinrutschen lassen;
- Sollte die Kurbelwelle doch einmal durch
zögerndes Einsetzen oder schlecht
aufgeheizten Innenlaufring stecken bleiben, kann
die Kurbelwelle mit dem Rohrstück (1) und dem
Oberteil der Kupplungsspannvorrichtung (2)
05 MV 150-2 nachgezogen
werden. (Das Rohrstück ist kein SpezialWerkzeug,
die Selbstbauskizze ist im Anhang abgedruckt);
|
Bild 61. Innenlaufring aufheizen
Bild 62. Nachziehen der Kurbelwelle
Bild 63. Getriebesatz einsetzen
- Den vorkomplettierten Getriebesatz aus
dem Montagebehälter herausnehmen und in die
linke Gehäusehälfte bis Anschlag einsetzen.
Der lange Bund der Kurvenwalze und der des
Führungsbolzens für die Schaltgabeln müssen
bei richtiger Montage auf der Kupplungsseite
herausragen (die Schaltstellung spielt dabei
keine Rolle);
|
Bild 64. Getriebe und Kurbelwelle montiert
- Fußschaltwelle mit Schaltstück (1)
montieren, dabei den Schaltarm (2) in die Kurvenwalze
(3) einrasten;
Achtung:
Dabei Isolierscheibe der Kurvenwalze nicht
beschädigen!
- Trennscheibe (4) in die Öltasche des
Kurbelraumes einlegen;
- Innenlaufring des Getriebelagers 6203 C4f aufheizen
und auf Antriebswelle (5) aufsetzen;
- Sämtliche Lager, Wellen und Bolzen leicht ölen;
- Dichtfläche zwischen beiden Gehäusehälften
mit Dichtmasse einstreichen, dabei darf keine
Dichtmasse in den Kurbel- und Getrieberaum
gelangen. Beide Gehäusehälften werden ohne
Dichtung montiert;
4.3. Vormontage der rechten Gehäusehälfte
nächster Punkt ; Index
- Die rechte Gehäusehälfte ist während der
vorangegangenen Montagearbeiten auf etwa 100°C
erwärmt worden (keinesfalls die Wellendichtringe
im Gehäuse belassen, da diese durch Überhitzung
verhärten und dadurch im Fährbetrieb undicht werden);
|
Bild 65. Rechte Gehäusehälfte vorbereiten
- Inneren Sprengring für das Lager 6306 C4f
montieren (Öffnung zur Ölbohrung);
- Ölleitscheibe (1) auf Sprengring auflegen.
Flache Seite zeigt zum Außenlaufring des Lagers, die
eingedrückte Vertiefung (Pfeil) zur Öffnung
des Sprengringes;
- Lager 6306 C4f (2) mit Montagezentrierdorn
29-50.405 (3) in
Gehäusehälfte einsetzen, dabei wird das
Ölleitblech mit dem konischen Bund (4) des
Montagezentrierdornes zentriert;
4.3.1. Aufsetzen der rechten Gehäusehälfte
nächster Punkt ; Index
- Innenlaufring des Lagers 6306 C4f aufheizen,
Gehäusehälfte aufsetzen. Ist dabei die
Gehäusehälfte auf etwa 100°C aufgeheizt und
der Innenlaufring des Lagers 6306 gut bis an die
Dichtflächen drücken.
Sollte dies einmal mißlingen, dann mit Gummi-
oder Plasthammer durch leichte gleichmäßige
Schläge nachhelfen, Verkantung beseitigen;
- Paßhülse vorn mit Schlagdorn
11 MW 3-4 26...28 mm tief
einschlagen, damit beide Gehäusehälften
zentriert werden;
|
Bild 66. Dichtring D 25x72x7 montieren
- Beide Gehäusehälften mit 15 Stück
Zylinderschrauben über Kreuz verschrauben;
Achtung:
Keinesfalls vor dem Einschlagen der Paßhülse
die Gehäusehälften verschrauben; die
Paßhülse zentriert das komplette
Gehäuse!
- Lager 6304 JC4 (1) für Abtriebswelle,
Innenlaufring aufheizen und in rechte
Gehäusehälfte, mit Schlagdorn
11 MW 7-4 bis Anschlag
eindrücken;
- Dichtkappe und Lagersitz ausmessen, zwischen
dem Bund der Dichtkappe und dem Lager
muß 0,2 bis 0,4 mm Luft vorhanden sein.
Mit Paßscheiben 40x0,1 (0,2; 0,5; 0,8)
TGL 10404-St ausgleichen;
- Dichtkappe mit Dichtung montieren, dabei
die Senkschrauben mit Dichtmasse einsetzen;
- Kettenrad am Getriebe montieren. Mutter
(SW 24) mit Ringschlüssel und Gegenhalter
05-MW 45-3 anziehen
und mit Sicherungsblech sichern;
- Wellendichtring (2) D 25x72x7 Dichtlippe
ölen und mit Montagehülse (3) und
Eindrückdorn (4) 29-50.406
auf Lichtmaschinenseite eindrücken.
Dichtlippe zum Lager 6306 zeigend;
- Drahtsprengring außen für Wellendichtring
montieren;
- Verschlußstopfen (3 Stück, Gummi) in
die Bohrungen (5) im Lima-Raum einsetzen;
|
Bild 67. Montage der Schaltarretierung
- Wellendichtring D 25x72x7 (1) auf
Kupplungsseite mit Eindrückdorn
29-50.409 eindrücken
(vorher Dichtlippe ölen! Selbige zeigt
nach außen zur Kupplung);
- Drahtsprengring (2) zur Sicherung des
Wellendichtringes montieren;
- Schaltarretierschraube (3) mit Dichtring,
Druckfeder und Kugel einschrauben;
- Schaltarretierhebel (4) auf hervorstehenden
Führungsbolzen (5) aufsetzen, in
Kurvenwalze (6) einrasten und Zugfeder
(7) in Kerbnagel (8) einhängen (Bild
67);
Das anschließende Freischlagen der
Lager wird mittels Gummi- oder Plasthammer,
beiderseits auf das noch heiße
Gehäuse vorgenommen.
Achtung:
Nicht auf Kurbelwellenstümpfe schlagen,
damit würde der Rundlauf der Kurbelwelle
(0,03 mm) nicht eingehalten werden!
- Antriebs- und Abtriebswelle in
Leergangstellung auf Leichtgängigkeit
überprüfen, beide Wellen müssen
gegeneinander freilaufen;
- Fußschalthebel auf Fußschaltwelle
aufstecken und alle Gänge
durchschalten;
4.4. Montage von Kolben, Zylinder und Zylinderdeckel
nächster Punkt ; Index
Über die Auswahl der richtigen Paarung
der Kolben und Zylinder haben wir bereits im Abschnitt
4.1.1. ausführlich informiert.
In diesem Abschnitt handelt es sich nur noch um die
richtige Montage des Kolbens und des Zylinders, sowie
die Einstellung des Verdichtungsverhältnisses.
|
Bild 68. Zylinderbaugruppe
Vor der Montage des Zylinders
überprüfen, ob die Bohrung (B) verschlossen
ist. Wenn nicht, eine Kugel ø 4,5mm einlegen
und den mit Dichtmasse versehenen Gewindestift
einschrauben.
|
Bild 69. Motor fertig zum Zylinderaufbau
Die Zylinderstehbolzen (Z) werden auf
festen Sitz geprüft und das Nadellager für
den Kolbenbolzen ist mit Motorenöl in das
obere Pleuelauge (P) einzusetzen.
Der Kurbelraum ist bis zum Aufsetzen des Zylinders
mit einem sauberen Putztuch zu verschließen,
damit kein Fremdkörper (Sicherungsring für
Kolbenbolzen) in den Kurbelraum gelangt.
4.4.1. Kolben und Zylinder
nächster Punkt ; Index
Zur Montageerleichterung ist der
Kolben auf einer elektrischen Heizplatte auf
ca. 40...50°C zu erwärmen. Vor der Montage
ist auf gleiche Farbmarkierung von Kolben und
Kolbenbolzen zu achten.
Während der Kolben erwärmt wird, ist die
Zylinderfußdichtung (ohne Dichtmasse) auf die
Dichtfläche des Gehäuses aufzulegen.
|
Bild 70. Montage des Kolbens
Die Kolbenunterlage (1) 22-50.412
auf das Gehäuse auflegen und den erwärmten Kolben mit
dem Pfeil zum Auslaßkanal zeigend über das Pleuel stecken.
Der kalte Kolbenbolzen (2) wird auf den ebenfalls kalten
Führungsdorn (3) 05-MW 19-4
aufgesteckt und das konische Ende des Führungsdornes voran
in den Kolben eingeführt. Damit werden Kolben und
Pleuel gefluchtet und das Nadellager bei dem
Eindrücken des Kolbenbolzens nicht beschädigt.
Der Kolbenbolzen muß zügig und ohne Unterbrechung
in den Kolben eingeführt werden, damit die
Erwärmungstemperatur des Kolbens nicht auf den
Kolbenbolzen übertragen wird. Selbiger würde sich
dadurch ausdehnen und im Kolben steckenbleiben.
Ein steckengebliebener Kolbenbolzen darf nur mit der
Ausdrückvorrichtung 22-50.010
nachgedrückt werden. Ein Nachschlagen mit Hammer
und Schlagdorn führt zur Deformierung des Kolbens.
Die beiden stets neuen Sicherungsringe (S) mit einer
Spitzzange einsetzen und auf festen Sitz in den
eingestochenen Nuten des Kolbens achten.
|
Bild 71. Aufsetzen des Zylinders
Die Kolbenringe so drehen, daß die
Arretierstifte zwischen den Ringstößen liegen (Bild
70, lange Pfeile), sonst klemmen die
Kolbenringe im Zylinder und gehen dadurch beim
Aufschieben des Zylinders zu Bruch.
Jetzt den in der Zylinderlaufbuchse leicht geölten
Zylinder über den Kolben schieben. Die Kolbenunterlage (U)
22-50.412 stützt den Kolben ab.
Sie wird entfernt, sobald der Zylinder den Kolben voll
bedeckt. Danach den Zylinder vollständig aufschieben.
4.4.2. Zylinderdeckel und Verdichtungsverhältnis
nächster Punkt ; Index
Der Motor gibt harte Geräusche von sich,
wenn das Verdichtungsverhältnis e = 10,5:1
überschritten wird. Liegt e unter 10,5:1 kann
der Motor seine volle Leistung nicht abgeben.
Bei richtigem Verdichtungsverhältnis hat der Brennraum
etwa 26 cm³ Rauminhalt.
Das Spaltmaß (1) ist auf 0,9...1,2 mm festgelegt. Das
Bild 72 zeigt die Meßmethode. Ein
Bleidraht, am besten eignet sich dafür handelsüblicher
Lötdraht von 2 mm Dicke, wird durch die Zündkerzenbohrung
in den Brennraum eingeschoben. Der über den oberen
Totpunkt hinweggedrehte Kolben drückt den Bleidraht
platt. Ein Meßschieber oder eine Meßschraube stellt
nach dem Herausziehen des Bleidrahtes das vorhandene
Spaltmaß fest.
|
Bild 72. Ausmessen des Spaltmaßes
Der Zylinderdeckel muß bei jedem
Meßvorgang mindestens mit zwei Muttern über
Eck angezogen sein.
(2) = Wasserablaufbohrung.
Ausgleichscheiben (A) in den Dicken 0,2 mm und 0,4 mm
ermöglichen die Korrektur des Spaltmaßes.
Bitte nur Originalscheiben aus Aluminium verwenden und
nach jeder Demontage des Zylinderdeckels durch neue
ersetzen.
Eine Ausgleichscheibe (Minimum 0,2 mm) muß unbedingt
eingebaut sein.
An der Zylinderlaufbuchse ist oben ein Bund (B) im Bild
73 von 1,5 mm angedreht, welcher die
Ausgleichscheiben zentriert und verhindert, daß die
Verbrennungstemperatur direkt an die
Aluminium-Ausgleichscheiben kommt.
|
Bild 73. Montage der Ausgleichscheiben
Nach dem Ausmessen des Spaltmaßes
wird die ermittelte neue Ausgleichscheibe über
den Zentrierbund (B) auf den Zylinder gelegt.
Den Zylinderdeckel aufsetzen und mit Steckschlüssel
(SW 13) die Muttern über Kreuz mit 26 Nm (2,6 kpm)
allmählich festziehen.
|
Bild 74. Dämpfungskämme montieren
Bild 75. Montageprinzip Kupplungsmitnehmer
- Distanzscheibe (1) 1,90 mm; 1,95 mm oder 2,00 mm Dicke
- Nadelkranz (2) KK 22x26x26;
- Kupplungsmitnehmer (3);
- Anlaufscheibe (4) 2,3 mm Dicke;
- Federscheibe (5).
In der genannten Reihenfolge auf
den Kurbelwellenstumpf (Kupplungsseite) auflegen,
dabei die Distanz- und Anlaufscheibe mit der
Hinterdrehung der Innenbohrung zum Bund der
Kurbelwelle aufsetzen.
Achtung:
Der Nadelkranz (2) ist in Tolerierungsgruppen
erhältlich (siehe Abschnitt 4.1.4.)!
Zulässiges Radialspiel des inneren Mitnehmers
mit Antriebsrad (3) beträgt 0,004...0,029 mm.
Einpassung wie Nadellager für Kolbenbolzen
vornehmen (siehe Abschnitt 4.1.3.)
und bei der Montage mit Motorenöl einsetzen.
4.5.3. Axialspiel des Kupplungsmitnehmers messen und einstellen
nächster Punkt ; Index
Mit der Meßvorrichtung 05-ML 13-4
ermittelt man das vorhandene Axialspiel. Die
Meßvorrichtung wird dazu ohne Federscheibe
(5) und Anlaufscheibe (4) (Bild
75) aufgesetzt. Durch axiale
Bewegung des inneren Mitnehmers kann die Axialluft
von der Meßuhr abgelesen werden.
Das Axialspiel des Antriebsrades mit innerem
Mitnehmer ist festgelegt auf 0,05...0,10 mm.
|
Bild 76. Axialspiel des Kupplungsmitnehmers messen
Ist das Axialspiel größer als
0,10 mm, treten bei unbelastetem Motor Geräusche
auf, welche durch die Schrägverzahnung des
Primärtriebes verursacht werden. Der Kupplungsmitnehmer
wird axial durch wechselnde Belastung bewegt. Wird die
Kupplung bei nicht rollendem Fahrzeug und laufendem
Motor gezogen, verschwindet dieses Geräusch
(Primärtrieb steht). Je größer das Axialspiel
des Kupplungsmitnehmers eingestellt wird, um so lauter
wird dieses Geräusch. Im belasteten Zustand des
Motors ist dies nicht vorhanden.
Mit den verschiedenen Distanzscheiben (1) (Bild
75) wird das Axialspiel verändert.
Kleineres Axialspiel als 0,05 mm führt zum Anlaufen
der Distanz- und Anlaufscheiben. Damit kann der Mitnehmer
festlaufen und die Kupplung unterbricht den Kraftfluß
von der Kurbelwelle zum Getriebe nicht mehr. Die
Kupplung kann unter diesen Umständen vom Konus
der Kurbelwelle losgerissen werden.
4.6. Aufbau der Kupplung
nächster Punkt ; Index
- Beide Konen (Kupplungskörper und Kurbelwelle)
ölfrei machen und Tragebild kontrollieren. Trägt
der volle Konus nicht, so kann dieser mit
Schleifpaste eingeschliffen werden.
Dabei das Rillenkugellager 16005 -Kupplungsdrucklager-
schützen und die Reste der Schleifpaste
gründlich entfernen.
Wird die Kupplung zur Kontrolle ohne Federscheibe
(1) und Kupplungsmitnehmer (2) auf den Kurbelwellenstumpf
aufgesetzt, muß der Konus bereits so sitzen, daß
die Kupplung per Hand nicht abgehoben werden kann.
|
Bild 77. Konus der Kupplung kontrollieren
- Die Kupplung aufsetzen. Die Federscheibe (5)
unter der Kupplung sorgt durch ihre Federkraft
für den Festsitz der Anlaufscheibe (4) (Bild
75). Die Vorspannung der Federscheibe
ist gut, wenn beim Aufsetzen der Kupplung (vor
dem Anziehen) die Kupplung im Konus noch nicht
festsitzt und leicht kippt.
- Vor dem Aufbau des Kupplungsdeckels ist die
Kupplung mit Hilfe eines Distanzrohres (A) fest
anzuziehen.
|
Bild 78. Kupplung anziehen
Bild 79. Einzelteile der Kickstarteranlage
Die Kickstarterwelle in der
Zahlenreihenfolge des Bildes 79
montieren. Den Mitnehmer (3) so aufstecken, wie
es im Bild 80 links gezeigt wird.
Der rechte Teil des Bildes 80
zeigt eine falsch montierte Kickstarterwelle.
|
Bild 80. Richtige Montage des Mitnehmers (links)
Das Kickstarterrad (6) wird vor dem
Einsetzen der 24 Lagernadeln (7) 2,5x19,8 mit Fett
versehen und bis zum Anliegen an die Anlaufscheibe
(5) auf die Kickstarterwelle (1) geschoben.
Zum Schluß die Kickstarterfeder (10) montieren.
Das Federende muß bis zum Anschlag in die Bohrung
(A) der Kickstarterwelle geschoben Werden. Bild
81 zeigt die einbaufertige
Kickstarterwelle.
|
Bild 81. Kickstarterwelle komplett
Die vormontierte Kickstarterwelle
wird nun am Lagerzapfen, unterhalb des Kickstarterrades,
zwischen Kupferbacken oder Holzbeilagen in einen
Schraubstock, siehe Bild 83,
eingespannt.
Die Gummiringe zur Abdichtung der Kickstarter- und
Fußschaltwelle in die im Kupplungsdeckel vorgesehenen
Ausdrehungen einsetzen, leicht ölen und den
Kupplungsdeckel von oben auf die Kickstarterwelle
aufsetzen. Das Federende der Kickstarterfeder ist
dabei in die im Kupplungsdeckel vorgesehene Bohrung
(B) einzudrücken.
|
Bild 82. Einbaulage der Kupplungsfeder
Der Kupplungsdeckel wird jetzt um
etwa 1 1/4 Umdrehung nach links gedreht und die
Keilschraube durch den inzwischen aufgesteckten
Kickstarterhebel gesteckt und verschraubt (Bild
83).
|
Bild 83. Kickstarterhebel befestigen
4.7.2. Kupplungsbetätigung montieren (siehe Bild 21 und Bild 87)
nächster Punkt ; Index
Die Lagerbuchse (17) mit dem Stützlager
6302 der Kurbelwelle (gehalten durch den Sprengring)
von außen in den Kupplungsdeckel schieben, die
Markierungen (M), siehe Bild 85,
müssen nach oben zeigen. Den Druckhebel (16)
danach von innen in die Gewindeschnecke der Lagerbuchse
bis zum Anliegen eindrehen und die Zugspindel (19)
einhängen.
4.7.3. Anbau des Kupplungsdeckels
nächster Punkt ; Index
Nach der Komplettierung des
Kupplungsdeckels wird die Dichtung auf die gereinigte
Dichtfläche (ohne Dichtmasse) gelegt und der
Kupplungsdeckel aufgesetzt.
Wie im Bild 84 gezeigt, wird das
Nockenblech der Zwangsausspurung mit der Nase (1)
in das Gehäuse eingesetzt.
|
Bild 84. Richtige Lage des Nockenbleches
Die Gehäuseschraube (2) hält das
Nockenblech unten fest.
Zur besseren Übersicht wurde der Kupplungsdeckel im
Bild 84 nicht mit gezeigt, dieses
Bild zeigt nicht den Montagezustand.
Den Kupplungsdeckel durch leichte Prellschläge
mittels Gummihammer zur Dichtfläche schlagen,
dabei die Kickstarterwelle kurz nach rechts drehen,
damit das Kickstarterrad in das Zahnrad 1. Gang
einrasten kann.
Die 5 Stück Gehäuseschrauben unter Verwendung
neuer Dichtringe einsetzen und damit den Kupplungsdeckel
über Kreuz gleichmäßig anziehen.
4.7.4. Kupplungsgrobeinstellung
nächster Punkt ; Index
Bevor die Kupplungseinstellung an
der Lagerbuchse des Kupplungsdeckels durchgeführt
werden kann, muß vorher die Kupplung über das
Stützlager der Lagerbuchse im Kupplungsdeckel
angezogen werden. Dazu wird die Federscheibe B14
auf den Kurbelwellenstumpfen aufgelegt und das
Antriebsrad für Drehzahlmesser bzw. bei der
Standardausführung die Mutter M 14x1,5 (SW 22)
mit einem Anzugsmoment von 80...100 Nm (8...10
kpm) angezogen.
Über die Zugspindel (Z), siehe Bild 87,
nun das Rohr (1) schieben. Rohr (1) und die
Zugspindel (Z) werden durch den in die Bohrung
für die Aufnahme des Seilzuges gesteckten Bolzen
(2) von ø 8mm verbunden. Anschließend die
Lagerbuchse (3) bis zum Anliegen des Rohres (1) am
Kupplungsdeckel verdrehen (Pfeil a). Damit ist
die Grundeinstellung des Druckstückes (D) mit
A = 11 mm festgelegt.
|
Bild 85. Grobeinstellung der Kupplung
Bild 86. Rohr zur Grobeinstellung der Kupplung
Nach dem Grobeinstellen der
Kupplung sofort die Stellplatte (18), siehe
Bild 21, aufstecken und das
Gehäuse für Drehzahlmesserantrieb mit
Dichtring montieren. Erst danach ist die
Grobeinstellung fixiert.
Achtung:
Zur Befestigung des Gehäuses für
Drehzahlmesserantrieb nur Schrauben M 6x25
verwenden.
Längere Schrauben beeinträchtigen
die Funktionsfähigkeit der
Kupplungsbetätigung!
|
Bild 87. Erläuterung der Kupplungsgrobeinstellung
4.7.5. Kupplungsfeineinstellung
nächster Punkt ; Index
Die Kupplungsfeineinstellung wird an
der Stellschraube des Kupplungshebels am Lenker
durchgeführt.
Das Kupplungsspiel am Kupplungshebel soll 2...3
mm betragen.
Bei auftretendem Rutschen der Kupplung ist
grundsätzlich erst die Grobeinstellung zu
überprüfen, bevor die Kupplung ausgewechselt
wird.
4.8. Antrieb für Drehzahlmesser
nächster Punkt ; Index
Der Antrieb des Drehzahlmessers für
die Luxusausführung erfolgt mechanisch direkt
von der Kurbelwelle auf die Kupplungsseite.
|
Bild 88. Drehzahlmesserantrieb
Anstelle der Befestigungsmutter
M 14x1,5 zur Befestigung der Kupplung wird das
Antriebsrad für Drehzahlmesserantrieb (1),
welches auf einem zusätzlichen Bund der
Kurbelwelle zentriert wird, verwendet.
Im Gehäuse für Drehzahlmesserantrieb
(2) ist die Antriebswelle (3) komplett in einem
Kunststoffstopfen (4) gelagert, welchen eine
Zylinderkopfschraube (5) mit Wellscheibe (6)
arretiert.
Der Drehzahlmesserantrieb ist wartungsfrei, er
wird bei der Montage mit Molybdändisulfidfett
eingesetzt.
4.9. Ölverlauf zur Schmierung der Kurbelwellenhauptlager und Wellendichtringe (siehe Bild 60)
nächster Punkt ; Index
Die beiden Kurbelwellenhauptlager
6306 werden von der auch den Kurbelraum passierenden
Kraftstoff-Öl-Mischung geschmiert. Die
Mischungsschmierung bietet den Vorteil, daß
die Lager ständig neues und sauberes Schmieröl
erhalten.
Im Kurbelraum wurde eine Ölfangtasche (4),
die über beide Gehäusehälften reicht,
angebracht. Damit beide Lager gleichmäßig
mit Öl versorgt werden, wurde die Ölfangtasche
(4) in der Mitte (Gehäusetrennfuge) durch eine
Öltrennscheibe (5) aus Gummi, welche bei der
Montage vor dem Aufsetzen der rechten Gehäusehälfte
eingelegt wird, getrennt. Das in der Ölfangtasche (4)
gesammelte Schmieröl läuft über je eine
Ölbohrung (6) in den Raum zwischen Ölleitscheibe
(7) und Wellendichtring. Dieser freie Raum wird
während des Motorlaufes bis zur Unterkante der
Bohrung in der Ölleitscheibe ständig gefüllt
und versorgt so die Gleitstelle Wellendichtring
- Kurbelwellenzapfen.
Nachdem das Öl den Wellendichtring versorgt hat,
schmiert und kühlt es das Kurbelwellenhauptlager.
4.10. Schmierung des Getriebes
nächster Punkt ; Index
Durch das Abtriebsrad (68 Zähne)
wird ein Teil des Öles aus dem Kupplungsraum in
die Ölfangtaschen der linken Gehäusehälfte
(Ö, Bild 59) hochgepumpt.
Von diesen Fangtaschen aus läuft das Öl
einmal in das Ölleitblech (L, Bild
57) und durch im Ölleitblech
vorhandene Bohrungen direkt auf die Verzahnung
der Getrieberäder und von der hinteren
Fangtasche über den nach oben offenen Sprengring
in das Ölfangblech der Abtriebswelle (Pfeil A,
Bild 59). Durch die angebohrte
Abtriebswelle gelangt das Öl zur Lagerstelle
der Losräder des 2. und 3. Ganges und
schmiert diese.
4.11. Montagefehler
nächster Punkt ; Index
Wird die Montage des Motors mit
kalten Gehäusehälften durchgeführt, werden
die Lagersitze im Gehäuse gewaltsam zerstört.
Die Lageraußenringe drehen sich dann im Gehäuse.
Ebenso führt der, zwangsläufig gewaltsame, Einbau
von Getriebewellen bzw. der Kurbelwelle in kalte,
d.h. für die Montage zu enge Lagerinnenringe,
zu Verspannungen in den Lagern und evtl. auch
zu unzulässig großem Radialschlag dieser
Wellen.
Daraus resultieren z.B. Schaltfehler des Getriebes,
unkorrekter Motorlauf durch schlecht einstellbare
Vorzündung, vorzeitiger Verschleiß von
Baugruppen und Bauteilen usw.
4.12. Einbau des Motors in das Fahrgestell
nächster Punkt ; Index
Beim Einbau des Motors in das
Fahrgestell nach den Abschnitten 3.1.1.
bis 3.1.4. in umgekehrter Reihenfolge
vorgehen. Jede Motorinstandsetzung zieht auch die
Einstellung der Zündung und des Vergasers nach sich.
Darüber sind in den Abschnitten 6.5.3.
und 7.1.4. nähere Einzelheiten
erläutert.
5. Fahrgestell
nächster Punkt ; Index
|
Bild 89. Explosivdarstellung Fahrgestell
Bild 90. Hinterradfederung
Der allgemeine Aufbau, soweit er
nicht schon aus den Bildern 1
und 2 erkenntlich ist, geht aus
der Explosivdarstellung des Fahrgestelles, Bild
89, hervor. Nachstehend werden
wichtige Einzelheiten bzw. Reparaturhinweise
verschiedener Fahrgestellbaugruppen näher
erläutert.
5.1. Hinterradfederung und elastische Motorlagerung hinten
nächster Punkt ; Index
Das Bild 90 zeigt
den Aufbau der Hinterradfederung. Zur Hinterradfederung
gehören die Hinterradschwinge, deren Lagerung mit der
hinteren Motoraufhängung kombiniert ist und die
Federbeine.
5.1.1. Lagerung der Hinterradschwinge
nächster Punkt ; Index
Das tragende Teil der Lagerung ist
der Schwingenlagerbolzen (11), der mit dem
Rahmenlagerrohr (10), dem rechten und linken
Innenrohr (1) und (2), sowie den 3 AnlaufScheiben
(16) im Rahmen geklemmt wird. Anzugsmoment der
Sechskantmutter(17) 70...80 Nm (7...8 kpm).
Den Schwingenlagerbolzen nur bei voll ausgefederter
Schwinge anziehen.
|
Bild 91. Schwingenlagerung
1. | Rechtes Innenrohr, 54 mm lang |
2. | Linkes Innenrohr, 44 mm lang |
4. u. 5. | Gummibuchse, 25 mm lang |
8. | Abstandshülse, 10 mm lang (Polyamid) |
9. | Hinterradschwinge |
10. | Rahmenlagerrohr |
11. | Schwingenlagerbolzen |
12. | Lagergummi |
13. | Abstandsring (Polyamid) |
14. | Motorschuh, rechts |
15. | Motorschuh, links |
16. | Anlaufscheibe |
17. | Sechskantmutter M 18x1,5 |
18. | Stellring |
19. | Rille zum Einhängen der Kippständerfeder |
Die Schwingenlagerung ist nach der
Montage völlig wartungsfrei.
Die Hinterradschwinge (9) wird als Ersatzteil von
unserem Ersatzteilvertrieb komplett mit den
eingedrückten Gummielementen ausgeliefert.
Für den Betrieb mit Seitenwagen sind geänderte
Schwingen und Lagerbolzen zu verwenden.
5.1.2. Auswechseln der Gummilagerung - Hinterradschwinge
nächster Punkt ; Index
- Ausdrücken der Innenrohre (1) und (2)
mit Hilfe des Dornes (3) auf einer Dornpresse;
- Entfernen des Stützringes (8);
|
Bild 92. Montage der Gummilager
- Aufschneiden und Herausdrücken der
Gummibuchsen (4) und (5);
- Eindrücken der neuen Gummibuchsen (4)
(in trockenem Zustand) mit dem Dorn von den
Außenseiten der Schwinge, dabei den Zwischenring
(7) unterlegen. Für das linke Schwingenauge
den kurzen und für das rechte Schwingenauge den
längeren zylindrischen Ansatz des Dornes (6)
verwenden;
- Einsetzen des Stützringes (8) - 10mm breit,
in das rechte Schwingenauge von außen;
- Auf das zylindrische Ende des Dornes (3) das
Innenrohr (1), 54 mm lang, bzw. (2), 44 mm lang,
aufschieben und mit dem konischen Ende voran den
Dorn in die mit Seifenwasser angefeuchteten
Gummibuchsen eindrücken, bis das Innenrohr
gleichmäßig an beiden Seiten des Schwingenrohres
herausragt.
5.1.3. Aus- und Einbau des Schwingenlagerbolzens
nächster Punkt ; Index
Den Stellring (18) und die
Sechskantmutter (17) links entfernen,
Schwingenlagerbolzen nach rechts mit Hilfsdorn
herausschlagen und den Hilfsdorn zur Zentrierung
der Schwinge stecken lassen (siehe Bilder
91 und 93).
|
Bild 93. Skizze für Hilfsdorn
Bei Einbau des Schwingenlagerbolzens
ist selbiger zu fetten, damit er nicht festrostet.
Auf den Schwingenlagerbolzen die Sechskantmutter rechts
aufdrehen bis Gewindeende.
Den Schwingenlagerbolzen jetzt von rechts nach links
durchschieben, der Hilfsdorn steckt noch in der Schwinge.
Linke Sechskantmutter mit 70...80 Nm (7...8 kpm) anziehen
(Schwinge voll ausgefedert) und Stellring kontern.
5.1.4. Montage der hinteren Schwinge einschließlich Motoraufhängung
nächster Punkt ; Index
- Lagergummi, Abstandsring und Motorschuhe
links und rechts auf das Rahmenlagerrohr
aufschieben;
- Motorschuhe mit Hilfe der Druckringe axial
auf die Länge des Rahmenlagerrohres zusammendrücken
(siehe Bild 94);
|
Bild 94. Motorschuhe durch Druckring (D) und
Zugspindel (Z) mit Gewinde M6 axial zusammengedrückt,
Hinterradschwinge aufgeschoben
- Hinterradschwinge mit Anlaufscheiben
von hinten auf die Motorschuhe aufschieben,
bis zum Anschlag an den Druckringen.
Druckringe entfernen und Schwinge bis Mitte
der Bohrung für Lagerbolzen weiterschieben;
- Hilfsdorn von links eindrücken und damit
die Lagerung zentrieren;
- Auf die Schwingenlagerbolzen rechte
Befestigungsmutter bis Gewindeende aufdrehen.
- Schwingenlagerbolzen fetten und von rechts
nach links eindrücken;
|
Bild 95. Hinterradschwinge in Pfeilrichtung aufschieben,
Druckringe bereits entfernt
- Linke Sechskantmutter mit 70...80 Nm (7...8 kpm)
anziehen (Schwinge voll ausgefedert) und Stellring
kontern.
|
Bild 96. Skizze für Druckring
5.1.5. Hintere Motoraufhängung (Bild 91)
nächster Punkt ; Index
Die Lagergummis (12) und Abstandsringe
(13) der hinteren Motoraufhängung können
nur bei ausgebautem Motor und Hinterradschwinge
entsprechend des vorangegangenen Abschnitts
gewechselt werden.
Die Verschleißgrenze ist erreicht, wenn die
Motorschuhe im eingebauten Zustand keine Vorspannung
mehr haben und von Hand seitlich hin und her bewegt
werden können.
Beim Erneuern der Lagergummis (12) und Abstandsringe
(13) ist zu prüfen, ob auch die Lagermanschetten
der Motorschuhe Verschleißerscheinungen zeigen.
Wenn in der Bohrung dort, wo der Abstandsring anliegt,
ein spürbarer Absatz vorhanden ist, wird im
Interesse einer ausreichenden Lebensdauer der neuen
Gummi- und Abstandsringe das Miterneuern der Motorschuhe
empfohlen.
5.1.6. Federbeininstandsetzung
nächster Punkt ; Index
Die Instandsetzung beschränkt
sich auf das Auswechseln defekter Federbeinteile
und die Schmierung der Verstellmuffen der hinteren
Federbeine.
Die Stoßdämpfer sind komplett auszutauschen
und der Regenerierung zuzuführen. Eine
Selbstreparatur der Stoßdämpfer ist nicht
möglich. Bei Ölverlust kann die fehlende
Menge zwar nachgefüllt werden (Spezialschlüssel
05-MW 82-4), in den meisten
Fällen wird aber die Abdichtung der Kolbenstange
defekt sein - der Stoßdämpfer muß
zur Regenerierung.
Stoßdämpferkennzeichnung
Die Kennzeichnung befindet sich oberhalb des
unteren Befestigungsauges.
Beispiel: A 22 - 100 - 88/8 M 1.50/1
Darin bedeuten:
A 22 | Bauart |
100 | Nennhub in mm |
88 | Dämpfkraft in Zugrichtung in kp |
8 | Dämpfkraft in Druckrichtung in kp |
M | mit Verstellung |
1.50/1 | Herstellernummer |
Ab Juni 1978 entfallen die
Buchstaben OV bzw. MV. Mit Verstellung wird
durch "M" gekennzeichnet.
Ausbau der Stoßdämpfer
Unteres Federbeinauge in den Schraubstock
spannen. Die Schutzhülse (8) niederdrücken
und die beiden Stützringhälften (1)
herausnehmen. Jetzt können die Teile
(8), (9) und (11) abgenommen werden.
Mögliche Stoßdämpferdefekte
- Der Stoßdämpfer ist wirkungslos ohne
sichtbaren Ölverlust (Fremdkörper
zwischen den Membranen des Kolbenventils).
- Die Dämpfung setzt nicht weich, sondern
ruckartig ein - die Federbeine "stempeln"
(zu wenig Dämpfungsflüssigkeit vorhanden oder
Bodenventil undicht).
- Dämpfungsflüssigkeit läuft aus.
Nachfüllen von Stoßdämpferöl
Mit einem Spezialschlüssel
05-MW 82-4 das Gewindestück
(4 im Bild 97) herausdrehen und die
Dämpfungseinrichtung herausziehen. Alle Teile in
Waschbenzin reinigen und neues Öl auffüllen.
Das Gewindestück mit etwa 49 Nm (5 kpm) anziehen.
Stoßdämpferpaarung
Zur Gewährleistung guter Straßenlage
müssen die Stoßdämpfer einer Achse gleiche
Dämpfungswerte aufweisen.
Die Kennzeichnung der Toleranzgruppe befindet sich
an der oberen Stirnseite der Kolbenstange (7 im
Bild 97).
Ein grüner Farbpunkt bedeutet negative
Abweichung vom Nennwert der Dämpfkraft.
Ist keine Farbkennzeichnung vorhanden, handelt es
sich um positive Abweichung. Es sind stets
gleich gekennzeichnete Stoßdämpfer zu paaren.
|
Bild 97. Aufbau des Stoßdämpfers
- Stützringhälften
- entfällt
- Anschlaggummis
- Gewindestück mit Radialdichtring AC 10x19x7
- Kolben mit Rückschlagventil (oben) und Dämpfungsventil (unten)
- Bodenventil mit Abstützring
- Kennzeichnung für Toleranzgruppe
- Schutzhülse
- Druckfeder
- Kolbenrohr
- Verstellmuffe
Federn für Federbeine
Bezeichnung | Maß- ein- heit | Solo | Gespann |
Länge (entspannt) | mm | 260+8 | 260+8 |
Außendurchmesser der Feder | mm | 55-0,8 | 55-0,8 |
Drahtdurchmesser | mm | 7 | 7 |
Windungen | An- zahl | 16,5 | 17,5 |
Federkonstante | N/mm | 15,23 | 17,304 |
Die Ersatzteilfeder für die
Soloausführung wird nicht gekennzeichnet.
Die Ersatzteilfeder für die Gespannausführung
trägt an der mittleren Windung eine weiße
Farbkennzeichnung.
5.2. Motoraufhängung am Zylinderdeckel
nächster Punkt ; Index
Der Aufbau der elastischen
Motoraufhängung vorn geht aus Bild
89 hervor. Für die Reparatur
bzw. das Austauschen der Motoraufhängung vorn
ist es zweckmäßig, den Vergaser einschließlich
Ansaugstutzen auszubauen und das Zündkabel
abzunehmen.
Die Auspuffanlage kann am Motor verbleiben, es
muß lediglich die Verbindungsschraube zwischen
hinterer Auspuffschelle und Auspuffstrebe gelöst
werden.
Nach dem Abschrauben der beiden Muttern M8 vom
Zylinderdeckel den Motor in die im Bild
98 ersichtliche Stellung absenken.
Nun noch die zur Befestigung der vorderen
Aufhängung am Rahmen dienende Mutter M10
lösen, und alle Einzelteile lassen sich
abnehmen.
Bei der Montage auf sichere Verschraubung
achten!
|
Bild 98. Auswechseln der elastischen Motoraufhängung am Zylinderdeckel
5.3. Teleskopgabel
nächster Punkt ; Index
Anhand der Bilder 99
und 100 ist der Aufbau und
die Zusammengehörigkeit der Einzelteile der
Teleskopgabel ersichtlich. Die Reparatur
einzelner Baugruppen wird nachfolgend einzeln
beschrieben.
|
Bild 99. Explosivdarstellung der Teleskopgabel
Bild 100. Teleskopgabel und Lenkungslagerung (Schnittzeichnung)
Linker Gabelholm:
Voll eingefedert, Federweg = 185
Ausführung mit Schutzbalg
Rechter Gabelholm:
Voll ausgefedert, Ausführung mit Schutzkappe
- Mutter für Steuerrohr
- Oberer Klemmkopf
- Verschlußschraube
- Lenkungslager 6006
- Unterer Klemmkopf
- Druckfeder (Solo Federdraht ø 4,0 mm,
Seitenwagen Federdraht ø 4,5 mm)
- Schutzbelag
- Kolbenring am Stützrohr
- Stützrohr
- Gleitrohr
- Führungsrohr
- Schutzkappe
- Radialdichtring 35x47x7
- Anschlagscheibe, Dicke 2,0 mm, und Sicherungsring
- Ventilscheibe, Drossel und Sprengring
- Scheibe für Endanschlag
- Druckfeder für Endanschlag
- Dichtscheibe
5.3.1. Lenkungslagerung
nächster Punkt ; Index
Die Lagerung der Lenkung
übernehmen zwei Radialrillen-Kugellager
6006, zwischen denen eine Distanzhülse
eingebaut ist. Diese Lagerung ist völlig
wartungsfrei.
Bei der Montage und auch später brauchen
keine Einstellungen vorgenommen zu werden.
Der Einbau der Lenkung wird folgendermaßen
durchgeführt:
- Die Kugellager 6006 mit Wälzlagerfett füllen;
- Unteres Lager bis zum Anschlag auf den Außenring
drücken, dabei einen Zwischenring ø 54x20
verwenden;
- Distanzhülse einlegen;
- Oberes Lager bis zum Anschlag des Innenringes auf
die Distanzhülse drücken.
Dabei beachten:
Unter das untere Lager einen Distanzring
ø 54x40 mm legen, damit das untere Lager
nicht mit herausgedrückt wird und ebenfalls über
den Distanzring ø 54x20 mm das obere Lager
hineindrücken.
Achtung: Bei der späteren
Montage des unteren und oberen Klemmkopfes ist
darauf zu achten, daß die Mutter für Steuerrohr
(1), Bild 100, mit einem
Anzugsmoment von 150 Km (15 kpm) angezogen wird!
Danach muß die Lenkung leichtgängig sein und
darf in keiner Lenkstellung klemmen. Sollte dies
einmal der Fall sein, so ist die Distanzhülse,
zwischen den Innenlaufringen der Lager sitzend,
auszuwechseln (zu kurze Distanzhülse führt zur
Verspannung der Lager).
Der Ausbau der Lenkungslager aus dem Rahmen
erfolgt nach den Bildern 101 ...
103 mit Hilfe der Abziehvorrichtung
22-51.006.
Der dazu erforderliche Aus- und Einbau der
Teleskopgabel wird im Abschnitt
5.3.2. erläutert.
|
Bild 101. Innenteil der Abziehvorrichtung in das Kugellager eindrücken
Bild 10 . Oberteil der Abziehvorrichtung aufsetzen
Bild 103. Schraube eindrehen, anziehen und damit das Lager aus dem Rahmen herausziehen
5.3.2. Kriterien für die Demontage der Teleskopgabel
nächster Punkt ; Index
Die Demontage der Teleskopholme
wird erforderlich:
- Wenn durch einen Unfall die Führungsrohre
verzogen sind. Die Teleskopgabel klemmt beim
Einfedern.
Achtung:
Die Teleskopgabel klemmt im eingefederten
Zustand, auch wenn die Gabelholme nicht
parallel stehen!
Ursache:
Die Klemmschraube der Steckachse wurde vor
dem Anziehen der Steckachsenmutter geklemmt.
Dadurch werden beide Gabelholme verspannt.
- Wenn die zulässige Verschleißgrenze
zwischen Führungsrohr und Gleitrohr
erreicht ist.
Prüfmethode:
Das Fahrzeug steht auf dem Kippständer,
die Teleskopgabel ist voll ausgefedert.
Beide Gleitrohre werden an der Achsaufnahme
vor und zurück bewegt. Die maximale Luft
darf 2,2 mm nicht überschreiten (Neuzustand
0,8...1,2 mm). Bei dieser Messung dürfen
die beiden Gabelholme nicht verspannt sein,
weil dann das vorhandene Spiel verringert wird.
In Zweifelsfällen sind die kompletten
Gabelholme auszubauen, die Führungsrohre
in "weiche Schutzbacken" einzuspannen
und das vorhandene Spiel an den Achsaufnahmen
mit einer Meßuhr zu messen.
- Wenn die Teleskopholme Öl verlieren
(Radialdichtringe im Gleitrohr undicht).
Ölstandskontrolle: Siehe Bild 114.
- Wenn die hydraulische Öldämpfung bei voller
Ölfüllmenge ungenügend ist.
- Wenn die Schutzkappen oder Schutzbälge gewechselt
werden müssen.
5.3.3. Ausbau und Einbau der kompletten Teleskopgabel (siehe auch Bild 100)
nächster Punkt ; Index
Der Ausbau der kompletten Teleskopgabel
ist ohne Lösen von Kabelverbindungen möglich.
Es empfiehlt sich folgende Reihenfolge:
- Handbremsseilzug am Lenker aushängen
bzw. Bremsschlauch vom Bremssattel
lösen. Den Schlauch aus dem unteren
Klemmköpf ziehen, seine Öffnung mit
einem geeigneten Stopfen verschließen
und am Lenker befestigen.
- Abdeckkappe für Steuerrohrbefestigungsmutter
bzw. Lenkungsdämpfer demontieren.
- Mutter für Steuerrohr und Verschlußschrauben
der Führungsrohre mit Steck- oder flachem
Ringschlüssel lockern.
- Scheinwerfer demontieren (komplett).
- Instrumentenhalter abnehmen, den Lenker
auf Kraftstoffbehälter ablegen.
- Vorderrad, Bremssattel und Vorderradkotflügel
ausbauen.
- Blinkleuchten, vorn, einschließlich deren
Halter vollständig demontieren.
- Mutter für Steuerrohr und Verschlußschrauben
abdrehen.
- Oberen Klemmkopf nach oben und unteren
Klemmkopf mit Teleskopholmen nach unten
vorsichtig ausschlagen.
Achtung:
Die herabhängenden Instrumentenhalter,
Blinkleuchten, Scheinwerfer und den Lenker
so sichern, daß nichts beschädigt wird
und die Kabel nicht herausgezogen werden!
Der Einbau der kompletten Teleskopgabel
erfolgt in umgekehrter Reihenfolge. Dabei
ist auf richtiges Verlegen der Kabelbäume
zu achten. Die Scheibenbremse muß nach dem
Anschließen des Bremsschlauches entlüftet
werden.
Die Schraubverbindungen sind nach der
Montage in folgender Reihenfolge
anzuziehen (Bild 104):
- Mutter für Steuerrohr (1), Anzugsmoment
150-30 Nm
(15-3 kpm);
- Verschlußschrauben (2), Anzugsmoment
150-30 Nm
(15-3 kpm);
|
Bild 104. Reihenfolge beim Anziehen der Schrauben
Achtung:
Die Verschlußschrauben am Außengewinde
mit Klebelack "Chemisol 1405" (Hersteller: VEB
Schuh-Chemie, Erfurt) einsetzen (alte Dichtmasse
entfernen).
Außerhalb der DDR ist Gummilösung zu verwenden.
Keine Dichtmasse in die Führungsrohre kommen
lassen, die Stirnseiten der Verschlußschrauben
von Dichtmasse befreien.
- Klemmschrauben (3) am unteren Klemmkopf
20 Nm (2 kpm);
- Mutter für Steckachse (4) 80 Nm (8 kpm);
- Klemmschraube für Steckachse (5), bei
eingefederter Teleskopgabel 20 Nm (2 kpm).
5.3.4. Aus- und Einbau der Teleskopholme (Gabelholme)
nächster Punkt ; Index
Zum Ausbau der einzelnen
Teleskopholme brauchen Lenker, Scheinwerfer
und Instrumentenhalter nicht demontiert zu
werden. Auch das Bremssystem der Scheibenbremse
kann geschlossen bleiben. Beim Ausbau des rechten
Holmes ist jedoch der Bremssattel vom Gleitrohr
zu demontieren und an geeigneter Stelle bis zur
Montage zu befestigen. Das Bild 105
ist nur zur besseren Übersicht ohne die
genannten Teile aufgenommen worden.
|
Bild 105. Ein- und Ausbau der Teleskopholme
- Verschlußschrauben (1) entfernen;
- Vorderrad ausbauen;
- Vorderradkotflügel abbauen;
- Führungsrohre unmittelbar unterhalb des
unteren Klemmkopfes markieren;
- Klemmschrauben (2) lösen;
- Führungsrohre komplett mit Gleitrohren
nach unten herausziehen, dabei Montageschlüssel
19 MW 22-1 (3) verwenden.
Den Einbau in umgekehrter
Reihenfolge ausführen.
Dabei die Schrauben, wie im Abschnitt
5.3.3. erläutert,
anziehen.
5.3.5. Demontage der ausgebauten Teleskopholme
nächster Punkt ; Index
Nachdem die Schutzkappen oder
Schutzbälge vom Gleitrohr entfernt wurden,
wird eine äußerliche Reinigung der
Teleskopholme vorgenommen, die Druckfedern
(im Führungsrohr steckend) nach oben
herausgezogen und die Dämpfungsflüssigkeit
ausgekippt.
Die Demontage erfolgt nun in folgender
Reihenfolge:
- Mit einem Rohrsteckschlüssel (SW 10)
die Befestigungsmutter (1) für das
Stützrohr lösen und diese sowie die
Wellscheibe (2) abnehmen (Bild
106);
|
Bild 106. Befestigungsmutter für Stützrohr entfernen
- Sollte sich beim Lösen oder Anziehen der
Befestigungsmutter des Stützrohres selbiges
mitdrehen, dann mit einem Schraubendreher durch
den Steckschlüssel das Stützrohr arretieren;
- Das Führungsrohr (A) aus dem Gleitrohr (B)
herauszeihen.
|
Bild 107. Führungsrohr aus dem Gleitrohr herausgezogen
- Hinweis!
Unbedingt beachten - beim Einspannen der
Führungsrohre (A) in den Schraubstock nur weiche
Schutzbacken verwenden und nur im oberen Drittel
einspannen.
Die Gleitrohren (B) dürfen nur an der
Achsaufnahme oder an den Befestigungsnaben
für den Kotflügel bzw. den Bremssattel
eingespannt werden!
- Dichtscheibe (3), Druckfeder (4) ø19 mm
und Napf für Endanschlag (5) vom Stützrohr
(6) abnehmen;
- Das Stützrohr (6) in das Führungsrohr (A)
hineinschieben;
- Den Rundring 32x1,6 (Bild 108)
aus dem Führungsrohr entfernen. Die hinter
dem Rundring liegende Drossel (3) besitzt
eine Ausfräsung am äußeren Durchmesser,
damit der Rundring mit Hilfe eines kleinen
Schraubendrehers leicht herausgedrückt
werden kann. Die Drossel (3), die Ventilscheibe
(4) und die Druckfeder für Ventilscheibe (5)
entfernen (siehe Bild 109;
|
Bild 108. Rundring aus Führungsrohr herausdrücken
Bild 109. Drossel, Ventilscheibe und Feder ausbauen
- Das Bild 109 wurde zum besseren
Verständnis mit nicht hineingeschobenem
Stützrohr aufgenommen;
- Jetzt den hinter der Ventilfeder sitzenden
Sicherungsring (1) und die darunter liegende
Anschlagscheibe (2) entfernen (Bild
110).
|
Bild 110. Anschlagscheibe (2 mm dick) entfernen
- Mit Hilfe eines Rundholzes (Besenstiel, etwa 600mm
lang) das Stützrohr nach unten herausschieben.
Nicht über das Innengewinde des Führungsrohres
schieben, dies bedeutet Beschädigung des
Kolbenringes auf dem Stützrohr.
5.3.6. Montage der ausgebauten Teleskopholme mit Verschleißuntersuchung
nächster Punkt ; Index
Grundbedingung für eine einwandfreie
Funktionsfähigkeit der Telekopgabel nach der Montage
ist ein sauberer Arbeitsplatz. Schmutz- und
Staubrückstände an den zu montierenden Teilen
führen zum vorzeitigen Verschleiß und Ausfall
der Teleskopgabel.
Die Montagearbeiten werden in folgender
Reihenfolge durchgeführt:
- Der Wellendichtring ist bei einer vor
der Demontage dichten Teleskopgabel auf
Verschleiß der Dichtlippe und auf richtigen
Sitz der Stützfeder (Zugfeder unter der
Dichtlippe) zu untersuchen. Im Zweifelsfalle
ist es besser, den Wellendichtring
auszuwechseln;
|
Bild 111. Wellendichtring eindrücken
Montagehinweis:
Den Wellendichtring nur mit dem
Schlagdorn (1) 11 MW 7-4
eindrücken.
Nicht einschlagen! Dabei kann die Feder
des Dichtringes abspringen. Die Dichtlippe zeigt
bei der Montage zum Dämpfungsöl, die
geschlossene Seite des Wellendichtringes nach
oben.
- Das Führungsrohr (A), Bild 109,
auf Chrombeschädigungen, Riefen und Verbiegung
überprüfen. Im Zweifelsfalle Rundlauf prüfen.
Zulässiger Rundlaufschlag 0,05 mm.
Ein Nachbiegen oder Nachrichten ist nicht
gestattet;
|
Bild 112. Kontrolle des Stützrohres
- Das Stützrohr (2, Bild 112)
auf Beschädigung überprüfen. Der Miramid-Kolbenring
(Pfeil) darf auf der Dichtfläche keine Riefen
haben, da sonst der Dämpfungsdruck zu niedrig
wird. Die Dämpfungsbohrung (1) des Stützrohres
muß gratfrei sein, und sie darf im Durchmesser
nicht verändert werden;
- Das Stützrohr (2), Bild 112,
wird in das geprüfte Führungsrohr (A) von
unten (Ventilseite) eingeschoben, der
Miramid-Kolbenring vorher mit Stoßdämpferöl
eingesetzt.
Nach Bild 111 die Anschlagscheibe
(2) und den Sicherungsring (1) montieren. Auf
einwandfreien Sitz des Sicherungsringes achten.
Die Druckfeder (5) mit dem Durchmesser 27 mm
an den Sicherungsring anlegen und Ventilscheibe
(4) mit geschliffener Seite zur nachfolgenden
Drossel zeigend einsetzen. Danach die Drossel (3)
auf einer Seite, entgegen dem Radius und der
Einfräsung mit feiner Schmiergelleinewand
auf Tuschierplatte abziehen und mit der
abgezogenen Seite zur Ventilscheibe zeigend
montieren (Bild 109).
Rundring (1) einsetzen. Aus Sicherheitsgründen
nur neue Ringe verwenden und auf einwandfreien
Sitz in der Nut achten (siehe Bild
109);
- Das Rundholz in das Führungsrohr von oben
einschieben und damit das Stützrohr bis
Anschlag nach unten hinausschieben, Rundholz
im Führungsrohr belassen;
Das Führungsrohr an seinem oberen Ende mit
dem Stützrohr nach oben zeigend in den
Schraubstock in weiche Schutzbacken einspannen.
Das noch im Führungsrohr befindliche Rundholz
stützt jetzt das Stützrohr nach unten ab;
Napf für Endanschlag (5), Druckfeder (4)
ø 19 mm und Dichtscheibe (3) auflegen
(Bild 107).
- Am Führungsrohr etwas Dämpfungsflüssigkeit
für den Wellendichtring anbringen und das
Gleitrohr von oben über das Führungsrohr
schieben und dabei das Gewindestück des
Stützrohres in die Bohrung im Gleitrohr
einfädeln. Wellscheibe (7) und Befestigungsmutter
(8), Bild 107, aufsetzen
und anziehen;
- Den Schutzbalg oder die Schutzkappe über
das Führungsrohr schieben und den Bund
(A) in die Rille (B) des Gleitrohres einsetzen.
Die Rille (B) im Gleitrohr vorher säubern.
Das Belüftungsloch im Schutzbalg muß nach
hinten zeigen. Den Schutzbalg oben mit
Klemmschelle befestigen.
- Die Druckfeder von oben in das Führungsrohr
einsetzen und die vorgeschriebene Menge
Dämpfungsflüssigkeit einfüllen;
|
Bild 113. Richtiger Sitz des Schutzbalges oder der Schutzkappe
Federn für Teleskopgabel
Bezeichnung | Maß- ein- heit | Solo | Gespann |
Länge | mm | 527 | 527 |
Außendurchmesser | mm | 26 | 26 |
Drahtdurchmesser | mm | 4,0 | 4,5 |
Windungen | An- zahl | 62,5 | 73,5 |
Federkonstante | N/mm | 4,06 | 5,9 |
5.3.7. Funktionsprüfung der Teleskopgabel
nächster Punkt ; Index
Nach der Montage sind die
Teleskopholme einer Funktionsprüfung auf
Dichtheit und Dämpfungskraft zu unterziehen.
Steht kein geeignetes Prüfgerät zur
Verfügung, so muß die Überprüfung
durch mehrmaliges kräftiges Ein- und
Ausfedern von Hand erfolgen. Die Dämpfung
muß beim Ausfedern deutlich spürbar sein.
Eine Probefahrt über eine schlechte
Wegstrecke ist auch als Funktionsprüfung
geeignet.
Der richtige Ölstand im eingebauten Zustand
der Teleskopgabel wird gemäß Bild
114 überprüft.
|
Bild 114. Ölstandskontrolle
Zur Ölstandskontrolle der Teleskopholme
sind die beiden am oberen Klemmkopf sitzenden
Verschlußstopfen zu entfernen und der Meßdraht
(ø 4 mm) ist in der Mitte der Druckfeder
einzuführen. Der Meßdraht muß bis zur tiefsten
Stelle der Teleskopholme gelangen, das heißt,
der Meßdraht muß noch durch das Stützrohr
geführt werden.
Bei jeder Ölstandskontrolle oder Neuauffüllung
kommt es auf gleiche Ölstände in den
Teleskopholmen an. Sonst werden die Fahreigenschaften
beeinträchtigt. Die angegebenen max. Ölstände
dürfen nicht überschritten werden, da sonst
beim Einfedern der Teleskopgabel der Druck zu
hoch ansteigt. Zur Ölqualität den Abschnitt
2.4. beachten.
Die Ölfüllmenge beträgt 230 cm³ je
Teleskopholm.
Ölstand (cm³) | Höhe des Ölspiegels (mm) |
230 (Solo) | = 330 |
230 (mit Seitenwagen) | = 340 |
Je nach Belastung des Fahrzeuges kann die Ölfüllmenge bis max. 265 cm³ bei der Solomaschine und auf max. 235 cm³ bei der Seitenwagenmaschine erhöht werden. |
265 (Solo) | = 395 |
235 (mit Seitenwagen) | = 345 |
5.4. Kraftstoffbehälter
nächster Punkt ; Index
Wegen der bestehenden
Explosionsgefahr dürfen Reparaturen am
Kraftstoffbehälter nur unter Beachtung
der einschlägigen Sicherheitsbestimmungen
ausgeführt werden.
Der Kraftstoffbehälter ist vorn und
hinten elastisch am Rahmen befestigt
(Bild 115).
Dadurch wird die Übertragung von Schwingungen
vom Rahmen auf den Kraftstoffbehälter wirksam
gedämpft. Nach dem Abnehmen des
Kraftstoffbehälters können die Gummiteile
einer Sichtprüfung unterzogen werden.
|
Bild 115. Befestigung des Kraftstoffbehälters
- Auflagestopfen, vorn
- Befestigungsschraube, hinten
- Befestigungselemente, hinten
- Haltegummi, vorn oben
Die elastische Lagerung des
Kraftstoffbehälters unterliegt keinem
wesentlichen Verschleiß. Sie darf nicht
in eine starre Lagerung umgewandelt
werden.
5.5. Kraftstoffhahn
nächster Punkt ; Index
Der Zustand des Kraftstoffhahns
hat auf die einwandfreie Motorfunktion wesentlichen
Einfluß. Ungenügender Kraftstoffzufluß kann auch
zu Kolbenklemmern führen.
|
Bild 116. Kraftstoffilterhahn, zerlegt
Der Kraftstoff durchfließt im Hahn zwei
Siebe. Das erst (1) ist nach dem Herausschrauben des
Kraftstoffhahnes aus dem Kraftstoffbehälter zugänglich;
das zweite (2) nach dem Lösen des Filtertopfes (3).
Es ist zu empfehlen, die Siebe nach jeweils 5000 km
Fahrstrecke oder einmal im Jahr gründlich zu reinigen.
Eine weitere Störquelle am Kraftstoffhahn kann die
Gummidichtung (4) unter dem Betätigungshebel (5) sein,
deren Bohrungen verstopft bzw. durch Quellen oder zu
straff angezogene Halteschrauben (6) verschlossen sein
können.
Betätigungshebel und Gummidichtung können nach dem
Lösen der beiden seitlich vom Betätigungshebel
angeordneten Halteschrauben ausgebaut werden.
Bei Instandsetzungsarbeiten am Kraftstoffhahn ist
auch der zum Vergaser führende Kraftstoffschlauch
mit zu überprüfen.
Ist dieser Schlauch spröde geworden, können an den
Anschlußstellen Undichtheiten auftreten. Der Einbau
eines neuen Kraftstoffschlauches der Abmessung 5x8,2 mm
ist dann erforderlich.
Achtung!
Auf keinen Fall dürfen Halteschrauben (6) bis zum
Anliegen des Federbleches (7) am Gehäuse (8)
festgezogen werden. Der Betätigungshebel (5) muß
leichtgängig sein. Wenn der Kraftstoffhahn einmal
tropfen sollte, dann die Halteschrauben (6)
gleichmäßig max. 1 Umdrehung anziehen.
Die Durchflußmenge muß mindestens 12 Liter pro
Stunde betragen.
5.6. Hinterradantrieb und Hinterradnabe
nächster Punkt ; Index
Der Aufbau des Hinterradantribes geht
aus den Bilder 117 und 118
hervor. Im Hinterradantrieb sind im Gegensatz zum
Vorgängertyp zwei Radialrillenlager eingebaut (siehe
Bild 118).
Die Kettenabdeckung enthält eine durchgehende Buchse
(1), die es erlaubt, die Mutter (2), siehe Bild
117, ohne Zerstörung der Abdeckung
mit dem möglichen Anzugsmoment anzuziehen.
|
Bild 117. Explosivdarstellung Hinterradantrieb
Die Hinterradnabe entspricht bis
auf geringfügige Formkorrekturen der Nabe des
Vorgängertyps.
|
Bild 118. Hinterradantrieb
- Dämpfungskörper
- Sicherungsring
- Lager 6204
- Kettenabdeckung
- Flanschbolzen
- Buchse
- Lager 6005
- Sprengring
- Dämpfungsgummi
5.6.1. Hinterradantrieb zerlegen
nächster Punkt ; Index
Dazu sind das Hinterrad und der
Hinterradantrieb auszubauen. Zunächst den
Flanschbolzen ausschlagen (siehe Bild
119).
Danach den Hinterradantrieb auf etwa 100 °C
anheizen. Das Lager 6005 (3) kann mit einem
Winkelschraubendreher ausgedrückt werden.
Den Sicherungsring 47 (4) herausnehmen und zum
Schluß das Lager 6204 (5) ausschlagen (Bild
117).
Den Zusammenbau nach dem nochmaligen Anwärmen
des Hinterradantriebes in umgekehrter
Reihenfolge ausführen.
|
Bild 119. Flanschbolzen ausschlagen
5.6.2. Tachometerantrieb
nächster Punkt ; Index
Der Tachometerantrieb ist auf
dem Bild 120 im Schnitt
dargestellt.
Das dazugehörige Schraubenrad ist mit einem
Hakensprengring auf dem Dämpfungskörper mit
Zahnkranz befestigt. Das Ritzel für Tachoantrieb
wird ausgewechselt, indem die Senkschraube (5)
aus der Kettenabdeckung herausgeschraubt und
die Lagerbuchse (6) mit dem Ritzel (3) und (7)
nach hinten herausgezogen wird.
Bei den Montagearbeiten sind das Ritzel, der
Ritzelschaft und das Schraubenrad mit
Wälzlagerfett einzusetzen.
|
Bild 120. Tachometerantrieb (Schnittzeichnung)
- Kettenabdeckung
- Dichtungsstück
- Ritzelkörper
- ohne Bedeutung
- Senkschraube BM 6x8
- Lagerbuchse
- Ritzel für Tachoantrieb
5.7. Radlager wechseln
nächster Punkt ; Index
Mit Hilfe eines Spreizdornes
(Sonderwerkzeug H 8-820-3)
wird der Ausbau der Radlager erleichtert. Der
Radkörper wird dazu leicht angewärmt. Nach dem
Einschlagen des Spreizdornes werden die Radlager
nach außen herausgeschlagen (Bild
121). Auch für den Einbau
der Radlager sind die Radkörper zu erwärmen.
Dabei darf auf keinen Fall die Distanzhülse
zwischen den Lagern vergessen werden. Außerdem
sind nur Kugellager 6302 mit Blechkäfig zu
verwenden.
Beim Wiedereinbau des kompletten Rades ist darauf
zu achten, daß der Gummidichtring neben dem
Radlager auf der Bremsseite nicht vergessen wird.
Dieser Dichtring soll verhindern, daß das
Schmiermittel der Radlager nach außen in die
Bremse geschleudert wird.
Die Radlager sind mit Wälzlagerfett
einzusetzen.
|
Bild 121. Herausschlagen der Radlager
Bild 122. Vorderradnabe (Schnittzeichnung)
- Radkörper mit eingegossenem Bremsring
- Bremsring
- Bremshebel
- Radkörperdeckel
- Rückholfeder für Bremsbacken
- Bremsgegenhalter
- Sechskantmutter M 14x1,5
- Scheibe
- Achse
- Achsaufnahme, rechts
- Abstandshülse
- Kugellager 6302
- Gummidichtring
- Ankerbolzen
- Sicherungsring 12
- Bremsbacken
- Achsaufnähme, links
- Sechskantschraube zum Klemmen der Achse
5.8. Bremsen
5.8.1. Innenbackenbremse
nächster Punkt ; Index
Die Ankerbolzen (1) haben
Festsitz im Bremsgegenhalter. Die Bremsbacken
(2) sind auf dem Ankerbolzen und der
Bremsschlüssel (3) im Bremsgegenhalter drehbar
gelagert (Bild 123).
An der Lagerung der Bremsbacken tritt
erfahrungsgemäß nur minimaler Verschleiß auf,
es ist jedoch erforderlich, daß die Lagerstellen
etwa alle 10000km, jedoch mindestens einmal im
Jahr gereinigt und neu mit Heißlagerfett
gefettet werden. Dasselbe gilt für die Lagerung
des Bremsschlüssels in der Bremsankerplatte.
Bei Ausbau der Bremsbacken sind diese zu
markieren, damit sie wieder so wie vorher
eingebaut werden können.
Bei Austausch der regenerierungsfähigen
Bremsbacken ist zu beachten, daß bereits
bearbeitete Bremsbacken einbaufähig sind.
Unbearbeitete Bremsbacken müssen jedoch noch
nachgedreht werden. Hierzu sind diese mit Hilfe
der Rückholfeder (4) auf dem Bremsgegenhalter zu
befestigen. Der Bremsgegenhalter ist in der
Bohrung zu zentrieren und die Backen sind in
einer
|
Bild 123. Bremsankerplatte, komplett
- Massekontakt für Stopplicht (auch für Vorderradbremse)
Drehmaschine so weit abzudrehen,
daß die Differenz zwischen dem Durchmesser des
Bremsringes und dem Durchmesser der Bremsbacken
mindestens 0,6 mm beträgt.
5.8.2. Scheibenbremse für das Vorderrad
nächster Punkt ; Index
Die Festsattelbremse wird über
einen Hebel am Hauptbremszylinder hydraulisch
betätigt. Die Anordnung der Bauteile ist aus
Bild 124 ersichtlich.
|
Bild 124. Scheibenbremsenanordnung
- Hauptbremszylinder
- Bremsschlauch
- Bremssattel
- Bremsscheibe
Die Bilder 125
und 126 zeigen explosiv die
Zusammengehörigkeit der Teile von Bremssattel
und Hauptbremszylinder.
Demontage und Montage des Hauptbremszylinders
- Kabelanschlüsse am Bremslichtschalter lösen
- Bremsschlauch etwa 0,25 Umdrehungen lockern
- Hauptbremszylinder vom Lenker abschrauben
- Verschlußkappe und Hermetikbalg abnehmen und
Bremsflüssigkeit auskippen
- Bremsschlauch vollständig abschrauben.
Bei der Montage zunächst die
Verschraubung des Bremsschlauches (Überwurfmutter)
lockern, damit sich beim Einschrauben der Bremsschlauch
nicht verdreht. Alle Verschraubungen anziehen,
Bremsflüssigkeit auffüllen und Bremse entlüften.
Reparatur des Hauptbremszylinders
Den Handbremshebel abnehmen. Danach mit Druckluft, die
über die Schlauchanschlußbohrung wirken muß, die
Innenteile des Hauptbremszylinders auspressen. Dabei
mit einer Hand verhindern, daß die Teile
davonspringen.
Riefen in den Gleitbahnen von Zylinder und Kolben
bedingen den Austausch des kompletten Hauptbremszylinders.
Sind nur die Dichtringe defekt, kann der Hauptbremszylinder
unter Verwendung eines Satzes neuer Dichtringe wieder
zusammengebaut werden. Peinlichste Sauberkeit ist
Voraussetzung. Alle Gleitflächen und Dichtungen
mit Bremsflüssigkeit benetzen und gemäß Bild
125 die Teile demontieren. Den
Haltering des Abschlußdichtringes mit einer Hülse
(Rohrdurchmesser = 18 mm x 16 mm x 30 mm) bis
zum richtigen Einrasten in seine Nut schieben.
Den Handbremshebel so befestigen, daß er leicht
aber spielfrei in seiner Halterung bewegt werden
kann. Das Spiel zwischen Kolben und Handbremshebel
mit der Stellschraube auf etwa 0,5 mm einstellen.
|
Bild 125. Hauptbremszylinder
- Verschlußdeckel
- Entlüftungsring
- Hermetikbalg
- Gehäuse
- Befestigungsschelle
- Feder
- Bremskolben
- Dichtmanschetten
- Scheibe
- Dichtung
- Sprengring
Demontage und Montage des Bremssattels
- Bremsschlauch durch das Lösen der Überwurfmutter
demontieren. Den Schlauch mit Bindedraht an der
Teleskopgabel befestigen.
Beachten: Die Schlauchöffnung darf nicht tiefer
als der Flüssigkeitsspiegel im Vorratsbehälter
des Handbremszylinders sein!
- Bremssattel vom Gleitrohr der Teleskopgabel
demontieren.
Montage in umgekehrter Reihenfolge.
Bei Bedarf Bremsflüssigkeit auffüllen, Bremse
entlüften.
Reparatur des Bremssattels
- Abdeckung abnehmen
- Beide Bolzen mit Dorn von der Seite des kleinen
Bolzendurchmessers herausschlagen
- Bremsbacken herausnehmen
- Bremssattel zerlegen
- Bremskolben mit Druckluft ausdrücken
Für die Aussonderung von Teilen
gelten die gleichen Kriterien wie beim Hauptbremszylinder.
Die Montage der peinlichst sauberen Einzelteile in
umgekehrter Reihenfolge vornehmen. Die Gleitflächen
und inneren Dichtringe vor dem Zusammenbau mit
Bremsflüssigkeit befeuchten.
|
Bild 126. Bremssattel der Scheibenbremse
- Innerer Bremszylinder
- Dichtring
- Bremskolben
- Dichtmanschette
- Bremsbacken
- Äußerer Bremszylinder
- Führungsbolzen
- Innensechskantschraube
- Dichtung
- Abdeckkappe
- Kegelstift
- Feder
- Entlüftungsschraube
- Schutzkappe
Bremsbacken auswechseln
Die Bremsbacken in nachstehender Reihenfolge wechseln, wenn
sie bis auf die Verschleißmarkierung abgearbeitet sind.
- Vorderrad ausbauen
- Bremsbacken wie im Abschnitt "Reparatur
des Bremssattels" ausbauen
- Bremssattel äußerlich reinigen
- Bremskolben zurückdrücken
- Neue Bremsbacken montieren
- Vorderrad einbauen
Beachten: Bei ausgebauten Bremsbacken Bremse nicht
betätigen!
|
Bild 127. Bremsbacken-Verschleißmarkierung
V = Verschleißnut
Bremsscheibe auswechseln
Die Bremsscheibe ist zu wechseln,
wenn sie auf weniger als 4,4 mm abgearbeitet ist
oder Riefen aufweist, die im Riefengrund ebenfalls
diese minimale Dicke unterschreiten.
Beachte: Aus Sicherheitsgründen bei jeder
Montage der Bremsscheibe neue selbstsichernde Muttern
verwenden!
Vor dem Einbau des mit neuer Bremsscheibe versehenen
Rades die Bremskolben im Bremssattel zurückdrücken.
Bremsflüssigkeit erneuern
Nach etwa zwei Jahren die Bremsflüssigkeit erneuern.
Das kann mit einem Füllgerät oder wie nachstehend
beschrieben erfolgen.
- Geeigneten Schlauch auf Entlüftungsventil
des Bremssattels stecken
- Entlüftungsventil öffnen. Durch fortlaufendes
Pumpen am Handbremshebel die Bremsanlage über
den Schlauch in einen geeigneten Behälter
entleeren.
- Bremsflüssigkeit auffüllen
- Bremsanlage entlüften.
Bremsflüssigkeit auffüllen
Wenn die Bremsanlage neu eingebaut wird, repariert
wurde oder die Bremsflüssigkeit erneuert werden
muß, kann das Auffüllen von Bremsflüssigkeit
entweder mit einem Füllgerät oder wie nachstehend
beschrieben erfolgen.
- Verschlußdeckel und Hermetikbalg vom
Hauptbremszylinder abnehmen
- Schlauch (1m lang) mit Trichter versehen und
auf Entlüftungsventil stecken
- Entlüftungsventil öffnen
- Schlauch anheben, so daß sich der Trichter etwa
20 cm über Oberkante Vorratsbehälter befindet und
Bremsflüssigkeit auffüllen, bis maximale
Füllstandshöhe im Vorratsbehälter erreicht
ist
- Entlüftungsventil schließen
- Hermetikbalg einlegen und Verschlußdeckel
aufschrauben
- Bremse entlüften.
Bremse entlüften
Die Bremse entlüftet sich selbst. Das dauert
bei geöffnetem Vorratsbehälter etwa eine Stunde.
Letzte Luftreste entweichen beim leichten Abklopfen
von Bremssattel und Bremsschlauch. Danach
Hermetikbalg einlegen und Verschlußdeckel
aufschrauben.
Schneller entlüften kann man wie folgt:
- Vorratsbehälter verschließen.
- Füllschlauch auf Entlüftungsventil stecken
und bis etwa zur Hälfte des Trichters füllen.
- Schlauch hochhalten (Trichter etwa 20 cm
über obere Füllstandsmarkierung des
Hauptbremszylinders).
- Entlüftungsventil 1/2 Umdrehung öffnen
und gleichzeitig Handbremshebel bis zum Anschlag
ziehen. Ventil bei gezogenem Handbremshebel
schließen.
- Vorgang wiederholen, bis keine Luftblasen mehr
auftauchen. Der Flüssigkeitsspiegel darf dabei
nicht unter die untere Füllstandsmarkierung
absinken.
- Abschließend den Hauptbremszylinder bis zur
oberen Markierung auffüllen, Hermetikbalg
einlegen und Deckel verschrauben.
Störungen der Bremsanlage
Störung | mögliche Ursache | Abhilfe |
Bremswirkung ungenügend | Bremsscheibe verschmutzt | Intervallbremsung bis zum Abtrocknen der Bremsscheibe |
Bremsbelag verölt | Bremsbacken wechseln |
Kolben im Bremssattel fest | Kolben gangbar machen bzw. Bremssattel austauschen, Bremsflüssigkeit wechseln |
Kein Gegendruck am Handbremshebel | Luft im Bremssystem | Bremssystem entlüften |
Bremsleitungen bzw. Bremszylinder undicht | Bremsleitungen, Bremszylinder abdichten oder austauschen |
Bremsflüssigkeitsmenge zu gering | Bremsflüssigkeit ergänzen |
Ausgleichbohrung im Vorratsbehälter verdeckt - Bremsflüssigkeit kann nicht nachlaufen | Spiel am Handbremshebel einstellen |
Bremse hält nicht | Bremsscheibe verschlissen | Bremsscheibe wechseln |
Unterdruck im Vorratsbehälter | Verschlußdeckel öffnen, Belüftungsbohrung säubern |
Bremshebel bewegt sich beim Bremsen | Bremsscheibe hat Dickendifferenz | Bremsscheibe wechseln |
Bremsflüssigkeitsstand sinkt ab | Bremsleitungen bzw. Bremszylinder undicht | Bremsleitungen abdichten, Dichtungen in den Zylindern erneuern bzw. Hauptbremszylinder und Bremssattel wechseln |
Bremsbacken verschlissen | Bremsbacken austauschen |
Bremsschlauch porös oder defekt | Bremsschlauch wechseln |
Nachlassender Druckpunkt am Handhebel bei stark erwärmter Bremse | Bremsflüssigkeit enthält Wasser - Dampfblasenbildung | Bremsflüssigkeit wechseln |
Bremsflüssigkeit enthält Wasser | Wechselintervall nicht eingehalten | Wartungsplan beachten |
Hermetikbalg nicht eingelegt oder defekt | Hermetikbalg einlegen oder erneuern Bremsflüssigkeit wechseln |
Stoplicht geht nicht beim Betätigen der Vorderradbremse | Kabel abgerissen, Steckverbinder oxydiert, Stoplichtschalter defekt | Verbindungen in Ordnung bringen, Stoplichtschalter wechseln |
5.9. Sekundärkette
nächster Punkt ; Index
Das Auflegen einer neuen Kette ist auf
den Bildern 128...130
dargestellt.
|
Bild 128. Auflegen einer Kette - 1. Etappe
Beide Kettenschutzschläuche werden zunächst
auf das Motorgehäuse aufgeschoben. Die Kette wird beim
Auflegen auf den hinteren Zahnkranz von oben nach unten
durchgezogen. Das obere Ende wird mit Hilfe einer
durchgesteckten Speiche fixiert. Danach wird mit Hilfe
eines Drahthakens die Kette von hinten nach vorne durch
den unteren Kettenschutzschlauch gezogen und um das
vordere Kettenrad gelegt.
Zuletzt wird die Kette - wiederum mit einem Drahthaken -
von vorn nach hinten durch den oberen Kettenschutzschlauch
gezogen und hinten oben durch das Kettenschloß verbunden.
|
Bild 129. Auflegen einer Kette - 2. Etappe
Bild 130. Auflegen einer Kette - 3. Etappe
Der obere Kettenschlauch ist dabei
etwas nach vorn zu schieben und durch eine Speiche
zu halten (Bild 130). Zu
beachten ist die richtige Lage der Verschlußfeder:
Öffnung nach hinten!
Beim Auswechseln einer Kette ist die neue Kette an
die alte anzuhängen und durchzuziehen. Ein Auswechseln
der Kette ist erforderliech, wenn mehr als 5 Rollen
oder mehr als 2 Rollen nebeneinander gebrochen bzw.
wenn die Kettenbolzen in den Kettenlaschen ausgeschlagen
sind.
Wird eine Kette eines anderen Fabrikats aufgelegt,
müssen unbedingt die dazugehörenden Kettenschlösser
verwendet werden, weil die Bolzendurchmesser
verschieden sein können.
|
Bild 131. Kettenspannung überprüfen
Beim Erneuern einer Kette sind auch
die Kettenräder mit zu überprüfen.
Bei Verschleiß derselben ist es erforderlich
diese ebenfalls zu erneuern.
Wesentlichen Einfluß auf die Lebensdauer der Kette
haben richtige Kettenspannung und Kettenschmierung.
Eine Richtige Kettenspannung ist gewährleistet,
wenn sich der obere Kettenschutzschlauch
einschließlich Kette mit zwei Fingern ohne
Anwendung von Gewalt auf das Querrohr der
Hinterradschwinge niederdrücken läßt.
Prüfung eines vollen Kettenumlaufes!
Dabei muß das Hinterrad voll ausgefedert sein
(Motorrad auf dem Kippständer stehend). Wem
die Kette dabei zu locker erscheint, möge
bedenken, daß beim Einfedern des Hinterrades die
Kette straffer wird!
Das Nachschmieren der Kette ist etwas alle
2500 km erforderlich.
Bei abgenommenem Lichtmaschinendeckel wird
mit Hilfe eines Schraubendrehers das
Wälzlagerfett Ceritol +k2 oder +k3 auf den
unteren Kettenzug aufgebracht und dabei das
Hinterrad in Fahrtrichtung langsam einen vollen
Kettenumlauf durchgedreht, danach die gleiche
Menge Fett auf den oberen Kettenzug auftragen
und das Hinterrad entgegen der Drehrichtung
durchdrehen.
5.10. Auspuffanlage
nächster Punkt ; Index
Die Auspuffanlage ist so auf den
Motor abgestimmt, daß erstens die erforderlichen
Leistungskennlinie erreicht und zweitens die
zulässige Geräuschgrenze eingehalten wird. An
der Auspuffanlage dürfen deshalb keinerlei
Veränderungen vorgenommen werden.
|
Bild 132. Schnittzeichnung des Auspufftopfes
- Auspuffmantel
- Schweißnaht
- Dämpfungseinsatz
- Auspuffendstück
Der Auspufftopf (Bild 132)
ist verschweißt und nicht demontierbar.
Die Befestigung des Auspuffrohres am Zylinder
erfolgt durch eine Überwurfmutter, die den
konischen Bördelrand gegen den Zylinder drückt
(ohne Dichtung).
Die Überwurfmutter wird im Neuzustand mit einem
Anzugsmoment von 150+30
Nm (15+3 kpm)
angezogen. Sie ist unbedingt nach einer
Fahrstrecke von rund 500 km mit dem gleichen
Anzugsmoment nochmals nachzuziehen, weil sich
während dieser Fahrstrecke der Konus des
Auspuffrohres an die Anlagefläche des
Zylinders und an die Druckstelle der
Überwurfmutter erst richtig anlegt.
Das Nachziehen erfolgt mit einem Hakenschlüssel
B 39-442 und aufgestecktem Verlängerungsrohr.
Wesentlich für die einwandfreie Auspuffbefestigung
ist, daß alle drei Aufhängestellen (Zylinder,
untere Verbindung, hintere Strebe) ordentlich
fest sitzen. Ist eine dieser Stellen schadhaft,
werden die beiden restlichen zu sehr beansprucht
und locker.
Die Gummilagerungen der Strebe dürfen wegen der
elastischen Motoraufhängung keinesfalls durch
eine starre Verbindung ersetzt werden.
5.11. Räder spuren, Vorderrad auswuchten
nächster Punkt ; Index
Eine richtig eingestellte Spur ist die
Voraussetzung für gutes Fahrverhalten.
Da der vordere Reifen nicht so breit ist wie der
hintere, ist das Vorderrad dabei parallel zur
Meßlatte zu stellen.
|
Bild 133. Räder spuren
1. Spurlatte
S. Spalt zwischen Meßlatte und Vorderrad
Das Vorderrad wird zur Verbesserung
der Fahreigenschaften serienmäßig ausgewuchtet. Bei
Reifenschaden muß der Reifen wieder in der gleichen
Lage zur Felge montiert werden, d.h. roter Punkt
am Ventil.
Die Unwucht kann sich durch ungleichmäßigen
Verschleiß nach längerer Laufzeit verändern,
deshalb ist nach etwa 10000 km neu auszuwuchten.
Bei Montage eines neuen Reifens muß ebenfalls
neu ausgewuchtet werden.
Das Auswuchten erfolgt durch Auspendeln des
Rades mit fettfreien Lagern auf der Radachse
und Anbringen von Gegengewichten (entweder
MZ-Auswuchtkörper bzw. ersatzweise Blei- oder
Kupferdraht) an den Speichennippeln an der Stelle
des Rades, die beim Auspendeln oben bleibt.
5.12. Seilzüge
nächster Punkt ; Index
Die Seilzüge sind am Motorrad äußeren
Einflüssen wie Regen, Schmutz und Lauge, besonders stark
ausgesetzt. Bei Motorrädern, die täglich gefahren und
darüber hinaus oft im Freien abgestellt werden, tritt
innerhalb der Seilzüge starke Reibung auf, und die
Betätigungshebel lassen sich nur noch schwer ziehen.
Leichtgängigkeit und Lebensdauer der Seilzüge werden
verbessert, indem die Seilzüge an den Betätigungshebeln
gegen Eindringen von Wasser und Schmutz abgedichtet und
durchgeschmiert werden.
Die einfachste Form der Abdichtung ist das Bestreichen
des herausragenden Seilendes und des Schlitzes in der
Verstellschraube des Betätigungshebels mit einem
wasserabweisenden Fett, am besten mit Ceritol.
Durch Anbau eines Gummischutzbalges, Teil-Nr. 05-44.050,
ist eine weitere zusätzliche Möglichkeit gegeben, die
Lebensdauer der Seilzüge zu verlängern. Der Innenraum
des Schutzbalges ist mit einem wasserabweisenden Fett
zu füllen.
Die Seilzüge werden mit der im Bild 134
dargestellten Vorrichtung durchgeschmiert.
|
Bild 134. Vorrichtung zum Abschmieren von Seilzügen
Als Schmiermittel wird entweder
ein Gemisch aus Getriebeöl und Getriebefett im
Mischungsverhältnis 1:3 oder ein Gemisch von
Wälzlagerfett Ceritol +k3 und Kraftstoff,
Mischungsverhältnis 1:1, verwendet.
Die Seilzüge werden an einem Ende der Umhüllung
in die keglige Gummikappe eingeklemmt und
zusammen mit der Gummikappe mit Hilfe der
Überwurfmutter auf die Vorrichtung
geschraubt.
|
Bild 134a. Seilzug in Schmiervorrichtung eingespannt
6. Elektrische Anlage
6.1. Drehstromlichtmaschine (DLM)
6.1.1. Arbeitsweise
nächster Punkt ; Index
Der immer dichter werdende Verkehr
und der Trend zur Erhöhung der Verkehrssicherheit
durch Einsatz von Halogenlicht, zusätzlichen Anbau
von Nebelschlußleuchten und Nebelscheinwerfern
auch an Krafträdern führt zur Erhöhung des
Bedarfs an elektrischer Energie.
Diesem Leistungsanstieg kann die Gleichstromlichtmaschine
bei vertretbarem Aufwand und infolge höherer
Motordrehzahlen nicht mehr folgen.
Demgegenüber sind Drehstromlichtmaschinen bei
gleicher Masse in der Lage, eine weitaus höhere
Leistung zu erzeugen.
Drehstromlichtmaschinen besitzen keinen Kollektor,
der Ausgangsstrom wird kontaktlos von der Statorwicklung
entnommen. Nur ein geringer, über 3 Erregerdioden
abgezweigter Erregerstrom wird über 2 Kohlebürsten
und Schleifringe an den Rotor übertragen, so daß
ein Betrieb bei hohen Drehzahlen möglich ist.
Der vom Stator entnommene Wechselstrom wird von einem
leistungsfähigen Drehstrombrückengleichrichter
in Gleichstrom umgewandelt.
Dieser gewährleistet durch den Einsatz moderner
Siliziumhalbleiter wartungslosen Betrieb und eine
lange Lebensdauer.
Der Brückengleichrichter stellt einen separaten
Baustein dar, auf dem auch das Erregerdiodentrio montiert
ist.
Die abgegebene Spannung wird mittels eines
elektromechanischen Einelementreglers auf der
erforderlichen Höhe gehalten. Gleichzeitig wird der
Maximalstrom durch den Regler begrenzt.
Bei Einhaltung der in den technischen Unterlagen
geforderten Reglerspannung und Einbaubedingungen
ist ein Schutz der DLM vor Zerstörung und eine
hohe Lebensdauer der elektrischen Anlage
gewährleistet.
6.1.2. Technische Daten
nächster Punkt ; Index
Kenn-Nr. | 8046.2 |
Lichtmaschinenspannung | 14 V |
Leerlaufdrehzahl | = 1300 U/min |
Drehzahl bei 2/3 des Maximalstromes | = 2200 U/min |
Maximaldrehzahl | 10000 U/min |
2/3 des Maximalstromes | 10 A |
Maximalstrom | 15 A |
Widerstand der Rotorwicklung | 4,2 ±0,3 Ohm |
Kohlebürstenlänge | 16 mm |
Kohlebürstenlänge (Mindestmaß) | 9 mm |
Kohlebürsten-Federkraft | 1,4...3,2 N (0,14...0,32 kp) |
Schleifringe (Mindestdurchmesser) | 31 mm |
Rundlaufabweichung | 0,05 mm |
Anzugsdrehmoment der Rotorbefestigungsschraube | 20±2 Nm (2±0,2 kpm) |
Drehrichtung (auf Schleifringkörper gesehen) | im Uhrzeigersinn |
Polarität | Masse negativ |
6.1.3. Technische Charakteristik
nächster Punkt ; Index
Die Drehstromlichtmaschine ist ein
3phasiger, 8poliger Synchrongenerator in
Sternschaltung.
Der die Erregerwicklung und die Schleifringe tragende
Rotor ist auf dem Kegelstumpf der Kurbelwelle des
Antriebsmotors befestigt. Der die Drehstromwicklung
aufnehmende Stator wird im Motorgehäuse lageorientiert
zentriert und gemeinsam mit einer die Zündeinrichtung
und den Kohlebürstenhalter tragenden Alu-Druckgußkappe
durch 3 über den Außendurchmesser des Stators
geführte Schraube befestigt.
Der Drehstrom wird in einem Gleichrichter in
3-Phasen-Brückenschaltung gleichgerichtet.
Der Erregerstrom zur Erzeugung des Magnetfeldes wird
von der Statorwicklung abgezweigt und durch 3
zusätzliche Erregerdioden und die 3
Minus-Leistungsdioden gleichgerichtet.
Der Erregerstrom wird von der Klemme 61 über den
Regler, die Kohlebürsten und die Schleifringe der
Erregerwicklung zugeführt. Der Regler hält die
Lichtmaschinenspannung konstant und begrenzt den
Maximalstrom.
Die Drehstromlichtmaschine weist gute
Selbsterregungseigenschaften auf. Ein Betrieb ohne
Batterie ist möglich.
Zündeinrichtung:
Kontaktunterbrecher mit Zündkondensator. Mit
zugehörigem Nocken je Kurbelwellenumdrehung ein
Zündimpuls.
|
Bild 135. Drehstromlichtmaschine 12 V, 15 A
Bild 136. Gleichrichter für DLM 12 V, 15 A
- 6xFlachsteckanschluß 6,3 TGL 22425
- Diodenplatte (minus)
- Diodenplatte (plus)
- Isolierplatte mit Erregerdioden
Bild 137. Schaltung von Lichtmaschine, Gleichrichter und Regler
- Drehstromlichtmaschine
- Stator
- Rotor
- Zündkondensator
- Unterbrecher
- Gleichrichter
- Plusdioden
- Minusdioden
- Erregerdioden
- Kontrolleuchte
- Zündschalter
- zu den Verbrauchern
- zur Zündspule
- Regler
- Batterie
- Kondensator 2,5 uF, 50 V
6.1.4. Fehlerdiagnosen
nächster Punkt ; Index
Im folgenden werden Arbeitsabläufe
beschrieben, die dazu dienen, Defekte an der
Stromversorgungsanlage in kürzester Frist
festzustellen.
Je nach Anwendungsfall ist die entsprechende
Methode auszuwählen.
Fehler in der Stromversorgungsanlage zeigen
sich im allgemeinen durch das Auftreten einer
der nachfolgenden Abweichungen:
- Abnormales Verhalten der Ladekontrolleuchte;
- Ungenügend aufgeladene Batterie. Ersichtlich am
Nichtanspringen des funktionsfähigen Motors
und an der niedrigen Dichte der Batteriesäure.
- Zu stark aufgeladene Batterie. Ersichtlich am
hohen Wasserverbrauch und überkochender
Batteriesäure.
- Geräuschbildung durch mechanischen Verschleiß
der Kohlebürsten und Schleifringe oder
Schleifen des Rotors am Statorpaket.
6.1.5. Verhalten der Ladekontrolleuchte
nächster Punkt ; Index
Arbeitsweise der elektrischen Anlage:
Vorschriftsmäßig |
Zünd- schal- ter | Lade- kontroll- leuchte | Motor | Siehe Abschnitt 6.1.7.2. |
Aus | Aus | abgestellt | |
Ein | Ein | abgestellt | |
Ein | Aus | läuft | |
Fehlerhaft |
Aus | Ein | abgestellt | Teil I |
Ein | Aus | abgestellt | Teil II |
Ein | geringe Helligkeit | abgestellt | Teil III |
Ein | Ein | läuft | Teil IV |
6.1.6. Meßgeräte
nächster Punkt ; Index
Meßgerät | Verwendungszweck |
Autolicht-Prüf-Fix 12 V (Prüflampe mit Spannungsquelle) | Leitungsprüfung, Diodenprüfung |
Vielfachmesser | Spannungsmessung, Diodenprüfung |
Widerstandsmeßbrücke nach Thomson | Widerstandsmessung am Stator |
Widerstandsmeßbrücke nach Wheatstone | Widerstandsmessung am Rotor |
Oszillograph | Beurteilung der Kurvenform der Spannung der Drehstromlichtmaschine entsprechend Abschnitt 6.1.7.1. |
6.1.7. Messungen am Fahrzeug
nächster Punkt ; Index
Auch im eingebauten Zustand
der elektrischen Geräte lassen sich schon
die meisten Fehler erkennen.
Die schnellste und exakteste Aussage läßt
sich mittels eines Oszillographen machen.
Praktisch alle vorkommenden Fehler an der DLM
und am Gleichrichter lassen sich in der
aufgezeichneten Kurvenform erkennen.
Der Motor muß bei der Messung mit mindestens
3000 U/min betrieben werden.
Sollte kein Oszillograph zur Verfügung stehen,
so ist mit einem Vielfachmesser (z.B. UNI 7)
nach Abschnitt 6.1.7.2. zu
verfahren.
6.1.7.1. Verwendung eines Oszillographen
nächster Punkt ; Index
Der Oszillograph ist an die Klemmen
D+ und Masse anzuschließen. Alle Verbraucher,
außer der Zündung sind abzuschalten. Die
Batterie bleibt angeklemmt.
Achtung: Bei Verwendung eines Oszillographen
ohne Gleichspannungsverstärker erscheinen die
Kurven auf der Nullinie des Oszillographen (siehe
Bild 138)!
Alle von den Bildern 138 bzw.
139 abweichenden Kurvenformen
weisen auf Fehler hin.
|
Bild 138. Normales Arbeiten der DLM - Oszilloskop ohne Gleichspannungsverstärker
Bild 139. Normales Arbeiten der DLM
Bild 140. Kurzschluß Plusdiode
Bild 141. Kurzschluß Minusdiode
Bild 142. Unterbrechung Plusdiode
Bild 143. Unterbrechung Minusdiode
Bild 144. Kurzschluß Erregerdiode
Bild 145. Unterbrechung Erregerdiode
Bild 146. Kurzschluß Statorwicklung
Bild 147. Kurzschluß Rotorwicklung
Bild 148. Masseschluß Statorwicklung
Bild 149. Unterbrechung Statorwicklung
Bild 150. Unterbrechung Rotorwicklung
6.1.7.2. Fehlersuche
nächster Punkt ; Index
Störung | mögliche Ursache | Abhilfe |
Teil I |
Ladekontrolleuchte leuchtet - Zündschalter ausgeschaltet - Motor abgestellt | Zündschalter defekt | Zündschalter auswechseln |
Kabel zur Kontrolleuchte hat Kurzschluß mit Pluspotential | Kurzschluß beseitigen |
Teil II |
Ladekontrolleuchte leuchtet nicht - Zündschalter eingeschaltet - Motor abgestellt | Ladekontrolleuchte defekt | Glühlampe oder Leuchte auswechseln |
Kabel 61 zum Regler unterbrochen | Kabel erneuern |
Masse des Reglers u. Kabel DF unterbrochen | Kabel erneuern |
Gleichrichter defekt (Überprüfung nach Abschnitt 6.1.10.1. durchführen) | Gleichrichter auswechseln |
Teil III |
Ladekontrolleuchte leuchtet mit geringer Helligkeit - Zündschalter eingeschaltet - Motor abgestellt | Korrosion in der Fassung der Ladekontrolleuchte | Fassung reinigen oder auswechseln |
Kabel DF vom Regler zur DLM unterbrochen | Kabel erneuern |
Rotor defekt (Überprüfung nach Abschnitt 6.1.10.3. durchführen) | Rotor auswechseln |
Teil IV (Verbraucher abschalten) |
Ladekontrolleuchte leuchtet - Zündschalter eingeschaltet - Motor läuft | Beschädigte Kabel und Verbindungen zwischen 61 Regler und 61 Gleichrichter, D+ Regler und D+ Gleichrichter, 51 Regler und Batterie | Beschädigte Teile instandsetzen oder erneuern |
Die zwischen D+ Regler und Masse gemessene Spannung ist größer als die zwischen 51 Regler und Masse (U>0,2 V) | Regler auswechseln |
Reglerkontakte zwischen DF und 61 des Reglers voneinander isoliert Überprüfung bei abgeklemmter Batterie und abgezogenen Steckverbindungen zwischen DF und 61 am Regler mit Hilfe einer Widerstandsmeßbrücke durchführen (R>0,5Ohm) | Regler auswechseln |
Gleichrichter defekt (Überprüfung nach Abschnitt 6.1.10.1. durchführen) | Gleichrichter auswechseln |
Kabel DF zwischen Regler und DLM unterbrochen | Kabel oder die entsprechenden Anschlüsse erneuern |
Beschädigte Kohlebürsten oder Kohlebürstenanschlüsse | Beschädigte Teile auswechseln |
Rotor defekt (Überprüfung nach Abschnitt 6.1.10.3. durchführen) | Rotor auswechseln |
Kabel U/V/W zwischen Stator und Gleichrichter und/oder Masseverbindung beschädigt | Beschädigte Teile erneuern |
Eisenschluß des Stators (Überprüfung nach Abschnitt 6.1.10.2. durchführen) | Stator auswechseln |
Windungsschluß des Stators (Überprüfung nach Abschnitt 6.1.10.2. durchführen | Stator auswechseln |
6.1.8. Ausbau aus dem Fahrzeug
6.1.8.1. Ausbau der Drehstromlichtmaschine
nächster Punkt ; Index
Achtung:
Vor dem Ausbau ist die Batterie vom Bordnetz zu
trennen!
Alle Steckverbindungen (U, V, W, DF, 61, D-) sind
von der DLM zu entfernen.
|
Bild 151. Kabel von der DLM abziehen
Kohlebürstenhalter durch Lösen
der beiden Befestigungsschrauben entfernen.
|
Bild 152. Kohlebürstenhalter abgebaut
Stator mit Haltekappe nach dem
Lösen der 3 Befestigungsschrauben entfernen.
|
Bild 153. Haltekappe abnehmen
Rotorschraube zusammen mit dem
Nocken entfernen. Rotor mit Hilfe der AbziehVorrichtung
(Abziehschraube M 10x 45 TGL 0-933-8.8) von der
Kurbelwelle trennen.
Bei der Demontage ist größte Vorsicht geboten, da
die Schleifringe sehr leicht beschädigt werden
können. Die ausgebauten Teile müssen vor Schmutz,
Feuchtigkeit und mechanischer Beschädigung geschützt
werden.
|
Bild 154. Rotor abziehen
Bild 155. Innere Elektrik
- Regler
- Kondensator 2,5 uF, 50 V
- Zündspule
- Leitungsverbinder
- Gleichrichter
- Befestigungsschrauben
Achtung:
Vor dem Ausbau ist die Batterie vom Bordnetz zu
trennen!
Steckverbindungen U/V/W, 61, D+ und D-
entfernen. Für die spätere Montage ist es zweckmäßig,
die Kabel D+ und D- und 61 besonders zu kennzeichnen,
da ein Vertauschen dieser Anschlüsse zur Zerstörung
der Dioden des Gleichrichters führt.
Die Anschlüsse U/V/W zwischen DLM und Gleichrichter
können untereinander vertauscht werden, ohne daß
Folgeschäden auftreten.
Der Ausbau erfolgt durch Lösen der Befestigungsschrauben
(6).
6.1.9. Demontage der Drehstromlichtmaschine
6.1.9.1. Stator mit Haltekappe
nächster Punkt ; Index
Kohlebürstenhalter (9, Bild 156)
Steckanschlüsse der Kohlebürsten lösen.
Befestigungsschrauben entfernen.
Abziehen der Halteklammer (10, Bild 156).
Dabei sind die Kohlebürsten (8, Bild 156)
vor dem Herausspringen zu halten.
Kohlebürsten und Druckfedern auf Verschleiß
kontrollieren.
Stator (6, Bild 156)
Ablöten der Statorwicklung U/V/W.
Lösen der Haltewinkel (5, Bild 156).
Damit ist der Stator als komplette Baueinheit von
der Haltekappe (7, Bild 156)
entfernbar.
Rotor (4, Bild 156)
Der Rotor ist nicht für Reparatur vorgesehen. Ein
Austausch des Schleifringkörpers hat in speziellen
Regenerierungswerkstätten zu erfolgen.
|
Bild 156. Explosivdarstellung der Drehstromlichtmaschine
- Isolierplatte mit Erregerdioden
- Diodenplatte - Plus
- Diodenplatte - Minus
- Rotor
- Haltewinkel
- Stator
- Haltekappe
- Kohlebürsten
- Kohlebürstenhalter
- Halteklammer
6.1.9.2. Gleichrichter
nächster Punkt ; Index
Lösen der vier M4-Befestigungsschrauben
und Ablöten der Gleichrichterlitzen an den Steckfahnen
U/V/W.
Die drei Baueinheiten sind getrennt prüfbar und
reparaturfähig (siehe Abschnitt
6.1.10.3.).
Zum Ausdrücken defekter Plus- oder Minus-Dioden ist
ein Ausdrückdorn (Bild <157) zu
verwenden.
|
Bild 157. Ausdrückdorn
Rundstahl 22 TGL 11163 St 50 K TGL 0-1652
Zum Eindrücken neuer Gleichrichter
muß ein Einpreßstempel (Bild 158)
verwendet werden.
|
Bild 158. Eindrückdorn
Rundstahl 22 TGL 11163 St 50 K TGL 0-1652
Dabei ist eine maximale Einpreßkraft
von 4000 N (400 kp) zulässig. Es ist darauf zu achten,
daß der Stempel exakt auf dem Diodenrand aufliegt.
Für das Arbeiten mit Halbleiterdioden gelten die
Angaben des Herstellers.
6.1.10. Bauteilprüfung
6.1.10.1. Gleichrichter überprüfen
nächster Punkt ; Index
Die Überprüfung der Gleichrichterdioden
erfolgt zweckmäßigerweise mit einem Durchgangsprüfer.
|
Bild 159. Prinzip der Diodenprüfung
Die Meßspitzen werden jeweils an den
Anoden- und Kathodenanschluß der Diode angelegt.
Legt man plus der Meßspitzen an die Anode und leuchtet
die Prüflampe auf, so ist die Diode funktionsfähig.
Leuchtet die Lampe nicht auf oder leuchtet die
Prüflampe, wenn der Pluspol an der Katode liegt,
so liegt ein Diodenfehler vor und die Diode muß
ausgetauscht werden.
Bei der Diodenplatte Plus (D+) liegen die Katoden am
Kühlblech, bei der Diodenplatte Minus (D-) die Anoden.
Die Erregerdioden liegen mit der Katode am Anschluß 61.
|
Bild 160. Diode in Ordnung
Bild 161. Gegenprobe - Diode in Ordnung
6.1.10.2. Stator überprüfen
nächster Punkt ; Index
Überprüfung der Statorwicklung
auf Windungsschluß:
Zwischen den einzelnen Phasen (U/V/W, V/W)
sollte ein Widerstand von etwa O,32 Ohm meßbar
sein.
Überprüfung des Stators auf Eisenschluß:
Zwischen dem Statorblechpaket und den
Wicklungsausführungen des Stators wird durch
Zwischenschaltung einer Prüflampe und Anlegen
einer Prüfspannung von 24 V~ der Stator auf
Eisenschluß geprüft. Dabei müssen sämtliche
Kabel U/V/W vom Stator getrennt werden. Beim
Aufleuchten der Lampe ist der Stator defekt
und zu ersetzen.
6.1.10.3. Rotor überprüfen
nächster Punkt ; Index
Überprüfung der Rotorwicklung:
Mittels Widerstandsmeßbrücke ist der Widerstand zu
messen. Er sollte bei 4,2 ± 0,3 Ohm liegen.
Gemessen wird an den Schleifringen nach dem Ausbau
aus dem Fahrzeug.
Die Prüfspitzen sind auf die Schleifringe nur leicht
aufzulegen, um Beschädigungen des Graphit-Schleifringes
zu verhindern.
6.1.10.4. Kohlebürstenlänge überprüfen
nächster Punkt ; Index
Demontage entsprechend Abschnitt
6.1.9.1.
Bei Unterschreitung der Kohlebürstenlänge von 9 mm
ist eine neue Kohlebürste einzusetzen.
6.1.11. Montagehinweise
nächster Punkt ; Index
Lötstellen sind mit säurefreien
Lötmitteln auszuführen und mit Elektro-Isolier-Schutzlack
(lötbar) vor Korrosion zu schützen.
Der Schutz sollte auch neu eingelötete Erregerdioden in
ihrer Gesamtheit erfassen. Dieses kann durch Tauchen des
gesamten Gleichrichters erfolgen. Dabei sind die
Steckanschlüsse abzudecken und nach dem Tauchen von
Lackresten zu befreien.
Stator
Bei der Montage des Stators in die Haltekappe ist darauf
zu achten, daß die Nut des Stators mit der Nut der
Haltekappe übereinstimmt.
Zulässiges Anzugsdrehmoment für die Rotorbefestigungsschraube
M 7/5.8 = 20 ± 2 Nm (2 ± 0,2 kpm).
Zulässiges Anzugsdrehmoment für die Statorbefestigungsschraube
M 5/5.8 = 4 ± 0,5 Nm (0,4 ± 0,05 kpm).
Die Montage des Kohlebürstenhalters ist zweckmäßig
nach der Haltekappenmontage durchzuführen.
Achtung!
Vor dem Anschließen der Batterie die Leitungsführung
überprüfen. Bei vertauschten Anschlüssen D+, D-, 61,
DF besteht die Gefahr der Zerstörung der
Halbleiterbauelemente sowie von Zusatzaggregaten.
Auf richtige Polarität der Batterie (Minus an Masse)
beim Anschließen achten.
Hinweise für die Zündeinstellung sowie das
Anstellen des Schmierfilzes sind aus speziellen
Unterlagen der Fahrzeuge ersichtlich.
6.1.12. Wichtige Hinweise
nächster Punkt ; Index
Beim Laden von Batterien mit netzgebundenen
Ladegeräten ist die Batterie vom Bordnetz des Fahrzeugs
zu trennen.
Bei Ausführung elektrischer Schweißarbeiten am Fahrzeug
ist darauf zu achten, daß +-Leitungen des Bordnetzes
nicht mit der Schweißelektrode in Berührung kommen.
Die Batterie ist abzuklemmen.
Bei laufendem Motor dürfen keine Anschlüsse zwischen
DLM, Gleichrichter und Regler unterbrochen werden, da
sonst Folgeschäden in der elektrischen Anlage auftreten.
Bei Kontrollarbeiten an DLM und Gleichrichter sind die
Meßinstrumente mit sicheren Verbindungen anzuschließen.
Beim Betrieb der Drehstromlichtmaschine ohne Batterie
ist zwischen D+ und D- des Gleichrichters ein Kondensator
2,5 uF, 50 V anzuschließen (An der ETZ 250 neben dem
Leitungsverbinder am Ansauggeräuschdämpfer serienmäßig
vorhanden).
6.2. Regler
nächster Punkt ; Index
Der Drehstromlichtmaschine ist ein
temperaturkompensierter, plusregelnder Regler mit
Knickcharakteristik zugeordnet. Dieser Einsystemregler
14 V, 15 A arbeitet mit Spannungsregelung und
Stromregelung. Die Stromregelung ist auf einen
Maximalstrom von 15 A ausgelegt. In den Regler
eingebaut sind der Regel- (Vorschalt-) Widerstand
(Anschlußseite) und ein Abgleichwiderstand.
6.2.1. Einbau
nächster Punkt ; Index
Um eine einwandfreie Arbeitsweise des
Reglers zu garantieren, ist es notwendig, ihn
schwingungsarm zu befestigen.
Das wurde bei der ETZ 250 in vollem Umfang erreicht,
indem der Reglerschalter mit einer Schaumstofftasche
und einem Gummistopfen elastisch aufgehängt wurde.
Es ist deshalb beim Einbau stets darauf zu achten,
daß der Reglerschalter einwandfrei in die dafür
vorgesehene Halterung hineingeschoben wird.
6.2.2. Wartung
nächster Punkt ; Index
Die Wartung des Reglers beschränkt
sich im allgemeinen auf das Sauberhalten der
Anschlüsse. Bei zu dunklem Scheinwerferlicht,
bei Startschwierigkeiten usw. nicht gleich
den Fehler am Regler suchen oder gar noch
unsachgemäße Eingriffe vornehmen, sondern erst
einmal Leitungen und deren Steckverbindungen auf
einwandfreien Sitz und auf Korrosion überprüfen.
Der Regler darf durch evtl. unter die Sitzbank
gelegte Teile wie Ersatzschlauch usw. nicht
berührt werden.
6.2.3. Einstellung
nächster Punkt ; Index
Vor der elektrischen Einstellung
ist stets erst eine mechanische Voreinstellung bzw.
Korrektur der mechanischen Einstellung vorzunehmen.
Das erleichtert die elektrische Einstellung und
garantiert die Einhaltung der erforderlichen
Spannungs-Strom-Kennlinie.
Eine elektrische Einstellung des Reglerschalters
im Fahrzeug stellt nur eine Notlösung dar
und sollte im Interesse einer optimalen Einhaltung
der Funktion der Stromversorgungsanlage vermieden
werden.
Zur Einstellung des Reglerschalters wird dieser
mit einer typenmäßig zugeordneten Lichtmaschine
auf einen im Drehzahlbereich 0...7000 U/min
kontinuierlich regelbaren Prüfstand genommen.
Die Spannung muß, um Fehler bei der Einstellung
auszuschließen, immer von der Drehzahl "Null"
der Lichtmaschine aus angefahren werden. Gemessen
wird die Spannung zwischen den Klemmen D+ und D-
des Reglers. Das zu verwendende Meßgerät sollte
mindestens Güteklasse 1,5 haben.
Es ist einzustellen:
- geregelte Spannung U3A
Spannung, die bei Belastung der Lichtmaschine mit 3 A
über den gesamten Drehzahlbereich geregelt wird. Sie
muß im angegebenen Toleranzbereich liegen. Kurzzeitige
Spannungaspitzen über den Toleranzbereich hinaus zu
Beginn der Unter- und Oberlageregelung sind nicht
mit falscher Einstellung zu verwechseln.
Die geregelte Spannung kann zwischen Ende der Unterlage-
und zu Beginn der Oberlageregelung um etwa +0,2...-0,1 V
unterschiedlich sein (Spannungssprung).
Der Spannungssprung darf nicht zu stark negativ
eingestellt werden, da sonst der Regler-Anker
"klappert", also ständig zwischen Unter-
und Oberlage pendelt.
- Höchstlastspannung UHI
Spannung, die bei Belastung der Lichtmaschine mit 15 A
bei einer Drehzahl von über 3800 U/min geregelt wird.
- Ansprechstrom IAS
Bei diesem Strom beginnt die Stromregelung zu arbeiten.
Elektrische Einstellwerte
Die nachstehenden Werte gelten für eine Reglertemperatur
von (20 ± 5) °C
Geregelte Spannung: | 13,8 V...14,6 V |
Höchstlastspannung: | 13,0 V...13,5 V |
Ansprechstrom: | 11,5 A...14,0 A |
Achtung:
Die Änderung der geregelten Spannung und des
Ansprechstromes nur durch vorsichtiges Verbiegen
des Federgegenhalters durchführen. Nicht die
Kontaktzungen verbiegen!
6.2.4. Schäden und ihre Ursachen
nächster Punkt ; Index
Hierzu ist im Abschnitt 6.1.
das wesentliche bereits ausgesagt worden.
Außerdem muß beachtet werden:
Das unsachgemäße Aufsetzen der Schutzkappe des
Reglerschalters führt zu einem Masseschluß, wenn
die Kappe mit dem Kern oder mit dem Kontaktwinkel
des Reglerschalters in Berührung kommt. Vor jedem
öffnen des Reglers sind die Sicherungen zu
entfernen. Die an der Seite der Kappe befindlichen
Lappen müssen richtig in die dafür vorgesehenen
Aussparungen am Reglersockel hineingesteckt werden.
Der Drahtbügel muß straff auf die Kappe drücken.
|
Bild 162. Mechanische Reglereinstellung
- mindestens 0,3 mm
- 0,8...1,1 mm
- 0,5 ± 0,1 mm
- 0,5 ± 0,1 mm
- 1,4...1,5 mm
- Kontakte des Spannungsreglers
- Kontakte des Stromreglers (Strombegrenzungsschalter)
Bild 163. Batterieanordnung
- Batterie
- Blinkgeber
- Sicherungsdose
- Ersatzglühlampen
- Bordwerkzeug
Bei der Inbetriebsetzung wird
Akkumulatoren-Schwefelsäure (im folgenden Text nur
noch Elektrolyt genannt) der Dichte 1,28 ± 0,01
g/cm³ (in den Tropen 1,22 ± 0,01 g/cm³)
gemessen bei (20±2)°C in die Batterie
eingefüllt.
Alle Zellen der Batterie sind bis 5 mm über die
Scheideroberkante oder bis zur angegebenen
Säurestandsmarke zu füllen. Die Temperatur des
Elektrolyts darf beim Einfüllen 25 °C nicht
überschreiten.
Nach etwa 2...3 Stunden haben sich die Platten und
Scheider vollgesogen und der Elektrolytstand ist
gesunken.
Es ist nochmals Elektrolyt der gleichen Dichte und
Temperatur bis zur Scheideroberkante nachzufüllen.
Anschließend wird die Batterie mit Gleichstrom
von 0,5 A geladen.
Beim Laden sind die Verschlüsse der Batterie
zu öffnen.
Es muß so lange geladen werden, bis alle Zellen
lebhaft und gleichmäßig gasen und die Spannung
von 2,5...2,7 V je Zelle erreicht ist.
Bei 2...3 Messungen im Abstand von einer Stunde
müssen Elektrolytdichte (1,28 ± 0,01
g/cm³) und Zellspannung konstant bleibt.
Während des Ladens darf die Elektrolyttemperatur
50°C nicht überschreiten. Am Ende der Ladung
ist der Elektrolytstand nachmals zu
überprüfen.
Einbau der Batterie
Bevor die Batterie in das Fahrzeug einbebaut
wird, sind die beiden Batteriekabel (rotes Kabel
an Pluspol - braunes Kabel an Minuspol) an die
Batterie anzuschließen und mit etwas Polfett oder
säurefreier Vaseline zu konservieren. Nach dem
Aufsetzen der Schutzkappe kann die Batterie
eingebaut und die beiden Batteriekabel können
an die Sicherungsdose angeschlossen werden.
Auch hier ist zu beachten:
Rotes Kabel an rotes Kabel,
braunes Kabel an braunes Kabel anschließen!
Der Entlüftungsschlauch ist so zu verlegen, daß aus
diesem evtl. austretende Säure nicht an Lack- oder
Metallteile kommt.
Wartung der Batterie
Die Durchschnittslebensdauer der Batterie beträgt
etwa 2 Jahre. Durch gute bzw. schlechte Pflege
kann diese Zeit verlängert oder auch entsprechend
verkürzt werden. In der Hauptsache beschränken
sich die Pflegearbeiten auf das Sauberhalten der
Anschlußklemmen - sie sind immer leicht mit Polfett
zu konservieren - und die regelmäßige Kontrolle des
Säurestandes (in der kalten Jahreszeit alle 4
Wochen, in der warmen Jahreszeit alle 2 Wochen).
Beim Einfetten der Anschluklemmen ist darauf zu
achten, daß kein Polfett in die Zellen
gelangt.
Ist der Säurestand unter die erforderliche Höhe
gesunken, so darf nur mit destilliertem Wasser
nachgefüllt werden.
Sollte doch einmal Säure aus der Batterie
verschüttet worden sein, so ist die Säuredichte
der nachzufüllenden Menge so zu wählen, daß die
Dichte der gesamten Säuremenge in der Batterie
in geladenem Zustand 1,28 ± 0,01 g/cm³
beträgt.
Bei Nichtgebrauch oder bei einer Fahrstrecke von
täglich weniger als 50 km ist die Batterie jeden
Monat mit 1 A nachzuladen.
6.4. Zündung
6.4.1. Zündspule
nächster Punkt ; Index
Die Zündspule ist vergleichbar mit einem
Transformator, der eine neidrige Spannung in eine hohe
umwandelt. Da aber bekanntlich nur eine Wechselspannung
transformiert werden kann, aber das Bordnetz mit einer
Gleichspannung gespeist wird, muß eine ständige
Spannungsänderung hervorgerufen werden, was der
Unterbrecher gemeinsam mit dem Kondensator besorgt.
|
Bild 164. Zündspule
Die Bordspannung von 12 V wird auf
die Zündspannung von etwa 12000V transformiert. Beide
Anschlußbolzen der Zündspule sind gekennzeichnet.
Die Klemme 1 ist mit dem Unterbrecher und die Klemme 15
mit der Klemme 15/54 am Zündschloß verbunden.
Achtung:
Bei stehendem Motor, eingeschalteter Zündung und
geschlossenem Unterbrecher wird die Zündspule von
einem Strom durchflossen, der bei längerer Zeit die
Zündspule erwärmt. Dabei wird das Isolationsmaterial
zerstört. Die Zündspule schlägt durch und ist
somit unbrauchbar.
6.4.3. Zündeinstellung
nächster Punkt ; Index
- Einstellung des Unterbrecherabstandes
Bevor mit der Einstellung begonnen wird, ist es notwendig,
die Unterbrecherkontakte einer Kontrolle zu unterziehen.
Dazu werden die Kontakte am besten ausgebaut (siehe Bild
165).
Die Schraube (7) wird herausgedreht, die Stromschiene nach
oben gedrückt, die Befestigungsschraube (8) entfernt und die
Unterbrechergrundplatte mit Unterbrecher abgehoben. Sind
auf den Kontaktflächen kleine Brandstellen zu erkennen,
können diese mit einer feinen Schmirgelfeile gesäubert werden.
Bei starkem Abbrand der Kontakte muß die Unterbrechergrundplatte
mit Unterbrecher ausgewechselt werden.
Beim Einbau ist darauf zu achten, daß die Verstellplatte
(4) sauber und ölfrei ist, ebenso der komplette Unterbrechersatz.
Bei Nichtbeachtung kommt es zu Zündaussetzern und insbesondere
zu Startschwierigkeiten. Am Lagerbolzen (5) sind die alten
Schmiermittelreste zu entfernen und der Unterbrecherhammer
ist mit wenig Unterbrecheröl aufzusetzen. Die Unterbrecherkontakte
sind so einzustellen, daß die Kontakte parallel zueinander
stehen.
Die Kurbelwelle wird bei Einstellung des Kontaktabstandes
soweit gedreht, daß die Anlaufnase des Unterbrecherhebels
auf die höchste Stelle des Nockens kommt.
Die Befestigungsschraube (8) wird gelöst und mit der
Exzenterschraube (9) der Kontaktabstand so eingestellt,
daß sich die Fühllehre gerade durch die Kontakte
hindurchziehen läßt.
Die Befestigungsschraube (8) festziehen und nochmals
mit der Fühllehre den Kontaktabstand überprüfen.
Der eingestellte Unterbrecherabstand muß beim Durchdrehen
der Kurbelwelle während des gesamten Öffnungswinkels
konstant bleiben, er darf keinesfalls größer werden.
Es handelt sich dann um einen Nockenschlag, der bei
höheren Umdrehungen zu Zündaussetzern führt.
Einstellung des Zündzeitpunktes
|
Bild 166. Zündeinstellehre 29-50.801 eingeschraubt
(3,0-0,5mm
vor OT oder 22°15'-2° Kurbelwinkel)
Die Einstellung erfolgt mit Zündeinstellehre 29-50.801
und Prüflampe.
Die Zündeinstellehre wird in das Zündkerzengewinde
eingeschraubt, und durch Drehen der Kurbelwelle in
Uhrzeigerrichtung stellt sich die Skala der Einstellehre
automatisch auf den oberen Totpunkt (OT) ein.
|
Bild 167. Prüflampe angeklemmt
Der Zeiger der Einstellehre steht im OT
des Kolbens auf "0" der Schleppskala.
Die Prüflampe mit einer Glühlampe (G) 12 V und max.
2 Watt wird auf der Plusseite (1) an die Stromschiene
(vom Unterbrecher zum Kondensator) angeklemmt und auf
der Minusseite (M) an das Motorengehäuse oder den
Zylinder angelegt.
Durch Weiterdrehen der Kurbelwelle um etwa 340 Grad in
Drehrichtung rechts wird der Zeiger der Einstellehre über
die Skalenwerte 5...4 (mm) am Zündzeitpunkt 3 (mm) der
Schleppskala ankommen. Beginnt an diesem Punkt die
Prüflampe aufzuleuchten, (Batterie an Bordnetz angeschlossen
und Zündung eingeschaltet), so ist der Zündzeitpunkt
richtig eingestellt.
Leuchtet die Prüflampe zu zeitig (z.B. zwischen den
Skalenwerten 4 und 3) auf, dann öffnen die
Unterbrecherkontakte zu zeitig und die Verstellplatte
(4) muß nach dem Lösen der Befestigungsschrauben (13)
in Drehrichtung nach rechts verschoben werden. Leuchtet
die Prüflampe nach dem Skalenwert 3 (z.B. am Skalenwert 2)
auf, dann öffnen die Unterbrecherkontakte zu spät und
die Verstellplatte (4) muß entgegen der Drehrichtüng
nach links verschoben werden (siehe dazu Bild
165).
|
Bild 168. Überprüfung des Zündzeitpunktes mit fremder Stromquelle
Nach jeder Verstellung der Verstellplatte
(4) ist der Unterbrecherabstand zu überprüfen und
nötigenfalls nachzustellen. Die Messung des
Zündzeitpunktes muß solange wiederholt werden, bis
die Prüflampe bei der Aufwärtsbewegung des Kolbens
am Skalenwert 3-0,5
aufleuchtet.
Wird zur Einstellung des Zündzeitpunktes eine fremde
Stromquelle (nicht Bordnetz) verwendet, dann
erlischt die Prüflampe, wenn sich die Unterbrecherkontakte
öffnen.
Achtung:
Keinesfalls darf der Unterbrecher früher als
3,0-0,5 mm vor OT
öffnen, da sonst die Verbrennung im Motor zu zeitig
abgeschlossen ist und der Verbrennungsdruck drückt
bereits vor dem OT auf den Kolben, was Überhitzung,
Leistungsabfall und hohen Verschleiß des Motors
bedeutet.
6.4.4. Zündkerze
nächster Punkt ; Index
Die Zündkerze besteht im wesentlichen
aus 3 Teile. Das sind der Isolierkörper, die
Mittelelektrode und das Stahlgehäuse mit Masseelektrode.
Zwischen Mittelelektrode und Masseelektrode springt der
Funke über und entzündet damit das Kraftstoff-Luft-Gemisch.
|
Bild 169. Unsachgemäßes Ein- und Ausschrauben der Zündkerze
Der Isolierkörper muß eine sehr
hohe elektrische Durchschlagfestigkeit haben. Um die
Durchschlagfestigkeit immer zu gewährleisten, ist die
Kerze auch entsprechend vorsichtig zu behandeln.
Durch unsachgemäße Behandlung (Schlag, Stoß) können
kaum sichtbare Haarrisse entstehen, und schon ist die
Zündkerze unbrauchbar.
Die Lebensdauer einer Kerze liegt bei Zweitaktmotoren
durchschnittlich bei 10000 Fahrkilometern. Nach dieser
Laufleistung ist es generell richtig, die Kerze
gegen eine neue auszutauschen.
Die ETZ 250 ist mit einer Zündkerze M 14/260
ausgerüstet. Es sit zweckmäßig, immer eine solche
Kerze (Wärmewert beachten) zu verwenden.
Ein niedriger Wärmewert im Winter oder ein höherer
im Sommer bringt keine Vorteile, eher Nachteile;
kann aber in extremen Klimazonen erforderlich
sein.
Auch der richtige Sitz der Kerze ist zu beachten.
Das Gewinde der Kerze muß mit dem Gewinde im
Zylinderdeckel bündig abschließen. Ragt die Kerze
zu weit in den Verbrennungsraum hinein (kein oder
ein flachgedrückter Dichtring unter der Kerze) oder
steht die Kerze zu weit außen (2 Dichtringe unter
der Kerze), so kommt es zum Wärmestau und zu
Überhitzungserscheinungen.
Die Wartungsansprüche der Kerze sind relativ
gering. Der Elektrodenabstand ist etwa aller
2500 km zu kontrollieren und die Kerzenelektroden
sind zu reinigen.
Beim Kerzenwechsel ist ein einwandfrei passender
Kerzenschlüssel zu verwenden, um einen Bruch des
Isolierkörpers zu vermeiden (Bild 169).
In jedem Fall ist auch auf das Aussehen des
"Kerzengesichts" zu achten. Es
ermöglicht nach längerem Einsatz der Kerze
Schlußfolgerungen über die Arbeitsweise des Motors,
die Gemischbildung, den verwendeten Kraftstoff, die
Vergasereinstellung und Eignung der Kerze für den
Motor.
Das richtige Kerzengesicht:
Stirnfläche zum Zündkerzengewinde schwarz und die
Isolierkörperspitze mit Masseelektrode graugelb
bis rehbraun.
6.4.5. Zündleitungsstecker (Kerzenstecker)
nächster Punkt ; Index
Die Aufgabe des Zündleitungssteckers ist es,
eine Verbindung zwischen Zündkerze und Zündkabel herzustellen
und das elektrische Feld der Zündkerze nach außen
abzuschirmen.
Um die Zündkerze einwandfrei zu entstören, ist darauf zu
achten, daß der am Zündleitungsstecker befestigte Blechmantel
richtig auf dem Sechskant der Zündkerze sitzt.
Auf keinen Fall darf der Blechmantel entfernt werden, da es
sonst zu Störungen im UKW- und Fernsehempfang kommt.
Genau wie die Zündkerze ist auch der Zündleitungsstecker
sorgsam zu behandeln. Haarrisse im Isolierkörper, die zu
einer Kriechfunkenstrecke führen, machen ihn unbrauchbar.
Zündaussetzer entstehen, wenn der Kerzenstecker innen
feucht, verschmutzt oder verölt ist.
6.4.6. Störungen in der Zündanlage
nächster Punkt ; Index
Durch Verschleiß und Alterung der einzelnen
Geräte können Störungen in der Zündanlage hervorgerufen
werden.
Nachfolgend werden hier einige hauptsächlich auftretende
Ursachen und deren Auswirkungen genannt:
- Nockenbahn schlecht geschmiert
Verschleiß der Anlaufnase des Unterbrechers zu kleiner
oder kein Kontaktabstand =
Startschwierigkeiten, unregelmäßiger Lauf, Leistungsabfall
- Kondensator schlägt durch
hoher Kontaktverschleiß =
Zündaussetzer bei höheren Drehzahlen
- Einstellung des Kontaktabstandes bei starker
Kraterbildung auf den Kontaktflächen
der wahre Abstand ist zu groß =
Zündaussetzer bei höheren Drehzahlen, schwacher Zündfunke, Leistungsabfall
- Kurbelwellenlager ausgeschlagen
zu große Rundlaufabweichung der Kurbelwelle und
somit des Nockens, Kohlebürsten und Unterbrecher
"springen" =
- Geringe Anpreßkraft der Kontaktfeder (Unterbrecher)
Unterbrecherhebel hat keine exakte Führung auf der
Nockenbahn =
Zündaussetzer bei höheren Drehzahlen
Zündleitungsstecker:
- Zwischen dem Isolierkörper der Zündkerze und
dem Preßteil des Zündleitungssteckers ist Staub
und Wasser =
Startschwierigkeiten, Zündaussetzer
- Durch unsachgemäße Behandlung ist der
Isolierkörper gerissen (Haarrisse)
Kriechfunkenstrecke zu Masse =
Startschwierigkeiten, schwacher Zündfunke, Leistungsabfall
Leitungen:
- Defekte Isolation der Hochspannungsleitung (Zündkabel)
Funkenüberschlag auf Masse (Zylinderdeckel) =
Startschwierigkeiten, vor allem bei feuchter Witterung,
Zündaussetzer bei hohen Drehzahlen
- Abgebrochene Leitungen
Kurzschluß =
- Flachsteckanschlüsse stark korrodiert
sehr hoher Übergangswiderstand =
die an den Geräten anliegende Spannung ist zu niedrig.
6.5. Licht- und Signalanlage
6.5.1. Scheinwerfer
nächster Punkt ; Index
Der Scheinwerfer wird geöffnet, indem
man die Zylinderschraube löst und das Vorderteil vom
Scheinwerfergehäuse abnimmt. Das Vorderteil besteht aus
dem verchromten Frontring, dem Reflektor mit der
Streuscheibe, der Bilux- und Standlichtlampe und ihrer
Halterung.
|
Bild 170. Scheinwerfergehäuse
Im Scheinwerfergehäuse befinden sich zwei
Leitungsverbinder (1) und eine Massepunktschraube (2), die als
Sammler aller im Scheinwerfer zusammenlaufenden Massekabel
verwendet wird.
Achtung:
Als Leitungsverbinder darf nur der im Bild 171
geöffnet gezeigte verwendet werden!
|
Bild 171. Leitungsverbinder für Scheinwerfer und für die innere Elektrik
Beim Auswechseln der Biluxlampe ist folgendes
zu beachten:
Das Klemmstück (Duroplastteil), das die elektrische Verbindung
zur Lampe herstellt, wird gerade abgezogen - nicht verkanten -,
da sonst die Kontaktbleche verbogen werden. Der Stromfluß kann
dadurch unterbrochen werden.
Die Kabel, die zu den Klemmen 31, 56a, 56b führen, brauchen
nicht abgeklemmt zu werden. Es ist aber ratsam, sie auf festen
Sitz zu überprüfen. Lediglich das Kabel 58 (Standlicht) ist
zu lösen.
Die Halterung (1) für die Bilux- und Standlichtlampe wird
durch Ausheben der Haltefeder (H) aus der oberen Blechnase
des Reflektors gelöst. Nun kann die Biluxlampe aus dem
Reflektor herausgehoben werden. Der Glaskörper der Lampe
darf nicht mit der bloßen Hand angefaßt werden. Auch saubere
Finger hinterlassen Fettspuren!
|
Bild 172. Vorderteil des Scheinwerfers mit Lampenhalterung
Beim Einbau ist darauf zu achten, daß
die Nase am Lampensockel genau in den Einschnitt des
Reflektors zu liegen kommt.
|
Bild 173. Verstellen des Scheinwerfers
Bei mangelnder Fahrbahnausleuchtung sind
die Kontaktstellen der Zuleitungen zur Biluxlampe zu
überprüfen und wenn nötig, gründlich zu reinigen.
Verschmutzte Kontakte verursachen einen erheblichen
Spannungsabfall!
Bei älteren Fahrzeugen kann der eflektor matt geworden
sein. Es ist im Interesse der eigenen Sicherheit
erforderlich, ihn gegen einen neuen auszutauschen. Die
Streuscheibe und der Reflektor sind miteinander
verklebt, sie können nicht einzeln ausgetauscht
werden.
Der Scheinwerfer läßt sich nach dem Lockern der
Befestigungsmutter (1) verstellen.
Das richtige Einstellen des Scheinwerfer-Abblendlichtes
wird nach dem Schema im Bild 174
durchgeführt.
|
Bild 174. Scheinwerfer-Einstellschema
Das Fahrzeug wird nach dem Schema
aufgestellt und entsprechend den überwiegenden
Betriebsverhältnissen belastet. Die Federbeine sind
dementsprechend "hart" oder "weich"
gestellt.
Die Hell-Dunkel-Grenze muß genau an der Z-Linie liegen,
und der Knick muß zwischen den Linien V-V und W-W
liegen. Wurde der Scheinwerfer nach dieser Vorschrift
eingestellt, dann wird die Hell-Dunkel-Grenze in allen
Betriebs- und Belastungszuständen die richtige Höhe
haben.
6.5.2. Brems-Schluß-Kennzeichen-Leuchte (BSKL)
nächster Punkt ; Index
Die Brems-Schluß-Kennzeichen-Leuchte ist
mit Kugellampen ausgerüstet, die wie allgemein üblich in
Fassungen mit Bajonettverschluß gehalten werden.
|
Bild 175. Brems-Schluß-Kennzeichen-Leuchte innen (teilweise aufgeschnitten)
Die Glühlampen und Kabelanschlüsse
sind nach dem Herausdrehen der Befestigungsschrauben
(Pfeile) und dem Abnehmen der Lichtaustrittsscheibe
zugänglich.
Auch bei der BSKL kommt es auf feste, nicht korrodierte
Anschlüsse an. Bei der Montage die Lichtaustrittsscheibe
nach dem Auflegen der Dichtung so verschrauben, daß die
BSKL vor Feuchtigkeit geschützt ist, aber die
Lichtaustrittsscheibe nicht zerbricht.
6.5.3. Zündlichtschalter
nächster Punkt ; Index
Der Zündlichtschalter ist der Hauptschalter
der elektrischen Anlage.
Mit ihm werden geschaltet (vergl. Bild 176
und Stromlaufplan, Bild 184):
- Alles ausgeschaltet, Zündschlüssel abziehbar
- Parkstellung bei Nacht (Standlicht), Zündschlüssel abziehbar
- Fahrt bei Tag (Zündung eingeschaltet) Zündschlüssel nicht abziehbar
- Zündung eingeschaltet, Standlicht leuchtet, Zündschlüssel nicht abziehbar
- Fahrt bei Nacht, Zündung und Hauptlicht eingeschaltet, Zündschlüssel nicht abziehbar.
|
Bild 176. Schaltstellungen Zündlichtschalter
Der Aus- und Einbau des Zündlichtschalters
ist aus Bild 177 ersichtlich. Bei der
Luxusausführung (A im Bild 177) muß
der Instrumenten- (Lenker-) Halter (1) vom oberen Klemmkopf
abgeschraubt werden. Erst dann ist die Abdeckkappe (2)
und der Zündlichtschalter zugänglich.
|
Bild 177. Explosivdarstellung Instrumentenhalter
- Luxusausführung
- Standardausführung
Um bei eventuellem Wechsel des
Zündlichtschalters die Kabel wieder an die richtigen
Fahnen stecken zu können, wurden im Bild a href=#b178>178
die einzelnen Anschlüsse noch einmal deutlich gekennzeichnet.
|
Bild 178. Anschlüsse des Zündlichtschalter
Der im Bild 178 gezeigte
Zündlichtschalter ist für ältere MZ-Typen nicht verwendbar,
da die frühere Schaltstellung (5) nicht mehr elektrisch
geschaltet ist. Umgekehrt kann jedoch ein Zündlichtschalter
älterer Typen auch für die ETZ 250 verwendet werden.
Einbauhinweis:
Der Pfeil im Bild 178 zeigt die
Einbaulage des Zündlichtschalters in Fahrtrichtung,
Anschlüsse nach unten.
6.5.4. Schalterkombination am Lenker
nächster Punkt ; Index
Die Schalterkombination am Lenker links
enthält nachstehende Schalter (Bild 179):
- Abblendschalter
- Schalter für Fahrtrichtungsanzeige
L = Blinker linke Seite
R = Blinker rechte Seite
- Schalter für Signalhorn
- Schalter für Lichthupe
|
Bild 179. Schalterkombination am Lenker
Die Einzelschalter sind im Gehäuse mit
Blechschrauben (Schalter für Fahrtrichtungsanzeige A und
Schalter für Signalhorn B1
und Lichthupe B2) bzw.
durch Betätigungsschieber und Feder (Abblendschalter C)
befestigt. An den Schaltern sind bereits vom Hersteller
die Kabel angelötet.
|
Bild 180. Einzelschalter der Schalterkombination am Lenker
Achtung!
Die Schalterkombination der Kleinkrafträder Simson S51
kann nicht für die ETZ 250 verwendet werden, da an den
mit MZ gleichen Schaltern andere Kabel angelötet sind!
6.5.5. Bremslichtschalter
nächster Punkt ; Index
Es sind zwei Bremslichtschalter bei der
Ausführung mit Scheibenbremse angebaut. Auch die
Trommelbremse vorn kann mit einem Bremslichtschalter
ausgerüstet werden, der Schalter in der Hinterradnabe
entspricht.
|
Bild 181. Hinterradbremse und Bremslichtschalter einstellen
Zum Einstellen des Bremslichtschalters
wird die Steckverbindung (2) gelöst und die Kontermutter
soweit gelockert, bis man die hintere Mutter einwandfrei
mit dem Maulschlüssel fassen kann. Diese wird eine
viertel Umdrehung gelockert.
Nun drückt ein Helfer den Bremsfußhebel so weit
nieder, bis beim Drehen des Hinterrades die Bremsbacken
an der Bremstrommel zu schleifen beginnen. Der Bremshebel
ist in dieser Stellung festzuhalten und die Stellschraube
so weit zu drehen, bis das Bremslicht aufleuchtet.
Die Zündung ist bei dieser Arbeit einzuschalten und das
Kabel anzuschließen. Anschließend sind beide Muttern wieder
festzuziehen. Die hintere Mutter ist gefühlvoll anzuziehen,
da die Isolierbuchse ein Plastteil ist. Hierbei ist die
Stellschraube (3) mit einem Schraubendreher gegen
Verdrehung zu sichern.
Reicht der Verstellbereich nicht aus, dann muß der
Gegenhalter ausgebaut und die Kontaktfeder am
Bremsschlüssel nachgerichtet werden.
6.5.6. Blinkanlage
nächster Punkt ; Index
Die ETZ 250 hat eine 4-Leuchten-Blinkanlage,
ausgerüstet mit 21-Watt-Kugellampen.
Beim Austausch der Blinklampen dürfen nur 21-Watt-Lampen
eingebaut werden. Andere Lampen, z.B. 15 Watt, verändern
die vorgeschriebene Blinkfrequenz von 90 ± 30
Perioden/Minute.
Die Kontrolle der Fahrtrichtungsanzeige übernimmt eine
Kontrolleuchte(Nr. 4 im Bild 185).
Die beiden vorderen Blinkleuchtenstreuscheiben sind mit
einem größeren Rand (1) als die beiden hinteren versehen.
Dieser Rand dient dem Fahrer zur Kontrolle seiner
Blinkanlage.
|
Bild 182. Blinkleuchte vorn
- Rand zur Kontrolle der Blinkfunktion
- Plastreflektor
- Anschlußklemmen
- Dichtung
Der Ausfall einer Blinkleuchte wird
durch eine erhöhte Blinkfrequenz (>150 Perioden/Minute)
der vorderen Blinkleuchten angezeigt. Abgesichert ist die
gesamte Blinkanlage durch eine 4-A-Sicherung (siehe Bild
163).
Der Blinkgeber ist am Batteriehaltedeckel mit
den Anschlüssen nach unten elastisch aufgehängt.
Achtung!
Die vom Zündschloß kommende Leitung mit Pluspotential
ist an die Klemme 49 und die vom Blinkschalter kommende
Leitung mit Minuspotential an die Klemme 49a des
Blinkgebers anzuschließen.
|
Bild 183. Blinkleuchte hinten
- Dichtung
6.5.7. Signalhorn
nächster Punkt ; Index
Das Signalhorn ist am Rahmen unter
dem Kraftstoffbehälter befestigt.
Bevor der Zylinderdeckel oder der Zylinder ausgebaut werden
können, muß das Signalhorn abgeschraubt werden.
Bringt das Signalhorn beim Betätigen des Druckschalters nicht
mehr die nötige Lautstärke, dann sind die Zuführungskabel,
deren Anschlüsse und der Druckschalter selbst auf verschmutzte
Kontaktstellen hin zu überprüfen. In diesem Fall wäre die
anliegende Spannung zu niedrig.
Ist das nicht die Ursache, dann wird die Stellschraube am
Horn probeweise ein wenig nach links oder rechts verstellt,
bis der Ton wieder laut genug zu hören ist.
6.5.8. Stromlaufplan
nächster Punkt ; Index
Aus dem Stromlaufplan, Bild
184, können bei Reparaturen an den
Verbrauchern bzw. der übrigen elektrischen Anlage die
erforderlichen Angaben über Kabelverlauf und Kabelfarben
entnommen werden.
Der elektrische Schaltplan liegt diesem Reparaturhandbuch
als Faltblatt bei.
|
Bild 184. Stromlaufplan
Legende zu Bild 184, Stromlaufplan
1 | Batterie |
1a | Kondensator |
2 | Zünd-Licht-Schalter |
3 | Lichtmaschine |
4 | Gleichrichter |
5 | Regler |
6 | Ladekontrolleuchte (bei Standardausführung auch für Kontrolle der Fahrtrichtungsanzeige) |
7 | Leergangkontrolleuchte (nur Luxusausführung) |
7a | Schalter für Leergangkontrolleuchte |
8 | Schalter für Signalhorn (Schalterkombination am Lenker |
9 | Signalhorn |
10 | Schalter für Lichthupe (Schalterkombination am Lenker) |
11 | Abblendschalter (Schalterkombination am Lenker) |
12 | Kontrolleuchte für Fernlicht |
13 | Lampe für Scheinwerfer |
| a Fernlicht |
| b Abblendlicht |
14 | Beleuchtung für Drehzahlmesserskala (nur Luxusausführung) |
15 | Beleuchtung für Tachometerskala |
16 | Standlicht im Scheinwerfer |
17 | Rücklicht und Kennzeichenbeleuchtung (in der Brems-Schluß-Kennzeichenleuchte unten) |
17a | Steckdose für Begrenzungsleuchten (nur mit Seitenwagenbetrieb) |
17b | Steckdose für Masse (nur mit Seitenwagenbetrieb) |
18 | Zündspule |
19 | Unterbrecher der Zündanlage |
20 | Zündkerze mit Entstörstecker |
21 | Bremslichtschalter-Vorderradbremse |
22 | Bremslichtschalter-Hinterradbremse |
23 | Bremslicht (in Rückleuchte oben) |
24 | Blinkgeber |
25 | Schalter für Fahrrichtungsanzeige (Schalterkombinatiom am Lenker) |
26 | Kontrolleuchte für Fahrtrichtungsanzeige (nur Luxusausführung) |
27 | Blinkleuchte vorn links |
28 | Blinkleuchte hinten links |
29 | Blinkleuchte vorn rechts |
30 | Blinkleuchte hinten rechts |
30a | Steckdose für Blinkleuchten (nur mit Seitenwagenbetrieb) |
31 | Scahltsymbole für: |
| a Flachstecker |
| b Hülse für Flachsteckeranschluß bzw. Steckdose |
| c Masse |
| d lösbare Verbindung (Schraube, Klemme) |
| e feste Verbindung |
LVR | Leitungsverbinder im Scheinwerfer, rechts |
o | oben |
u | unten |
v | vorn |
x | belegter Anschluß |
LVL | Leitungsverbinder im Scheinwerfer, links |
o | oben |
u | unten |
v | vorn |
x | belegter Anschluß |
LVF | Leitungsverbinder am Fahrgestell, oben am Filtergehäuse |
v | vorn |
h | hinten |
x | belegter Anschluß |
Si | Sicherungsdose |
l | links |
r | rechts |
MA | Massepunkt Scheinwerfer |
MB | Massepunkt Brems-Schluß-Kennzeichenleuchte |
ML | Masse Lampe für Scheinwerfer |
MC | Massepunkt Fahrzeug (am Leitungsverbinder LVF) |
MD | Massepunkt Lichtmaschine |
MT | Massepunkt Tachometer |
| |
Kabelfarben: |
br | braun |
rt/sw | rot-schwarz |
sw | schwarz |
sw/ws | schwarz-weiß |
ws/sw | weiß-schwarz |
gr | grau |
gn/rt | grün-rot |
bl | blau |
ge | gelb |
rt | rot |
sw/rt | schwarz-rot |
sw/bl | schwarz-blau |
sw/gn | schwarz-grün |
ws | weiß |
gn | grün |
gn/bl | grün-blau |
bl/ws | blau-Weiß |
rt/ge | rot-gelb |
br/sw | braun-schwarz |
| |
¹) strichpunktierte Leiter nur bei Standardausführung vorhanden |
²) gestrichelte Leiter nur bei Luxusausführung vorhanden |
6.6. Instrumente und Kontrolleuchten
nächster Punkt ; Index
Die Anordnung der Instrumente geht aus
dem Bild 177 hervor. Die
Standardausführung der ETZ 250 wird nur mit
einem Tachometer (rechts im Instrumentenhalter)
ausgerüstet.
Die Luxusausführung hat außer dem ebenfalls rechts
angeordneten Tachometer auf der linken Seite einen
mechanisch von der Kurbelwelle angetriebenen
Drehzahlmesser (siehe auch Bild 88).
Die Anordnung und Bedeutung der Kontrolleuchten ist
im Bild 185 enthalten. Über die
Verkabelung bzw. Zusammenschaltung mit anderen
elektrischen Geräten sind die notwendigen Angaben
im Stromlaufplan, Bild 184,
vorhanden.
|
Bild 185. Anordnung der Kontrolleuchten
- Leerganganzeige, gelb, (nur Luxusausführung);
- Kontrolleuchte für Lichtmaschine, rot, (nur Luxusausführung);
- Fernlichtkontrolle, blau;
- Kontrolle der Fahrtrichtungsanzeige grün (bei Standardausführung gleichzeitig Kontrolleuchte für Lichtmaschine).
Tachometer und Drehzahlmesser sind bei
Nachtfahrt beleuchtet. Dazu dienen die im Bild
186 mit (3) gekennzeichneten
Lampen, die über den Flachsteckanschluß (4) Masse
erhalten. Die Funktion der mit (1) gekennzeichneten
Lampen geht aus Bild 185 hervor.
Den Kontrolleuchten (1) wird das fehlende elektrische
Potential über die Flachsteckanschlüsse (2)
zugeführt.
|
Bild 186. Anordnung der Lampen in den Instrumenten
Der Ausbau der Lampen aus den
Instrumenten wird möglich, nachdem die Flachstecker
von den senkrechten Anschlüssen der Lampen abgezogen
sind. Die Lampen lassen sich danach leicht aus dem
Instrumentengehäuse ziehen.
7. Ansaugsystem
7.1. Beschreibung und Funktion der Anlage
nächster Punkt ; Index
Die gesamte Ansauganlage ist ein in sich und
auf den Motor optimal abgestimmtes System. Jede Veränderung
an dieser Anlage wird sich nachteilig auf die Leistung, den
Verbrauch, den Verschleiß usw. auswirken.
|
Bild 187. Ansauggeräuschdämpfer und Luftfilter
Bild 188. Montage des Ansaugrohres
Die Ansauganlage beginnt an der unter
dem Regler befindlichen Öffnung und endet am Einlaßkanal
des Zylinders. Es darf an der gesamten Anlage keine
Stelle geben, die es ermöglicht, zusätzlich Luft
anzusaugen, außer an den dafür vorgesehenen Bohrungen
Folgenden Weg muß die Luft und ab dem Vergaser das
Kraftstoff-Luft-Gemisch zurücklegen, um in den
Kurbelraum zu strömen:
Die Luft wird durch die Öffnung (A) des Ansaugrohres
(1), siehe Bild 87, angesaugt. Das
Ansaugrohr dient der Geräuschdämpfung und der
Luftberuhigung.
Nach dem Verlassen des Ansaugrohres strömt die Luft
im Rahmenträger zurück und tritt in das mit dem
Rahmenrohr dicht verschraubte Luftfiltergehäuse (L),
siehe Bild 187, ein.
Beim Durchgang durch das Luftfilter wird die Luft
gesäubert. Die mitgeführten Staubteilchen bleiben
im Filter haften. Anschließend werden im
Ansauggeräuchdämpferraum (1) die durch die
Ansaugschwingungen entstehenden Druckunterschiede
weitgehendst ausgeglichen.
Die Luft wird dann durch das Anschlußstück (2), das
durch den Klemmring (3) am Vergaser befestigt ist,
hindurch bis zum Vergaser gesaugt.
Im Vergaser wird die ankommende Luft mit dem
zerstäubten Kraftstoff in einem bestimmten Verhältnis
gemischt. Dieses Kraftstoff-Luft-Gemisch strömt
dann durch den Einlaßkanal in den Kurbelraum des
Motorengehäuses.
7.1.1. Luftfilter
nächster Punkt ; Index
Für die ETZ wird ein Trockenluftfilter
verwendet. Das Luftfilter (4) befindet sich im
Luftfiltergehäuse.
Es wird auf der einen Stirnseite im Gehäuse und auf
der anderen durch einen Napf (5), der auf einem
Gewindebolzen geführt und befestigt wird, zentriert
(Bild 187).
Damit das Filter einwandfrei an seinen beiden
Stirnflächen abgedichtet wird, sind der Napf (5) und
der Deckel (7) so zu verschrauben, daß das Luftfilter
fest sitzt und die Dichtung (6) ihre Funktion
erfüllen kann.
Das Luftfilter ist zugänglich nach Ausbau der
Batterie. Der Staub setzt sich an der Außenseite des
Filters an. Beim Reinigen ist das zu beachten. Das
Trockenluftfilter wird durch leichtes Ausklopfen oder
durch Ausbürsten mit einem trockenen sauberen
Haarpinsel gereinigt.
7.1.2. Ansauggeräuschdämpfer
nächster Punkt ; Index
Das Ansauggeräuschdämpfergehäuse besteht
aus 2 Leichtmetallgußteilen, die unlösbar miteinander
verschraubt sind.
An diesem Gehäuse ist das Luftfiltergehäuse (L)
befestigt.
Der Geräuschdämpfungsraum (1) dient einmal zur Einhaltung
der Lautschtärke des Ansauggeräusches und einmal als
Vorratsbehälter für die vom Motor zur Verbrennung benötigten
Luft.
Das Ansauggeräuschdämpfergehäuse ist durch 3 Schrauben mit
dem Rahmen verbunden.
Der ebenfalls zur Geräuschdämpfung dienende Ansaugschlauch
(1), siehe Bild 188, ist im Rahmenträger
hinten direkt im Blechausschnitt mit Hilfe einer Nut im
Gummi befestigt. Ein Anguß am vorderen Ende des Schlauches
(H) hält letzteren in der Öffnung (Ö) des Rahmenträgers.
Der Austausch des Ansaugschlauches wird möglich, nachdem
die Ansauganlage, der Hinterradkotflügel und das Hinterrad
ausgebaut wurden.
Ein Besenstiel (S) oder ein anderer Holzstab erleichtern
das Einfädeln des Angusses (H) in die Öffnung (Ö).
7.1.3. Anschlußstück zum Vergaser
nächster Punkt ; Index
Das Anschlußstück ist ein Gummiformteil, das
die Verbindung zwischen Ansauggeräuschdämpfer und Vergaser
herstellt.
Es ist darauf zu achten, daß die Wand der Bohrung im
Ansauggeräuschdämpfergehäuse einwandfrei in der dafür
vorgesehenen Nut im Anschlußstück sitzt und daß das andere
Ende des Anschlußstückes fest mit dem Vergaser, mit Hilfe
eines Klemmringes, verbunden ist.
Das Anschlußstück ist von Zeit zu Zeit auf poröse Stellen,
hauptsächlich im Bereich der Falten, zu überprüfen.
7.1.4. Vergaser
nächster Punkt ; Index
Bei der ETZ wird ein BVF-Vergaser vom Typ
30N2-5 verwendet. Er ist ein Vergaser mit einer
Kaltstarteinrichtung.
7.1.4.1. Aufbau und Funktion des Vergasers
nächster Punkt ; Index
Der Vergaser besteht aus 2 Systemen. Um ihren
Aufbau und ihre Funktion genau kennenzulernen, ist es günstig,
jedes System einzeln zu erläutern.
|
Bild 189. Startkolben geschlossen (Fahrtstellung)
Bild 190. Hebel für Startvergaser
- Fahrtstellung
- Stellung Kaltstart
1. Kaltstarteinrichtung
Wie es schon der Name sagt, handelt es sich bei dieser
Einrichtung darum, das Starten des Motors im kalten
Zustand zu erleichtern.
Die Kaltstarteinrichtung ist auf dem Bild 189
(FahrtStellung, Hebel für StartVergaser am Lenker liegt
nach vorn am Anschlag an) und auf dem Bild 191
(Kaltstart, Hebel für Startvergaser am Lenker ist zum
Fahrer hin gezogen) zu sehen.
In der Fahrtstellung des Hebels für Startvergaser am
Lenker muß die Dichtung (2) am Startkolben (1) das
Startmischrohr (3) vollkommen abschließen.
Die Seilzugstellschraube (4) ist deshalb immer so
einzustellen, daß zwischen Seilzughülle und Stellschraube
etwa 1 mm Spiel vorhanden ist.
Wird der Hebel für Startvergaser am Lenker in
Kaltstartstellung gebracht (Hebel zum Fahrer hin
gezogen), dann wird der Startkolben mit der Dichtung
angehoben und somit die obere Öffnung des
Startmischrohres (A), Bild 191,
freigegeben.
|
Bild 191. Startkolben angehoben (Kaltstart)
Der im Startmischrohr stehende
Kraftstoff wird beim Starten des Motors hochgesaugt
und durch den Startkanal (5), Bild 191,
der nach dem Gasschieber im Ansaugkanal mündet,
weitergeleitet.
Um für den Kaltstart im Startsystem den erforderlichen
Unterdruck zu haben, muß der Gasschieber in der
Leerlaufstellung stehen.
Die Startvorrichtung ist unwirksam, wenn beim
Starten des Motors der Gasschieber über das
LeerlaufSystem hinaus angehoben wird!
Die untere Öffnung des Startmischrohres mündet in
einen separaten Raum, den Startschacht, der nur durch
die Startdüse (6), Bild 191, mit
dem Raum für den Zentralschwimmer verbunden ist.
Die Bohrung der Startdüse ist so abgestimmt, daß nach
dem Absaugen der im Startmischrohr stehenden
Kraftstoffmenge nur soviel Kraftstoff nachfließen
kann, daß der Motor bei lange gezogenem Starthebel
das zugeführte überfettete Gemisch gerade noch
verarbeiten kann.
Der benötigte Kraftstoff zum Starten wird bereits
im Startschacht vorgemischt.
Die dazu benötigte Luft wird durch eine in der Oberkante
der Trennwand befindliche Aussparung aus dem Raum für
den Zentralschwimmer abgesaugt. Dieser wird wiederum
durch ein Überlaufrohr (15), Bild 196,
das sich in der Mitte des Schwimmergehäuses befindet,
belüftet.
2. Vergaser
Durch das Schwimmerventil (16 im Bild 192)
fließt der Kraftstoff in das Schwimmergehäuse. Hat
der KraftstoffSpiegel eine bestimmte Höhe erreicht
(Kraftstoffniveau), dann wird das Schwimmernadelventil
durch eine Blechnase (17), Bild 196,
die sich an der Halterung der Schwimmer befindet,
geschlossen.
Bei laufendem Motor wird durch das "Gasgeben"
die Teillastnadel mehr oder weniger aus der Nadeldüse
(18) herausgezogen und der Gasschieber folglich um den
gleichen Weg angehoben. Die durch den Motor angesaugte
Luft strömt durch den Ansaugkanal des Vergasers und
somit auch an dem Zerstäubungseinsatz vorbei. Dadurch
wird der Kraftstoff durch die Hauptdüse (19) und
Nadeldüse zum Ansaugkanal hochgesaugt.
Durch den Zerstäubereinsatz (18 im Bild
196) wird der Kraftstoff zerstäubt
und mit der durchströmenden Luft vermischt. Dieses
zündfähige Kraftstoff-Luft-Gemisch wird dann zum
Motor weitergeleitet.
Für ein zündfähiges Gemisch im Leerlauf sorgen einmal
die Leerlaufdüse und die vorgeschriebene Einstellung
der Leerlaufluftschraube (siehe Bild 192,
Nr. 8 und 11).
Verantwortlich für das richtige Mischungsverhältnis
zwischen Kraftstoff und Luft im Teillastbereich ist
die Nadelstellung, d.h., in welche Kerbe die
Teillastnadel in den Nadelhalter eingehängt wird.
|
Bild 192. Vergaser BVf 30 N 2-5 (StartVergaser) im Schnitt
1. | Startkolben |
2. | Dichtscheibe |
3. | Startmischrohr |
5. | Startkanal |
6. | Startdüse |
7. | Nadeldüse mit Hauptdüse |
8. | Leerlaufdüse |
9. | Leerlaufkanal |
10. | Übergangsbohrung |
11. | Leerlaufluftschraube (zur besseren Ansicht herausgedreht) |
12. | Leerlaufluftkanal |
13. | Mischluftkanal |
14. | Schieberanschlagschraube |
15. | Belüftungsrohr für das Schwimmergehäuse |
16. | Schwimmerventil |
20. | Zerstäubereinsatz |
Bild 193. Teillastnadel mit Nadelhalter
Der Nadelhalter hat außer der Fixierung
der Teillastnadel auch noch die Aufgabe, die Nadel zu
führen (obere Platte des Nadelhalters).
Für die Einstellung der Nadel ist die untere Platte
(A) des Nadelhalters maßgebend (Bild
193).
Der Nadelhalter selbst liegt plan auf dem Boden des
Gasschiebers auf. Dieser wiederum, in seiner Führung
axial verschiebbar, wird durch eine Feder, die sich an
der Verschlußkappe abstützt, in die Ausgangsstellung
(Leerlaufstellung) gedrückt. Die Federkraft wirkt der
Seilzugkraft entgegen (siehe Bild
192).
7.1.4.2. Kraftstoffniveau-Grundeinstellung
nächster Punkt ; Index
Zur Verbrennung im Motor wird ein
zündfähiges Kraftstoff-Luft-Gemisch im Verhältnis
1:15 (Mittelwert) benötigt.
Wird dieses Verhältnis verändert, z.B. durch Zufuhr
von mehr Luft (1:18), so wird das Gemisch zu arm.
Bei niedrigeren Luftanteilen, z.B. 1:13, ist es zu
fett und demzufolge schwer zündfähig.
Das im Schwimmergehäuse kanstant zu haltende
Kraftstoffniveau wird durch das Schwimmernadelventil
und den Schwimmer reguliert.
Die Einstellung des Kraftstoffniveaus trägt
wesentlich mit zur Bildung dieses
Kraftstoff-Luft-Verhältnisses bei.
|
Bild 194. Schwimmerventil geschlossen, ohne Dichtung messen
- Schließblech
Zu hoch eingestelltes Kraftstoffniveau
bedeutet - Überfettung; zu niedriges - Abmagerung.
Der Grundeinstellung des Kraftstoffniveaus kommt
deshalb große Bedeutung zu.
Bitte die Bilder 194 und 195
beachtern.
Bei der Grundeinstellung des Kraftstoffniveaus muß
immer davon ausgegangen werden, daß die Zunge (A) im Bild
194 zu der Halterung der Schwimmer
parallel stehen soll.
Eine extrem verbogene Zunge (A) bedeutet, daß die
Halterung der Schwimmer an der unteren Lötstelle
(Knickwinkel) verbogen ist. In diesem Falle müssen die
Schwimmer auf das Grundmaß 30,0 mm (bei geschlossenem
Schwimmerventil, aber nicht eingedrückter Dämpfung der
Schwimmernadel) gleichmäßig nachgerichtet werden (im
Knickwinkel, untere Lötstelle).
|
Bild 195. Schwimmerventil voll offen, ohne Dichtung messen
- Anschlagzunge
Das im Bild 194
angegebene Maß (27 mm) bedeutet voll eingefederte
Dämpfung der Schwimmernadel - eine geringfügige
Korrektur wird an der Zunge (A) durchgeführt.
Achtung:
Auf keinen Fall darf die Zunge (A) nach unten zur
Halterung der Schwimmer verbogen werden, da in
diesem Falle das Schwimmernadelventil nicht genügend
geöffnet wird und demzufolge der Kraftstoff nur
langsam nachfließen kann, was zu einer Abmagerung
bei steigenden Drehzahlen des Motors führt!
Das im Bild 195 angegebene Maß
(33mm) begrenzt den Schwimmerweg nach unten und
wird an der Anschlagzung (B) nachreguliert.
Achtung:
Der Schwimmerweg darf nicht kleiner als 6 mm sein
(Differenz zwischen 33 mm und 27 mm)!
7.1.4.3. Kraftstoffniveau-Feineinstellung
nächster Punkt ; Index
Steht kein Niveauprüfgerät zur Verfügung,
kann das Kraftsoffniveau auch direkt an dem Vergaser des
Fahrzeuges gemessen werden. Dazu benötigt man ein
gebrauchtes Schwimmergehäuse, welches an der Schmalseite,
so daß das Schwimmernadelventil sichtbar wird, mit einem
Ausschnitt 20 mm breit und 25 mm lang versehen, und mit
einer 2 mm dicken Piacrylscheibe verklebt wird. Als
Kleber ist ein Zweikomponentenkleber geeignet.
|
Bild 196. Vergaserunterteil (Schnittzeichnung), Kraftstoffniveau
15 | Belüftungsrohr für das Schwimmergehäuse |
17 | Schließblech des Schwimmerventils |
18 | Nadeldüse mit Düsenträger |
19 | Hauptdüse |
21 | Gefederte Schwimmernadel |
22 | Schwimmerventil, komplett |
Auf die eingeklebte Piacrylscheibe wird
das Maß 14 mm, von der Dichtfläche ausgehend
übertragen.
Dieses so vorbereitete Schwimmergehäuse wird mit
Dichtung an den zu messenden Vergaser angebaut.
Voraussetzung für eine einwadfreie Messung ist, daß die
Durchflußmenge des Kraftstoffes am Kraftstoffschlauch
12 l pro Stunde beträgt. der Kraftstofftank muß
mindestens zur Hälfte gefüllt sein, damit der
vorgeschrieben Druck auf das Schwimmernadelventil
vorhanden ist.
Den in der Grundeinstellung überprüften und gereinigten
Vergaser an den Kraftstoffschlauch anstecken und den
Kraftstoffhahn öffnen. Es gelangt nur soviel Kraftstoff
in das Schwimmergehäuse, bis der durch den steigenden
Kraftstoffspiegel (Niveau) angehobene Schwimmer das
Schwimmernadelventil schließt und damit die
Kraftstoffzufuhr unterbricht. Das jetzt tatsächlich im
Schwimmergehäuse vorhandene Niveau wird mit der
Markierung am Schauglas verglichen, gegebenenfalls durch
Nachjustieren der Zunge (A), Bild 194,
genau einreguliert.
Ist das Schwimmernadelventil undicht, kann man dies an
der tropfenden Belüftung (15), Bild 197,
erkennen. In diesem Falle das Ventil ausbauen und nochmals
gründlich reinigen. Ist es danach noch undicht, müß das
Schwimmernadelventil ausgewechselt werden.
Die Kraftstoffniveauhöhe beträgt 14±1 mm, von
Oberkante Schwimmergehäuse aus gemessen.
7.1.4.4. Kraftstoffniveau-Feineinstellung
nächster Punkt ; Index
Beachten!
- Die Einstellung des Vergasers darf nur bei betriebswarmen
Motor erfolgen. Das Fahrzeug muß auf einer ebenen Fläche
stehen.
- Die Leerlaufstellung des Gasschiebers ist nicht durch die
Stellschraube für den Gasseilzug einzustellen, sondern durch
die Anschlagschraube für den Gasschieber zu regulieren.
Es wird die Anschlagschraube (14) für den
Gasschieber so eingestellt, daß der Motor einwandfrei rund
läuft. Danach wird die Leerlaufluftschraube (11) ganz
hineingedreht und 1 Umdrehung wieder zurück. Durch anschließendes
langsames Hinein- und Herausdrehen der Leerlaufluftschraube wird
die höchste Motordrehzahl gesucht. Nachdem diese gefunden wurde,
ist die Anschlagschraube für den Gasschieber so einzustellen,
daß der Motor die Leerlaufdrehzahl wieder erreicht (siehe Bild
192).
Dieser Vorgang ist so lange zu wiederholen, bis sich beim
Verstellen der Leerlaufluftschraube die Motordrehzahl nicht mehr
ändert.
Ändert sich zu Beginn der Einstellung bei der Regulierung der
Leerlaufluftschraube die Drehzahl nicht, dann ist die Leerlaufdüse
verstopft.
Wird diese Einstellung richtig ausgeführt, dann wird der Motor
einen einwandfreien Übergang vom Leerlauf zum Teillastbereich
haben.
7.1.5. Ansaugstutzen
nächster Punkt ; Index
Die Aufgabe des Ansaugstutzens besteht darin,
die Lage des Vergasers zu fixieren und als Verbindungsglied
zwischen Vergaser und Einlaßkanal des Zylinders zu dienen.
Er wird mit Sechskantmuttern und Stiftschrauben am Zylinder
befestigt.
Um die Wärme des Zylinders nicht auf den Vergaser zu
übertragen, werden zwischen dem Ansaugstutzen und dem
Zylinder ein Plastflansch und zwei Dichtungen (vor und nach
dem Plastflansch) beigelegt.
7.2. Fehlersuche
7.2.1. Abmagerung
nächster Punkt ; Index
Die Erkennungsmerkmale für die Abmagerung des
Kraftstoff-Luft-Gemisches sind:
- Starker Abbrand der Elektroden der Zündkerze;
- An der Zündkerze sind Schmelzperlen;
- Im Bereich von Halb- bis Vollgas wird eine zu
niedrige Leistung vom Motor abgegeben;
- Der Motor neigt zum Festgehen.
Fehler bzw. Schäden, die zur Abmagerung des
Gemisches führen und deren Behebung:
- Luftfilter sitzt nicht einwandfrei im Zentrierrand
des Ansauggeräuschdämpfergehäuses
- Luftfilter ausbauen und wieder einwandfrei in den
Zentrierrand einlegen.
- Luftfilter wurde durch unsachgemäße Behandlung
beschädigt
- Luftfilter durch neues ersetzen.
- Dichtungen zwischen Luftfiltergehäuse und
Ansauggeräuschdämpfer bzw. zwischen Luftfiltergehäuse
und Rahmen defekt
- Dichtungen erneuern oder Schraubverbindungen
nachziehen.
- Dichtung zwischen Luftfiltergehäuse und
Verschlußdeckel fehlt oder ist beschädigt
- Dichtung ergänzen oder erneuern.
- Anschlußstück zum Vergaser ist beschädigt bzw.
porös oder es sitzt nicht einwandfrei in der
Bohrung des Ansauggeräuschdämpfergehäuses
- Anschlußstück gegen ein neues austauschen
oder richten.
- Ansaugstutzen porös
- Ansaugstutzen durch einen neuen austauschen
oder wenn möglich, mit Kunstharz abdichten.
- Isolierflansch gerissen oder porös;
Dichtung beschädigt
- Teile sind gegen neue auszutauschen
- Zu geringe Kraftstoffzufuhr durch:
- verschmutzten Kraftstoffhahn,
- zusammengedrückte Gummidichtscheibe,
- verhärtete oder defekte Kraftstoffleitung,
- verschmutztes Entlüftungsloch im Tankdeckel
- der Kraftstoffhahn ist abzubauen und seine
Teile sind einzeln zu säubern.
- defekte oder verhärtete Kraftstoffleitungen
und die beschädigte Gummidichtung sind gegen
neue auszutauschen.
- die Bohrung im Tankdeckel ist mit Druckluft
auszublasen.
- Teillastnadel hängt zu tief
- Die Teillastnadel ist eine oder mehrere
Kerben höher zu hängen, bis ein normales
Mischungsverhältnis erreicht ist.
- Zentralschwimmer ist verbogen - Schwimmerventil
wird nicht genügend geöffnet
- Zentralschwimmer einstellen.
- Schwimmernadel hängt
- Schaft der Schwimmernadel und die
Durchgangsbohrungen des Ventilkörpers
polieren,
- Ventil auf evtl. vorhandene Fremdkörper
untersuchen,
- Schwimmernadel und Ventilsitz gegen
neue Teile austauschen.
7.2.1. Überfettung
nächster Punkt ; Index
Die Erkennungsmerkmale für die Überfettung des
Kraftstoff-Luft-Gemisches sind:
- Motor läßt sich schwer starten;
- Motorleistung sinkt mit zunehmender Erwärmung
des Motors;
- Hoher Verbrauch;
- Neigung zum "Viertakten";
- Zündkerze mit vorgeschriebenem Wärmewert
verölt;
- Starke sichtbare Rauchfahne im betriebswarmen
Zustand.
Fehler bzw. Schäden, die zur Überfettung des
Gemisches führen und deren Behebung:
- Trockenluftfilter ist überaltert (mehr als 10000 km
Fahrstrecke)
- Luftfilter gegen ein neues auswechseln.
- Trockenluftfilter naß
Ursache: Luftfiltergehäuse undicht - Wassereinbruch
- Luftfilter trocknen, erforderlichenfalls
auswechseln.
- Teillastnadel hängt zu hoch
- Teillastnadel ist eine oder mehrere Kerben
tiefer zu hängen, bis ein normales
Mischungsverhältnis erreicht ist.
- Verschleiß der Nadeldüse und Teillastnadel (über
20000 km Fahrstrecke)
- Beide Teile sind durch neue zu ersetzen.
- Schwimmerventil undicht
Ursache:
- Ventil verschmutzt,
- Schwimmernadel ausgeschlagen
- Schwimmerventil säubern,
- neue Schwimmernadel einbauen.
- Zentralschwimmer ist verbogen - Schwimmerventil
bleibt zu weit offen
- Zentralschwimmer einstellen.
- Hauptdüse zu groß
- Andere Hauptdüse mit gleichem
aufgedrucktem Maß verwenden
(Düsen mit gleichem Nennmaß sind
durch die Toleranzen unterschiedlich),
- bringt das keinen Erfolg, dann die
nächst kleinere Düse einbauen.
- Dichtung am Startkolben ist beschädigt
- Dichtung gegen eine neue auswechseln.
- Feder für Startkolben hat eine zu geringe Vorspannung
- Feder gegen eine neue austauschen.
- Hülle des Seilzuges für Starteinrichtung
ist ohne Spiel; dadurch kann der Startkolben
das Startmischungsrohr nicht einwandfrei
abdichten
- Seilzughülle auf etwa 1 mm Spiel einstellen.
8. Spezialwerkzeuge
nächster Punkt ; Index
|
Bild 197. Spezialwerkzeugsortiment ETZ 250
8.1. Verzeichnis der Spezialwerkzeuge
nächster Punkt ; Index
| | Ersatzteil- Bestell- Nr. | Zeich- nungs- Nr. |
1 | Motoren-Montagevorrichtung | 22-50.014 | 1a |
| Klemmstück hinten1) | 89-99.321 | 1b |
| Klemmstück vorn vollständig1) | 89-99.322 | 1c |
2 | Zentrierbolzen für Schwinge (05-MW 26-4) | 89-99.055 | 2 |
3 | Abziehvorrichtung für Lager im Steuerkopf | 22-51.006 | 3 |
4 | Montagevorrichtung für Gummilagerung Schwinge | 22-51.445 | 4 |
5 | Spreizdorn für Radlager (H 8-820-3) | 89-99.090 | 5 |
6 | Montageaufnahme für Getriebesatz | 29-50.011 | 6 |
7 | Meßeinrichtung für Axialspiel Kupplungsmitnehmer (05-ML 13-4) | 89-99.117 | 7 |
8 | Kupplungsspannvorrichtung (05-MV 150-2) | 89-99.071 | 8 |
9 | Gegenhalter für Getriebekettenrad (05-MW 45-3) | 89-99.057 | 9 |
10 | Abzieher für Antriebsrad (05-MV 45-3) | 89-99.064 | 10 |
11 | Ausdrückvorrichtung für Kolbenbolzen | 22-50.010 | 11 |
12 | Kolbenunterlage | 22-50.412 | 12 |
13 | Zündeinstellehre | 29-50.801 | ohne |
14 | Ankerabziehschraube (02-MW 39-4) | 89-99.026 | 13 |
15 | Schlagdorn für Paßhülsen (11-MW 3-4) | 89-99.072 | 14 |
16 | Führungsdorn für Kolbenbolzen (05-MW 19-4) | 89-99.051 | 15 |
17 | Schlagdorn für Lager 6203 und 6204 (11-MW 7-4) | 89-99.073 | 16 |
18 | Schlagdorn für Lager 6306 | 29-50.405 | 17 |
19 | Montagewerkzeug für Dichtring 30x72x7 Lichtmaschinenseite | 29-50.406 | 18 |
20 | Montagewerkzeug für Dichtring 30x72x7 Kupplungsseite | 29-50.409 | 19 |
21 | Montagebrücke | 22-50.430 | 20 |
22 | Kugellagerabzieher (Lager 6306) | 22-50.431 | 21 |
23 | Abziehhülse (Kupplung-Gewinde M 24x1,5) | 22-50.435 | 22 |
24 | Druckspindel mit Druckstück | 22-50.437 | 23 |
25 | Abziehschraube Lager 6203 | 22-50.438 | 24 |
26 | Spannpatrone | 22-50.439 | 25 |
27 | Montageschlüssel für Teleskopgabel (19-MW 22-1) | 89-99.136 | ohne |
| Distanzstück | nicht im Sortiment | 26 |
| Kolbenringzange (05-MW 141-4) | 89-99.124 | 27 |
| Spannring (05-MW 147-4) | 89-99.128 | 28 |
| Spezialschlüssel für Stoßdämpfer (05-MW 82-4) | 89-99.059 | 29 |
1)zur Nachrüstung von bis 1980 erworbenen Motoren-Montagevorrichtungen für den Motor der ETZ 250 |
8.2. Zeichnungen für Spezialwerkzeuge
nächster Punkt ; Index
1. Motoren-Montagevorrichtung 22-50.014
nächster Punkt ; Index
Alle bis 1980 von MZ verkauften
Montagevorrichtungen können nicht für das Einspannen
des Motors EM 250 verwendet werden.
Der MZ-Ersatzteilvertrieb bietet für das Umrüsten
dieser älteren Vorrichtungen den Bezugsberechtigten für
Spezialwerkzeuge Umrüstsätze an, bestehend aus
Klemmstück hinten 89-99.321 und
Klemmstück vorn vollständig 89-99.322
Außerdem muß die Einspannstelle vorn
an der Vorrichtung 22-50.014 nach Zeichnung 1a
umgearbeitet werden, was mit Werkstattmitteln ohne
weiteres möglich ist.
|
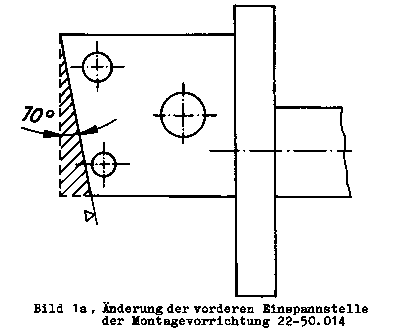
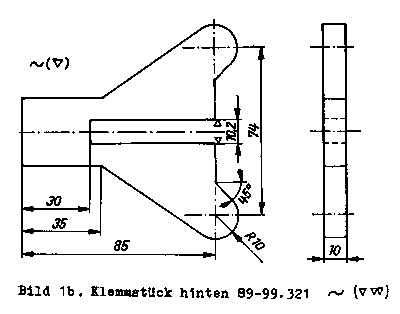
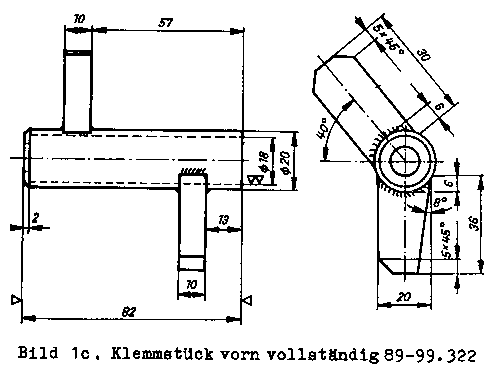
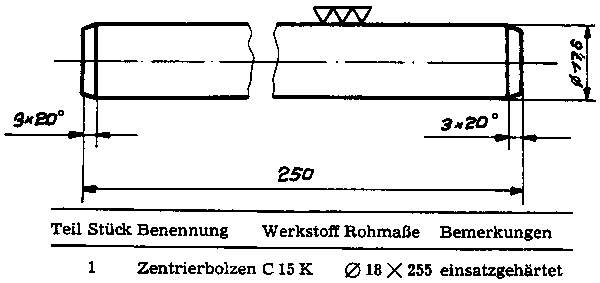
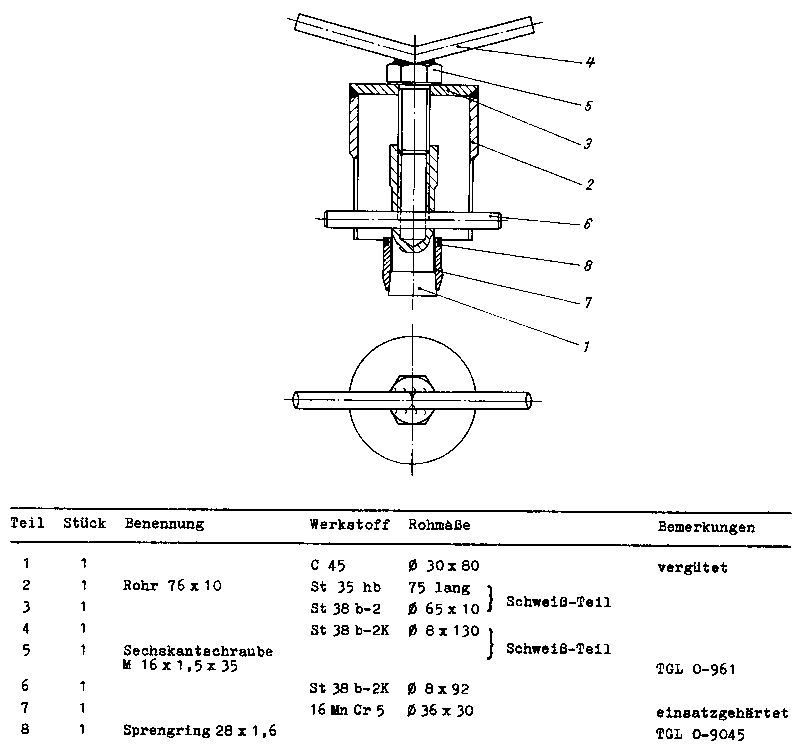
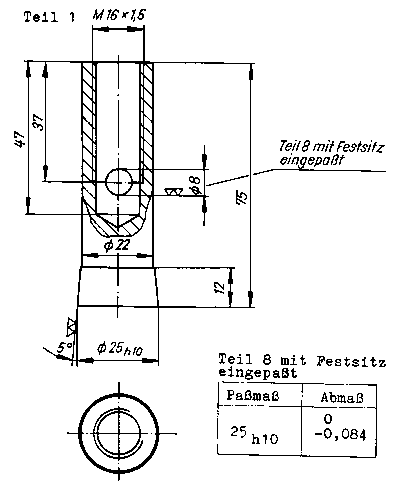
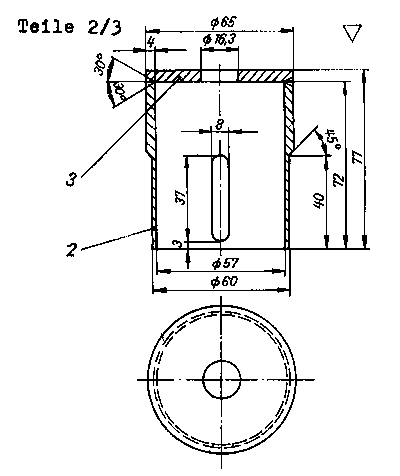
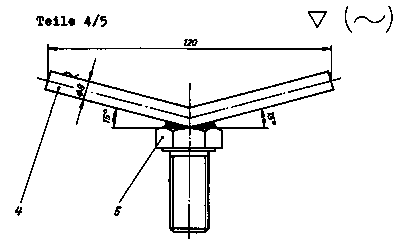
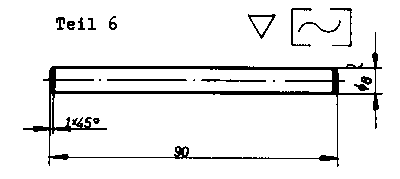
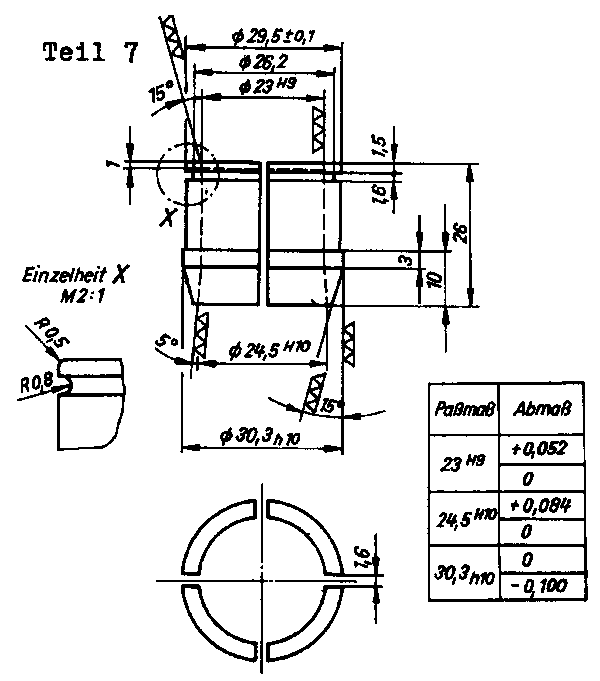
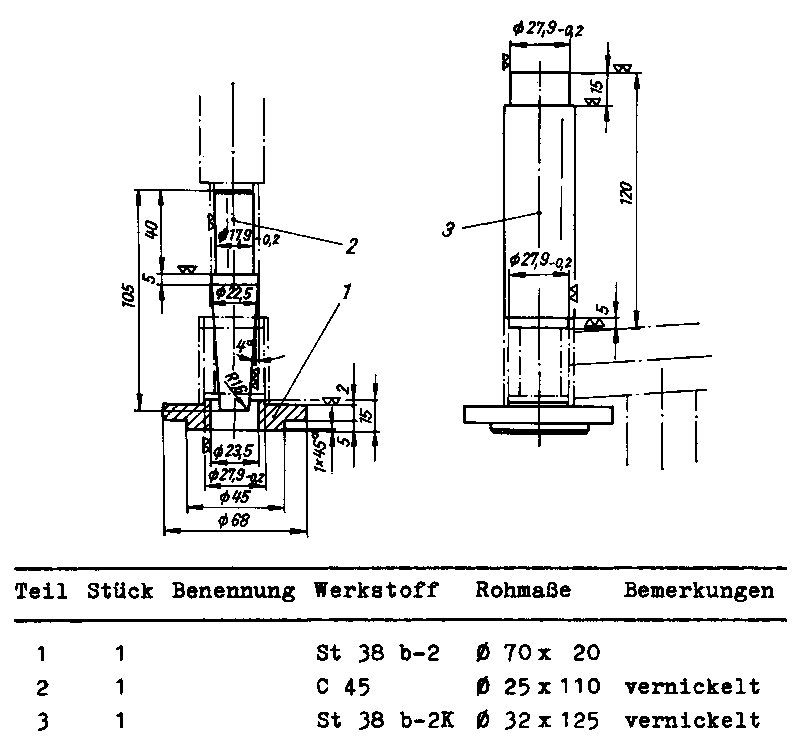
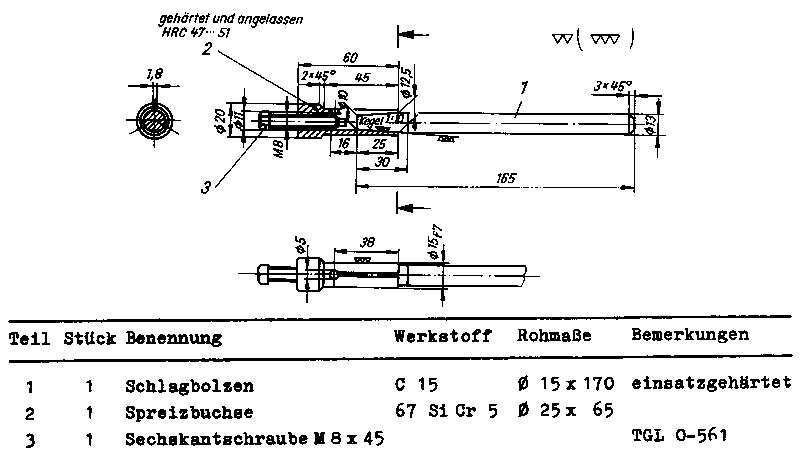
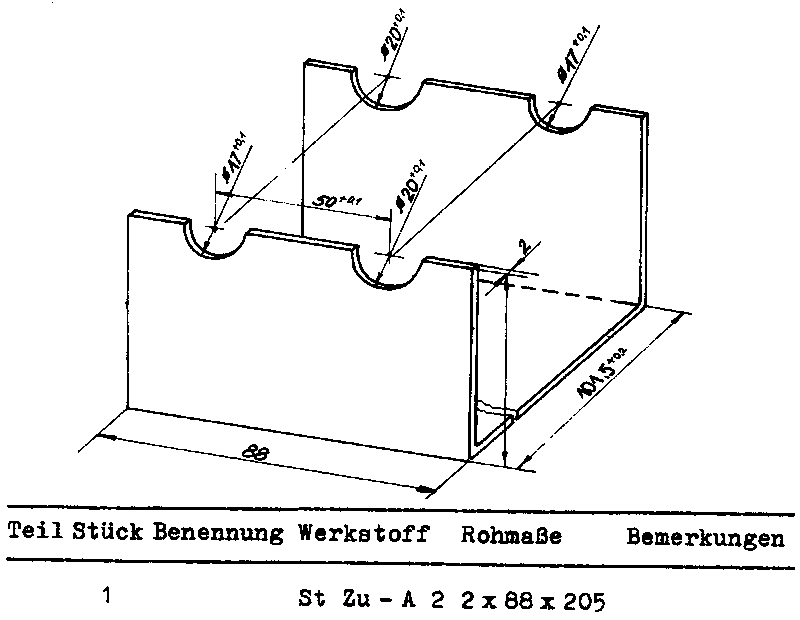
7. Meßeinrichtung für Axialspiel Kupplungsmitnehmer (05-ML 13-4) 89-99.117
nächster Punkt ; Index
|

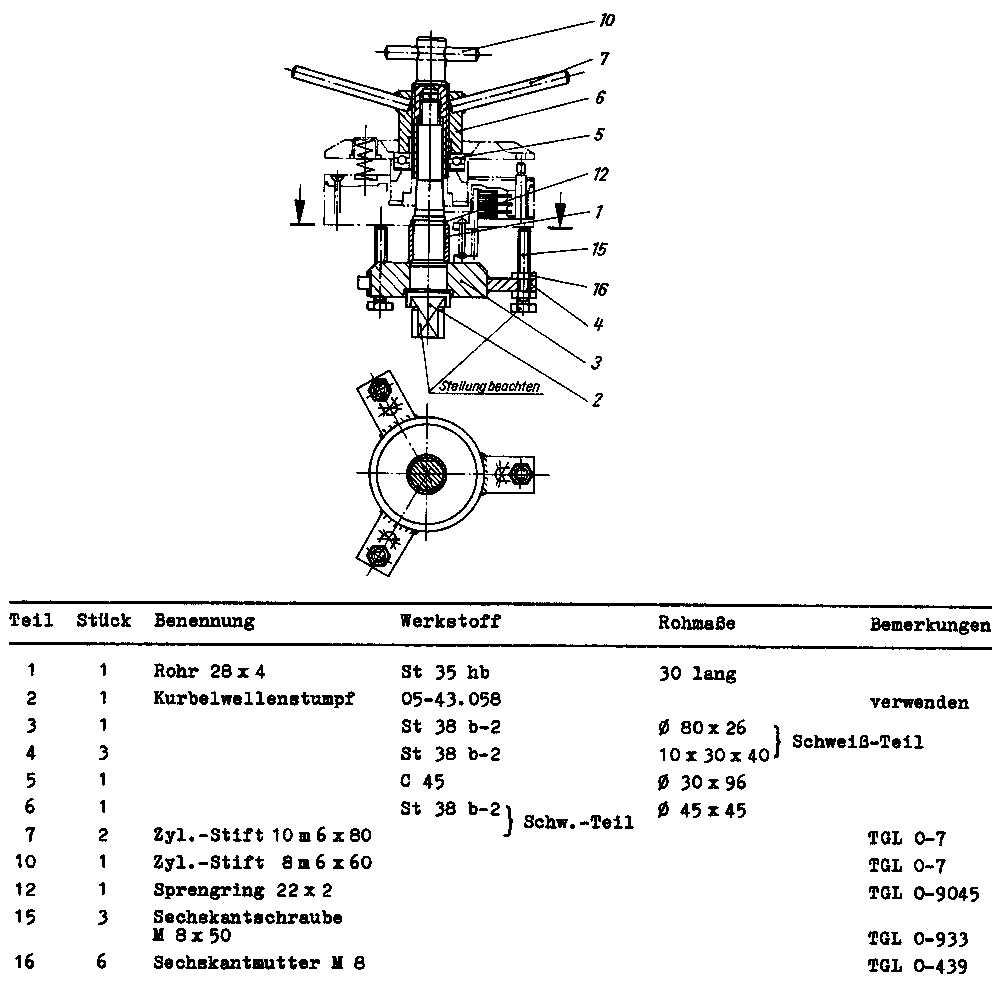
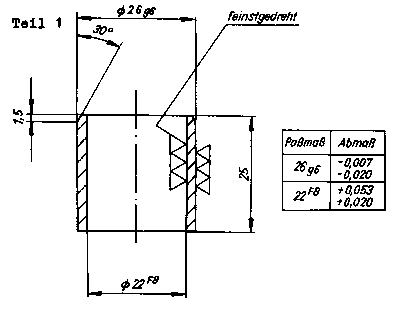
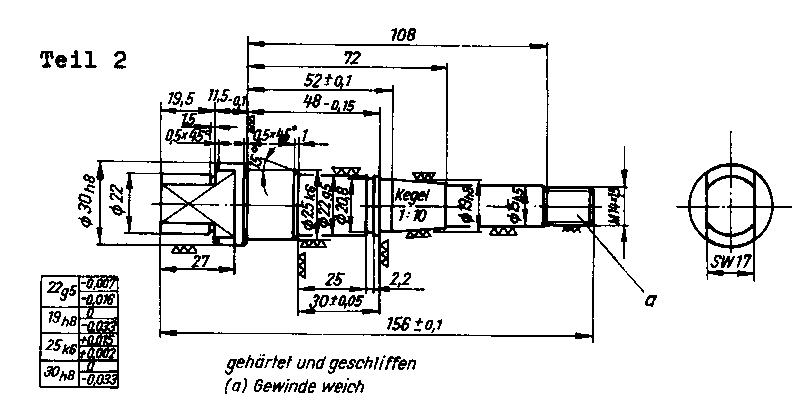
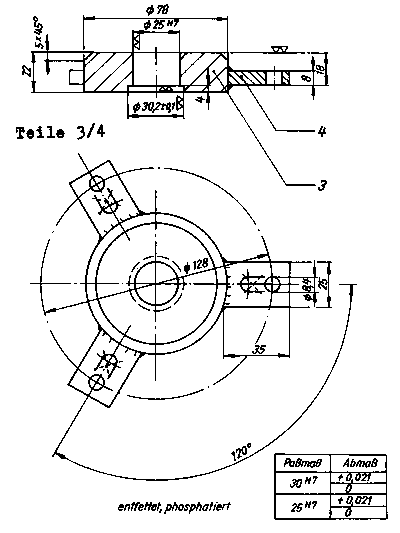
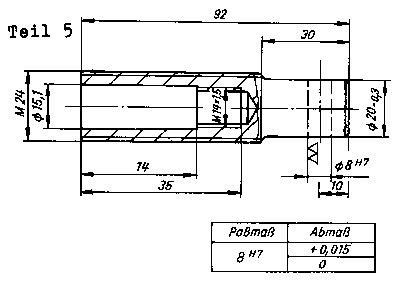
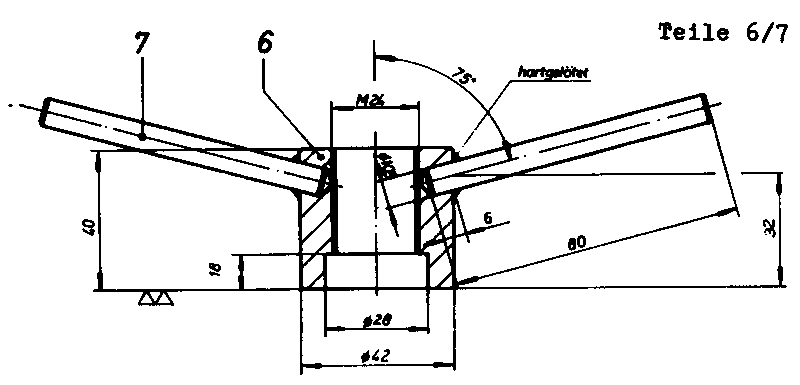
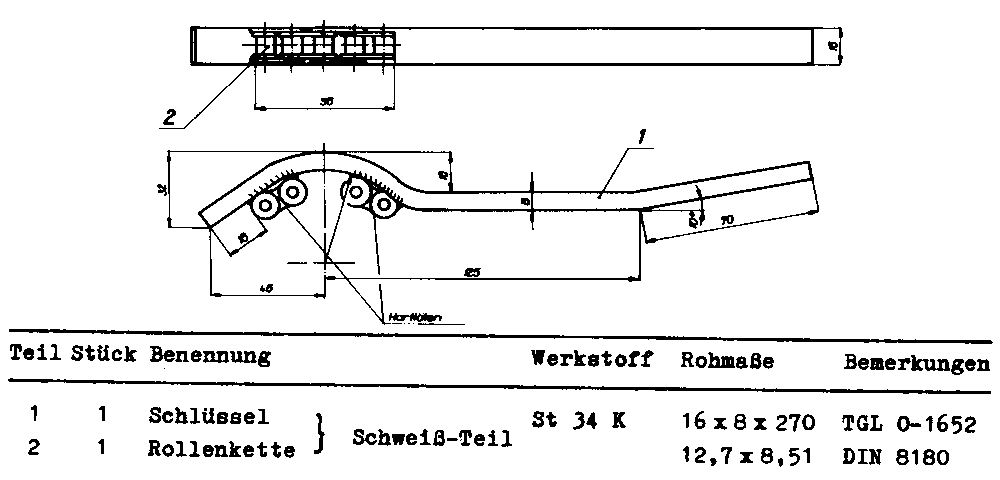
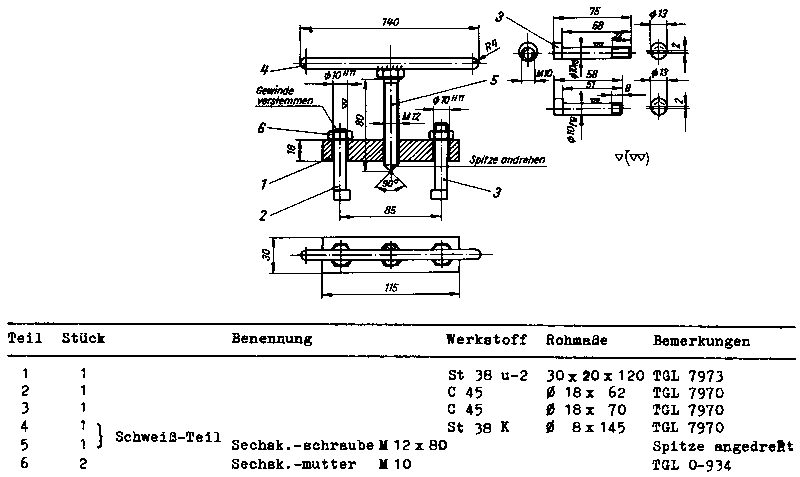
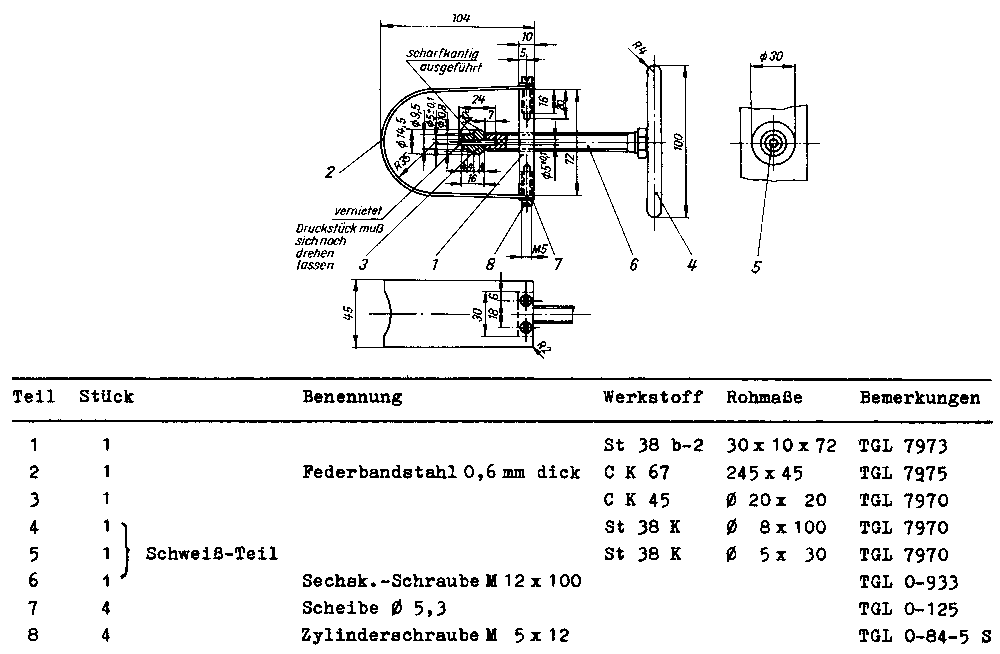
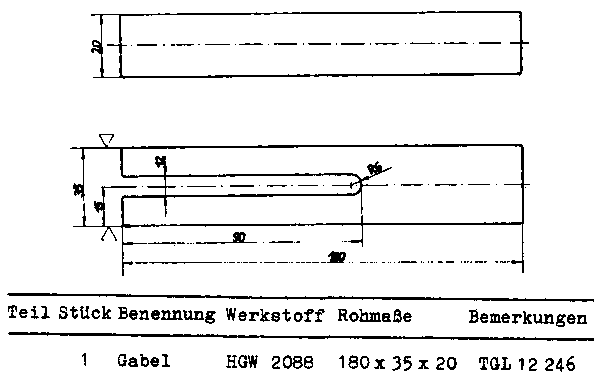
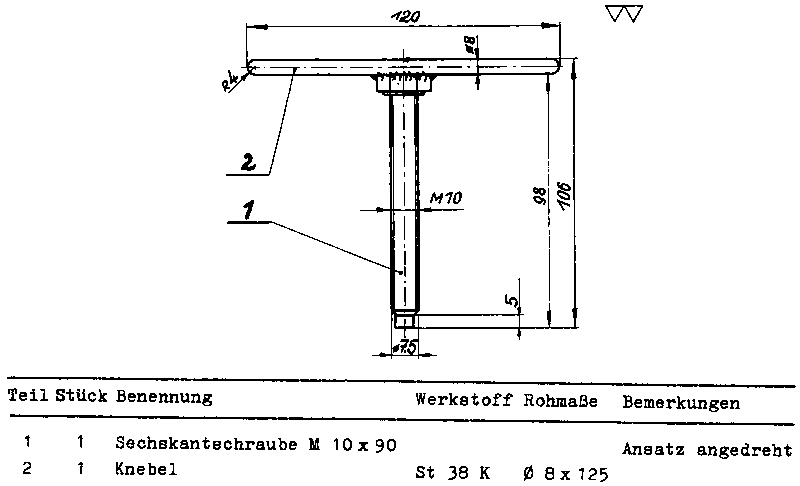
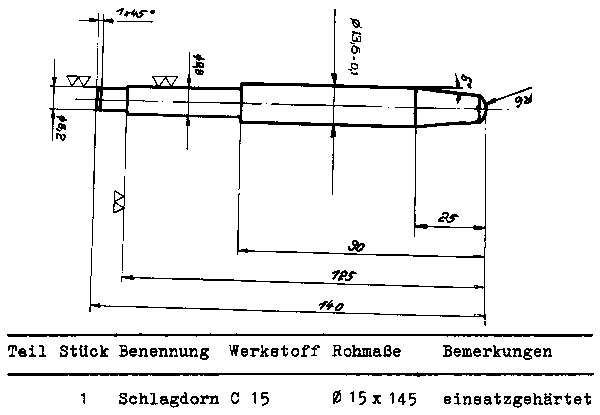
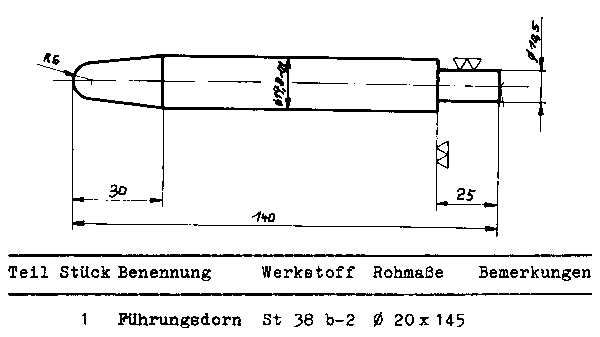
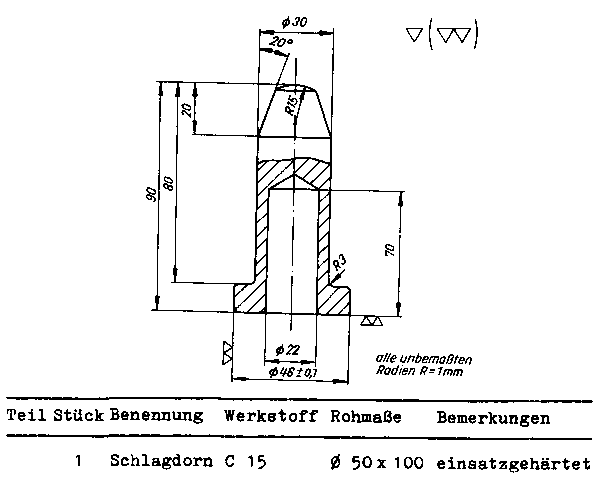
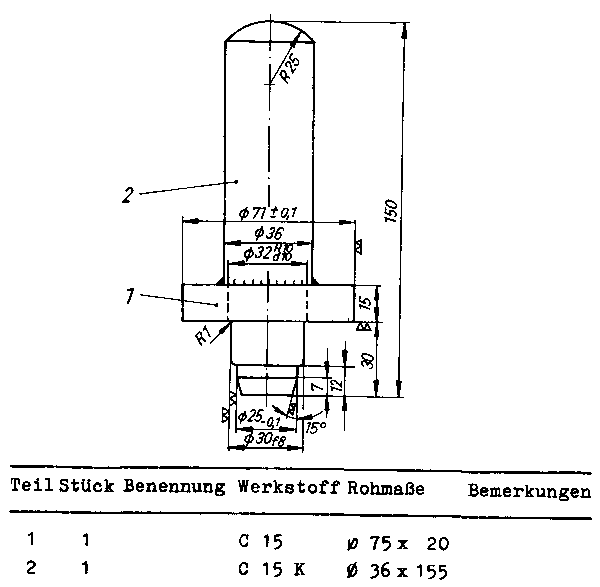
18. Montagewerkzeug für Dichtring (30x72x7) 29-50.406 (Lichtmaschinenseite)
nächster Punkt ; Index
|
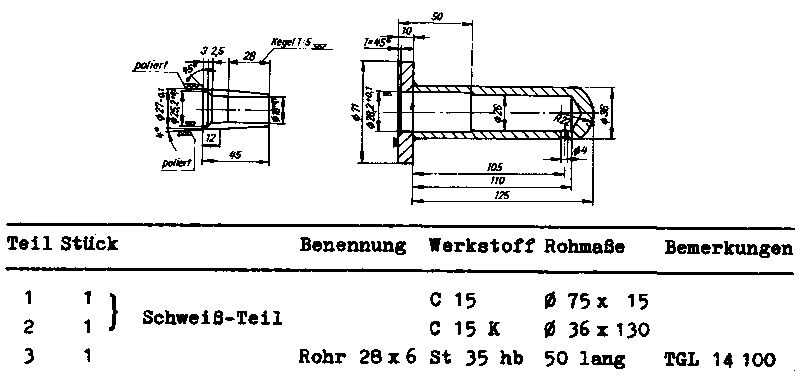
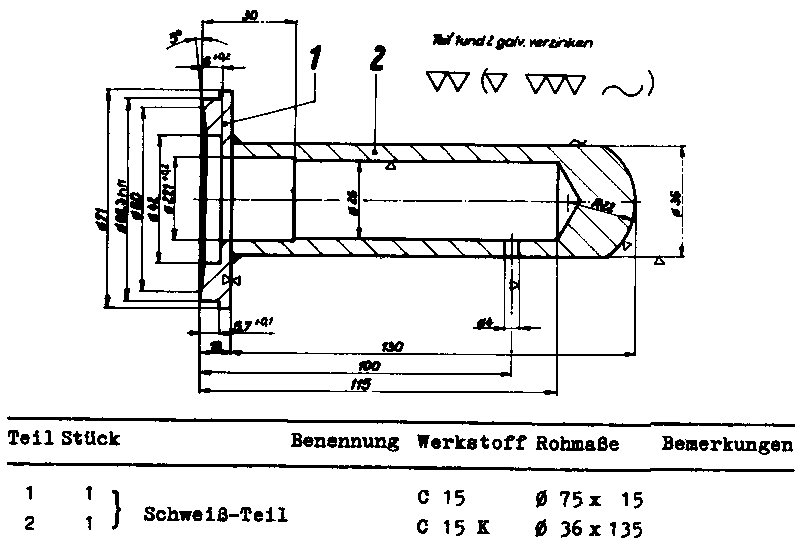
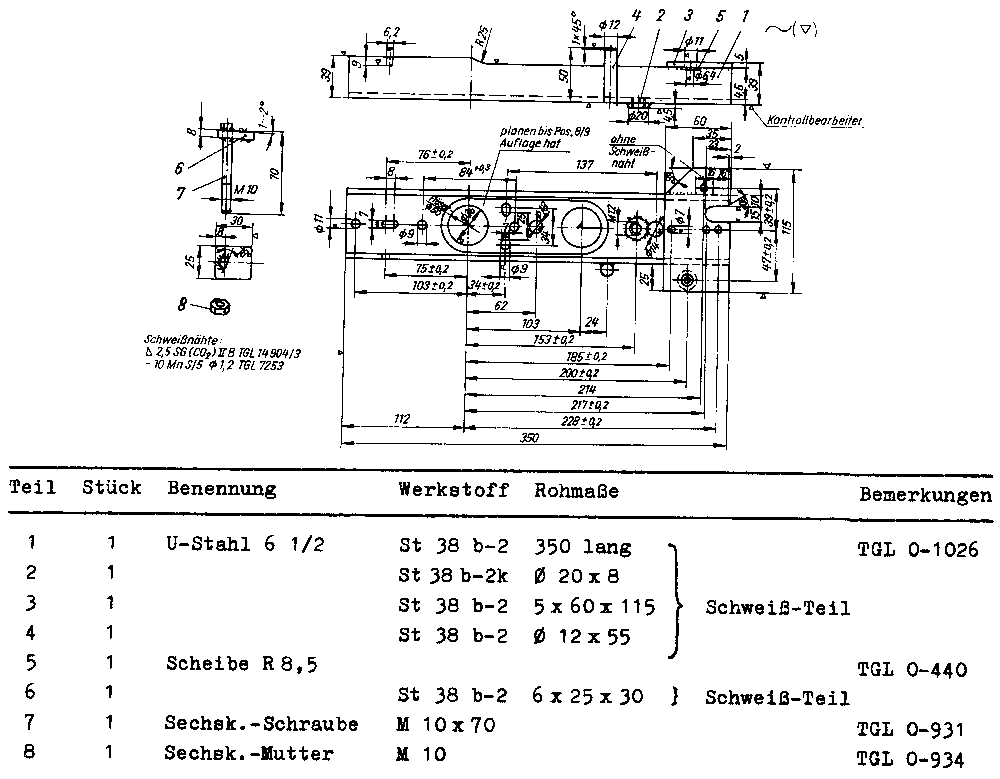

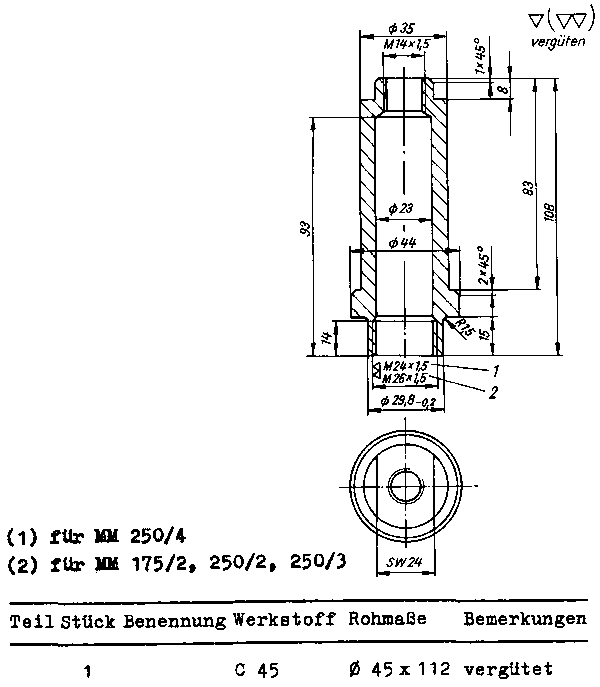
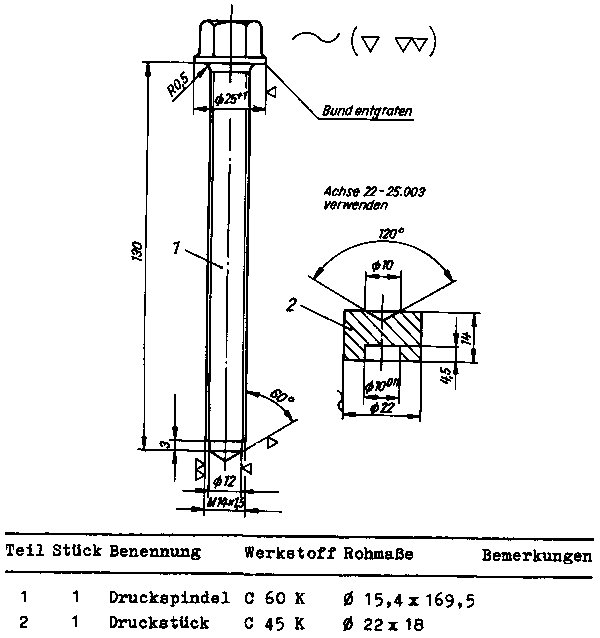
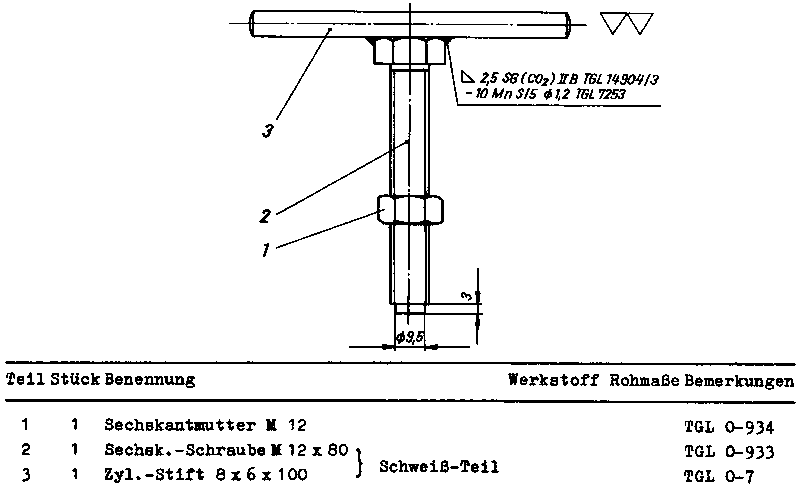
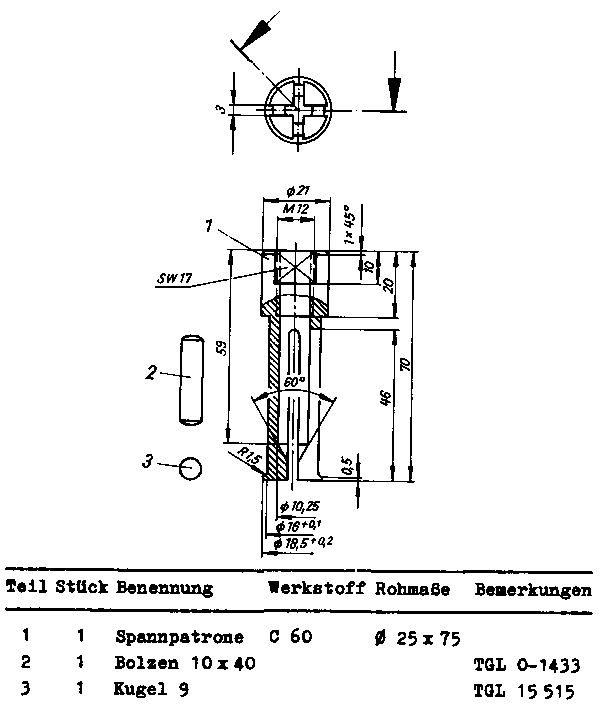
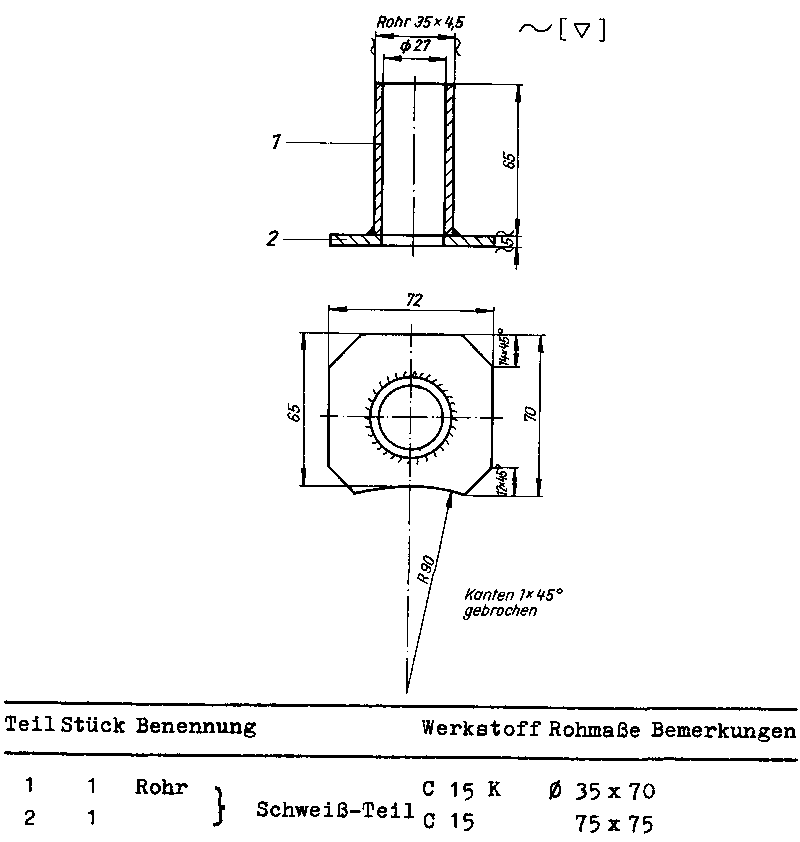

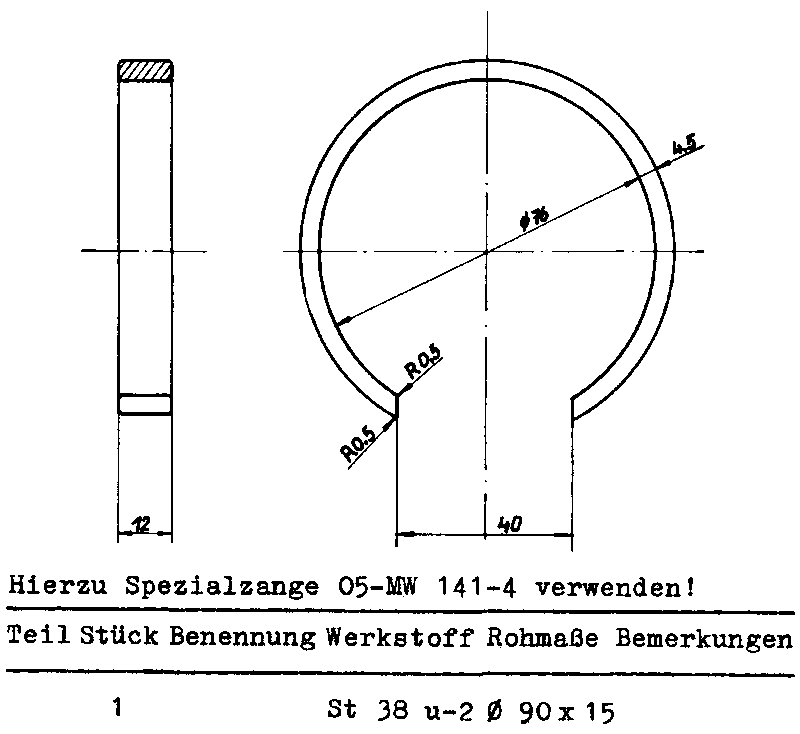
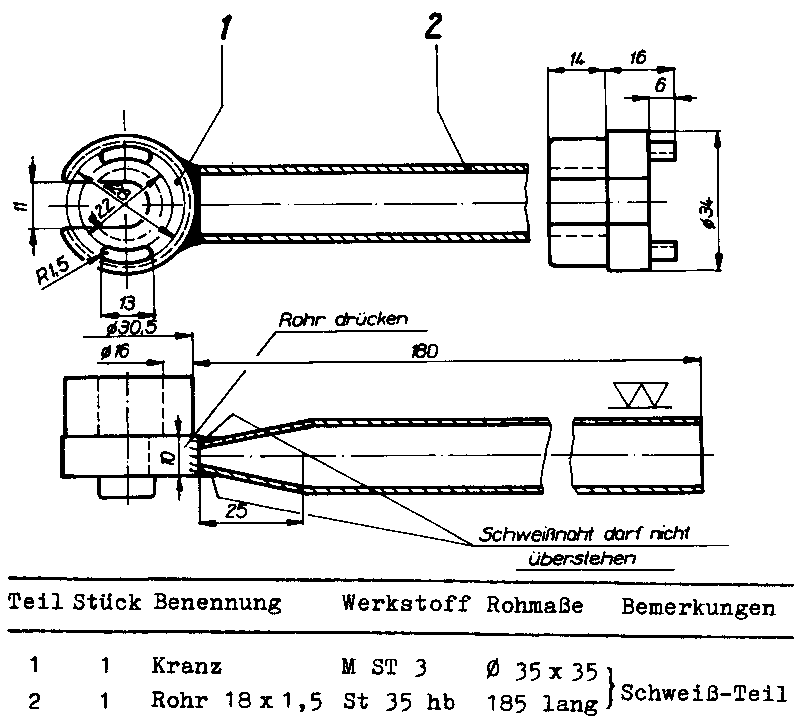
9. Anzugsmomente - Motor
nächster Punkt ; Index
Muttern für den Zylinderkopf | 26 Nm (2,6 kpm) |
Zündkerze | 40 Nm (4,0 kpm) |
Zylinderschrauben für Gehäuse Lichtmaschinen- und Kupplungsdeckel | 13 Nm (1,3 kpm) |
Schrauben für Dichtkappe Abtriebswelle | 5 Nm (0,5 kpm) |
Schrauben für Haltekappe-Lichtmaschine | 5 Nm (0,5 kpm) |
Schraube für Ankerbefestigung (Lichtmaschine) | 20 Nm (2,0 kpm) |
Stiftschrauben für Zylinderbefestigung | 20 Nm (2,0 kpm) |
Mutter für Kupplungsbefestigung | 80...100 Nm (8...10 kpm) |
Mutter für Antriebsrad 68 Zähne | 60 Nm (6,0 kpm) |
Mutter für Kettenritzel am Getriebe | 60 Nm (6,0 kpm) |
Schrauben für Abschlußkappe im Kupplungsdeckel bzw. Drehzahlmesserantrieb | 8 Nm (0,8 kpm) |
10. Anzugsmomente - Fahrgestell
nächster Punkt ; Index
Mutter für Steuerrohr | 150 Nm (15,0 kpm) |
Verschlußschrauben für Telegabel | 150 Nm (15,0 kpm) |
Klemmschrauben am unteren Klemmkopf - Telegabel | 20 Nm (2,0 kpm) |
Innensechskantschrauben für Instrumentenhalter | 20 Nm (2,0 kpm) |
Klemmschraube-Vorderradachse | 20 Nm (2,0 kpm) |
Vorder- und Hinterradachse | 80 Nm (8,0 kpm) |
Mutter für Flanschbolzen - Hinterradantrieb | 80 Nm (8,0 kpm) |
Federbeinbefestigung oben | 26 Nm (2,6 kpm) |
Federbeinbefestigung unten | 45 Nm (4,5 kpm) |
Motorbefestigung hinten | 26 Nm (2,6 kpm) |
Motorbefestigung am Gummielement (Zylinderkopf) | 26 Nm (2,6 kpm) |
Auspuffrohrbefestigung am Zylinder | 150 Nm (15,0 kpm) |
Befestigungsschrauben M 8 für Auspuff | 26 Nm (2,6 kpm) |
Schwingenlagerbolzen (voll ausgefedert) | 70...80 Nm (7,0...8,0 kpm) |
Beilageblatt - Schaltplan
Index
|
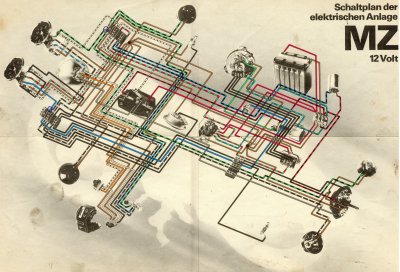
Index